Boeing-Rolls Short-Inlet Flight Tests Show Potential To Cut Big Fan Drag
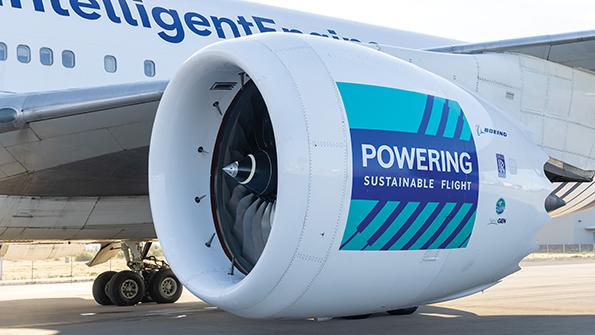
The heavily instrumented inlet was tested at angles of attack in excess of 27.8 deg.
The bigger the fan and bypass ratio of a turbofan, the quieter and more efficient the engine. But these benefits diminish as increased nacelle weight and drag degrade the fuel-burn advantages of the larger bypass.
To help counter this conundrum, Rolls-Royce and Boeing teamed up under the second phase of the FAA’s Continuous Lower Energy, Emissions and Noise (CLEEN) environmental research program to flight-test a shorter and lighter inlet. The newly revealed results of the six-year program show the potential for significant benefits with fuel savings of about 0.5% and weight savings in excess of 350 lb. per shipset for a typical widebody application.
- Inlet could cut fuel burn by 0.5%
- UltraFan is to use shorter inlet
Shortening an inlet is challenging: It must retain sufficient length to operate efficiently over the entire flight envelope of the aircraft and to channel freestream airflow evenly to the fan and compressor regardless of different speeds, altitudes and maneuvers at high angles of attack or sideslip. The inlet design is therefore critical to engine performance, and any change to the profile of the lip and distance to the fan face must be carefully considered to avoid distorting the flow into the engine or reducing the total pressure recovery of the compressor.
“The short inlet, in essence, performed to design intent,” says Ash Owen, chief engineer for civil technology programs at Rolls-Royce. “The fan was free of aerodynamic instabilities at all conditions, and the fan blade vibration levels remained as baseline. So for both the key requirements that we were evaluating the short inlet for it was fine.”
Flight tests took place in late 2022 using Rolls-Royce’s Boeing 747-200 flying testbed and formed the culmination of the three-phase program, which began in 2016 with design and analysis of the short inlet on a 112-in.-dia.-fan Trent 1000. Ground tests followed in 2018 at Rolls-Royce’s facility at the NASA John C. Stennis Space Center and compared the short and baseline nacelles over a series of crosswind runs.
“It was very successful,” Owen says. “So much so that we took the decision with Boeing that it would be a good idea to go to the next step and fly it. The short inlet—reduced in length by around 50% compared to the standard unit—was fitted to the heavily instrumented Trent 1000 for the test program, which amassed almost 7.5 hr. of flight time.
“We did takeoff work, cruise, and importantly, we did high-angle-of-attack work,” Owen continues. “We were particularly interested to see if we were going to get any undesirable lip flow interaction. We didn’t at all, and the results compared with a flight with the baseline inlet.” Testing included taking the engine to a maximum angle of attack of more than 27.8 deg. at the inlet.
“We did three short-inlet flights and one baseline flight because we also had, of course, all of the Trent 1000 certification data we could use as well for the baseline,” Owen says. “The aerodynamic performance was as we expected, and that’s particularly crucial for us because we wanted to compare it back to the computational fluid dynamics analysis. Also the fan blade vibration levels were similar to the baseline and acceptable.”
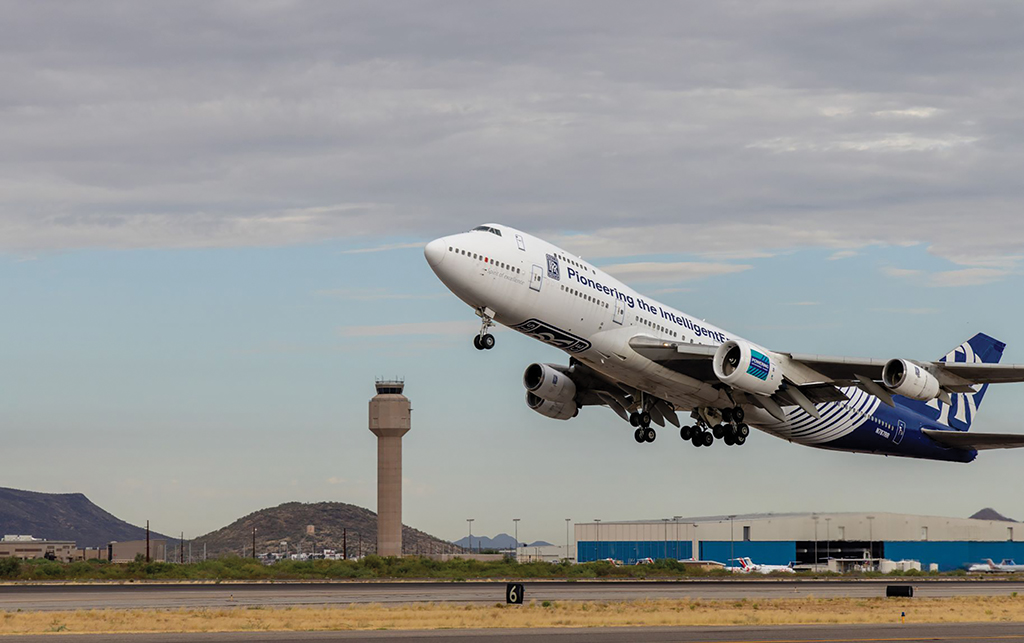
According to Rolls-Royce’s assessment, the short inlet has now been demonstrated for a Trent-type application to TRL 6, a technology readiness level in a relevant environment that prepares the way for full-scale development. Boeing’s evaluation of the lighter structure and reduced wetted area of the nacelle indicates potential fuel-burn savings of up to 0.5%.
The program clears the way for Boeing to consider shorter inlets for future products or reengining, although that would require further tests for the impact on fan noise—much of which in current engines is absorbed by special surface treatments in the inlet area.
“Clearly, we expect short-inlet technology to be required for the UltraFan,” Owen says, referring to the company’s next-generation geared turbofan—the demonstrator for which is poised to begin ground tests. “That’s the next stage of the journey from our perspective. We would anticipate short-inlet technology being required for an engine the size of UltraFan purely because the fan diameters are so great.”
The CLEEN effort is therefore seen as de-risking the short inlet for the UltraFan, but more study work will be needed for flow interaction with the larger engine’s slower-speed advanced fan. “From the work we’ve done, we see no problems going into the UltraFan,” Owen says.
The Boeing-Rolls work under CLEEN comes after Pratt & Whitney also evaluated a short-inlet design for the smaller PW1100G geared turbofan during an earlier phase of the FAA program.