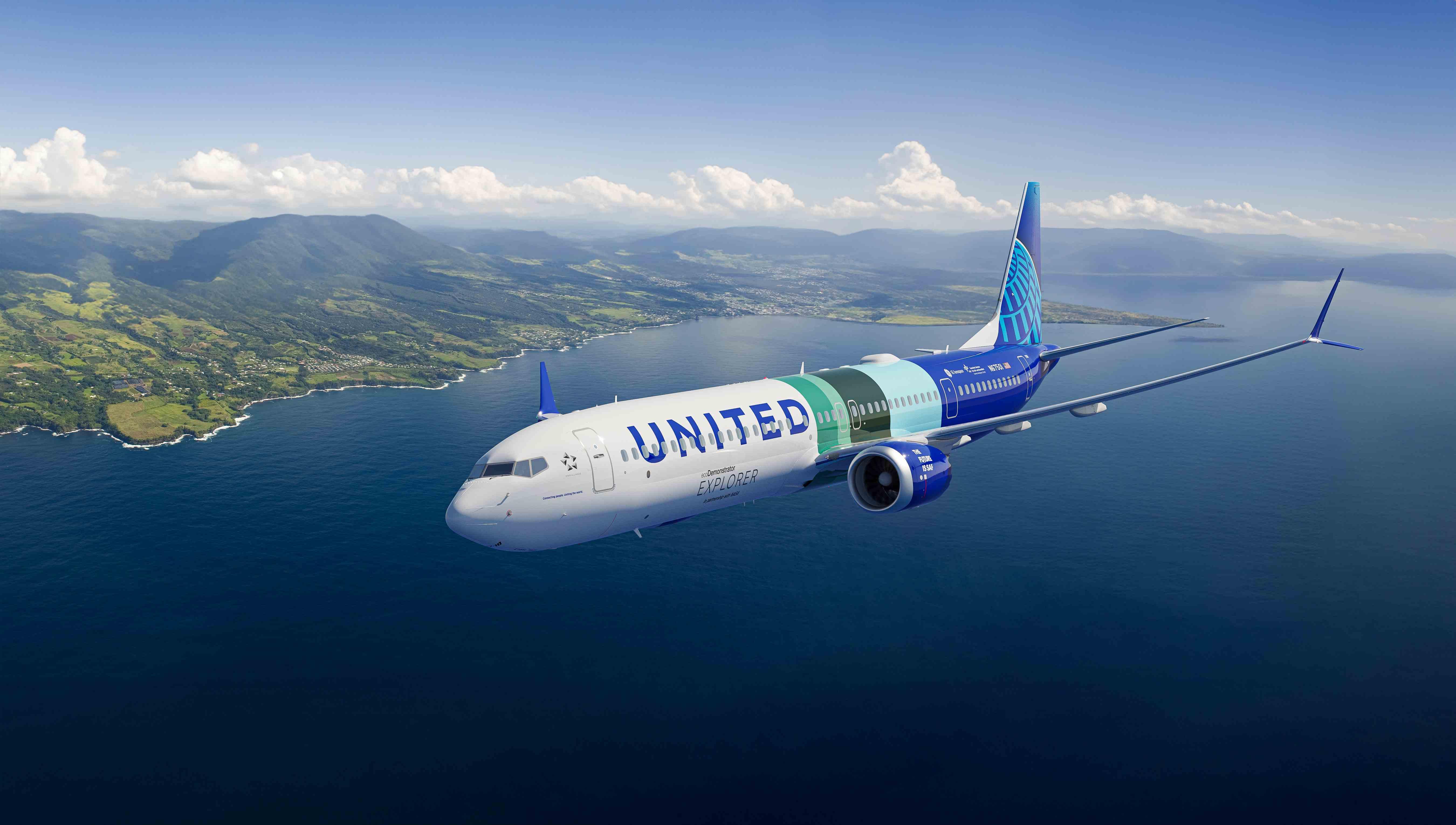
Boeing, NASA and United Airlines have launched a ground- and flight-test program aimed at evaluating the non-carbon emissions of sustainable aviation fuels (SAF), as well as the impact of the new fuel on the formation of condensation trails—usually called contrails.
The three-week program forms the latest phase of Boeing’s recently launched ecoDemonstrator Explorer series and involves a 737-10 destined for United, as well as NASA’s DC-8 airborne science lab aircraft. For the flight-test segment, the sensor-equipped DC-8 will fly behind the 737 to measure the emissions and contrail ice particles.
Contrails occur when water vapor and particles in the aircraft engine exhaust mix with cold, humid air at high altitude and, in certain atmospheric conditions, produce persistent clouds known as aircraft-induced cirrus. In some cases contrail cirrus can persist for hours, and these are estimated to contribute more than half of aviation’s climate-warming effect.
Researchers believe that SAF could potentially reduce the formation of persistent contrails. This is because SAF lacks aromatic and sulfur components which—in conventional fuels—form the exhaust particulates around which water can condense at high altitudes. In jet fuel, these particles are mostly composed of sulfates, nitrates, carbon and ash.
For United, the program marks its first major involvement in Boeing’s ecoDemonstrator initiative and another element of its increasing strategic investment toward net-zero carbon emissions by 2050. “We know that contrails have climate impact. What we have not yet rooted in science is how much,” says Lauren Riley, United's chief sustainability officer. “Until we get to the bottom of that scientific question, we're not really going to be able to come up with solutions that can address the problem.”
“What we're testing in this partnership is do you avoid [persistent] contrail formation altogether if you're able to fly one day on 100% SAF that has no aromatics? We're not going to see that today—we certainly are not approved to have 100% SAF, but we could by decade-end or into the next if there's enough supply that comes online and the engines' manufacturers declare they can handle it,” she adds.
For the flight-test experiment, the 737 will fly through an air mass conducive to contrail formation using two fuel types. The fuel tanks in the wings will hold a conventional low-sulfur Jet A, and the center tank will contain 100% SAF provided by California-based World Energy. The DC-8, following in trail, will be used to sample and measure the contrail formed by the 737 with conventional fuel before it switches to burning SAF—in this case, a HEFA-SPK (synthetic paraffinic kerosene produced via the hydroprocessed esters and fatty acids pathway).
The project is the latest phase in a multi-year partnership between Boeing and NASA focused on how SAF can reduce emissions and enable other environmental benefits. Compared to conventional jet fuel, SAF—made from a range of sustainably produced feedstocks—can reduce emissions by up to 85% over the fuel’s life cycle and offers the largest potential to reduce aviation carbon dioxide over the next 30 years.
The flight-test program follows ground testing on an SAF-fueled Alaska Airlines 737-9 in 2021, as well as flight tests on the 777-200ER and 787-10 ecoDemonstrator aircraft in 2022. Other test participants include GE Aerospace, one half of the CFM International joint venture—along with Safran—that produces the Leap 1B engine powering the 737-10. Also involved is the FAA, as well as the German aerospace center DLR, which, along with Airbus and Rolls-Royce, has been studying SAF and contrail formation under the European ECLIF3 study.
Rich Moore, a physical research scientist from NASA Langley Research Center, Virginia, says the flight-test effort is a natural follow-on to the recent ground tests, particularly the CFM Leap 1B-powered 737-9 SAF campaign of 2021.
“This is the logical continuation of those ground testing efforts," Moore says. "In those previous tests we were able to observe the soot particle emissions reductions from the engine on the ground. The question, of course, is when we bring the engine up into cruise conditions do we see the reduction in soot particle emissions and do those reductions translate into reduced contrail ice crystals? We can't probe that on the ground and so that requires flight testing.”
“We are going to burn the same fuel on both engines at the same thrust and we're going to chase the 737-10 with the NASA DC-8, and depending on the sensors that we're using we will be at varying distances in trail,” Moore adds.
Boeing Emissions Technical Fellow Steve Baughcum says: “A lot of what we're going to be focusing on in the test is characterizing the water vapor conditions in which persistent contrails would form. We’ll be working with the modeling teams that predict those regions to help us identify where we should be flying the airplane to observe a persistent contrail. Then we're looking at the effects of using a lean combustor for both soot and then using the 100%-SAF fuel as a way to hopefully produce a very low level of aerosols and then see how that affects the characteristics of the contrails that we form.”
A suite of instruments on board the DC-8 will measure the water vapor content and other characteristics of the outside atmosphere in-situ. “We also have detailed instruments that draw air into the cabin, where we can interrogate it with the same particle counters and gas analyzers that we used on the ground,” Moore says. “That will allow us to understand the engine exhaust plume.”
The DC-8 instrument array includes sensor probes to visualize the ice crystal content in the contrail, and atmospheric light detection and ranging (LIDAR) systems. “The LIDAR on the DC-8 is a unique state-of-the-art capability which allows us to measure the cross-sectional return of the contrail,” Moore says. By varying the LIDAR wavelength, researchers aim to measure the profile, or curtain, of water vapor below the aircraft, which will provide the larger-scale atmospheric context of the sample area.
The ecoDemonstrator team will work closely with forecasters who are developing modeling tools for predicting where contrails will occur. Flights will begin sampling at waypoint coordinates in the forecast contrail zone, and the DC-8 will collect profile data on the atmosphere to see if it matches the model’s prediction. “If we're wrong, then we know something about the model and we can ask the lead aircraft to climb to a more favorable altitude for contrail formation. If we're right, we can just stay there and profile the contrail that the aircraft is forming,” Moore says.
Data from the flight tests, along with simultaneous imaging from NASA satellites, will also feed into follow-on work planned by Boeing in support of the recently awarded Advanced Research Projects Agency–Energy’s (ARPA-E) Pre-Trails exploratory program (for Predictive Real-time Emissions Technologies Reducing Aircraft-Induced Lines in the Sky). Under Pre-Trails, teams led by Boeing, GE Research, Northrop Grumman Systems, RTX Technologies Research Center and the Universities Space Research Association will develop diagnostic and predictive tools to enable mitigation of contrail-related climate forcing.
In-situ atmospheric data will be collected with the remote sensors, while the DC-8 operates at an altitude around 3,000-5,000 ft. higher than the lead aircraft, and at trailing distances ranging from several thousand feet to tens of miles. The DC-8 will then descend into the contrail to sample its properties.
“From a science perspective we'd like to be as close as possible, but from a safety standpoint we have to stay outside a minimum separation distance. It depends on the conditions, but we expect to be somewhere in the 10 to 20 miles in-trail range to penetrate the primary vortices,” Moore explains.
“Once we've done that with one fuel, then we will ask the lead aircraft to switch to the 100% SAF and we can measure the change in the control properties associated with the aircraft fuel,” he adds.