Airbus Evaluating Cryogenic Electric Propulsion For Commercial Aircraft
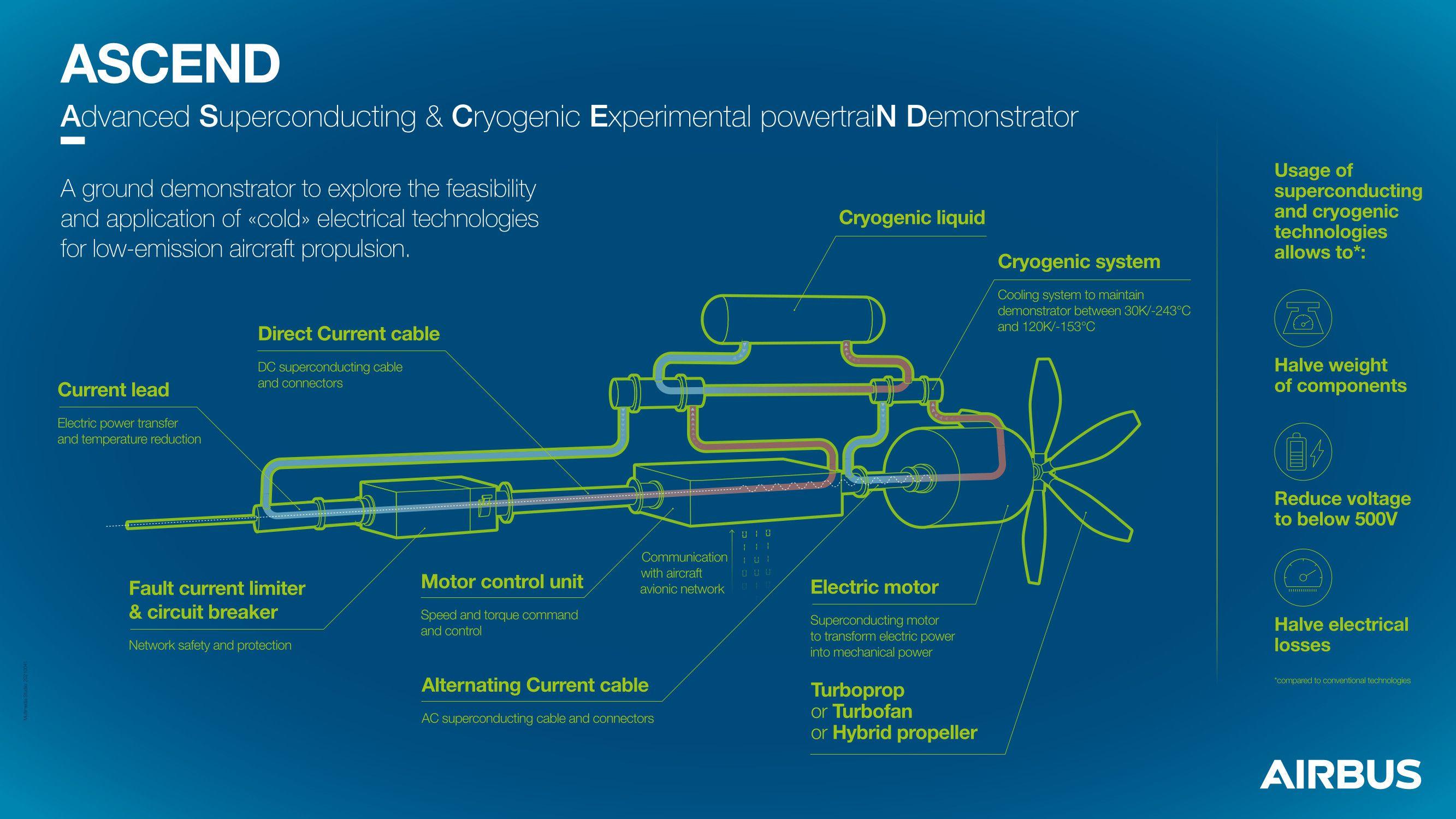
Credit: Airbus
As Airbus evaluates liquid hydrogen as a possible route to zero-emission commercial aviation by the mid-2030s, it has begun a research program to explore the potential of cryogenically cooled electric propulsion for large civil aircraft. The goal of the three-year Advanced Superconducting &...
Subscription Required
This content requires a subscription to one of the Aviation Week Intelligence Network (AWIN) bundles.
Schedule a demo today to find out how you can access this content and similar content related to your area of the global aviation industry.
Already an AWIN subscriber? Login
Did you know? Aviation Week has won top honors multiple times in the Jesse H. Neal National Business Journalism Awards, the business-to-business media equivalent of the Pulitzer Prizes.