Gallery: COVID-19 Drives Innovations at Delta Air Lines and its Subsidiaries
Lindsay Bjerregaard October 29, 2020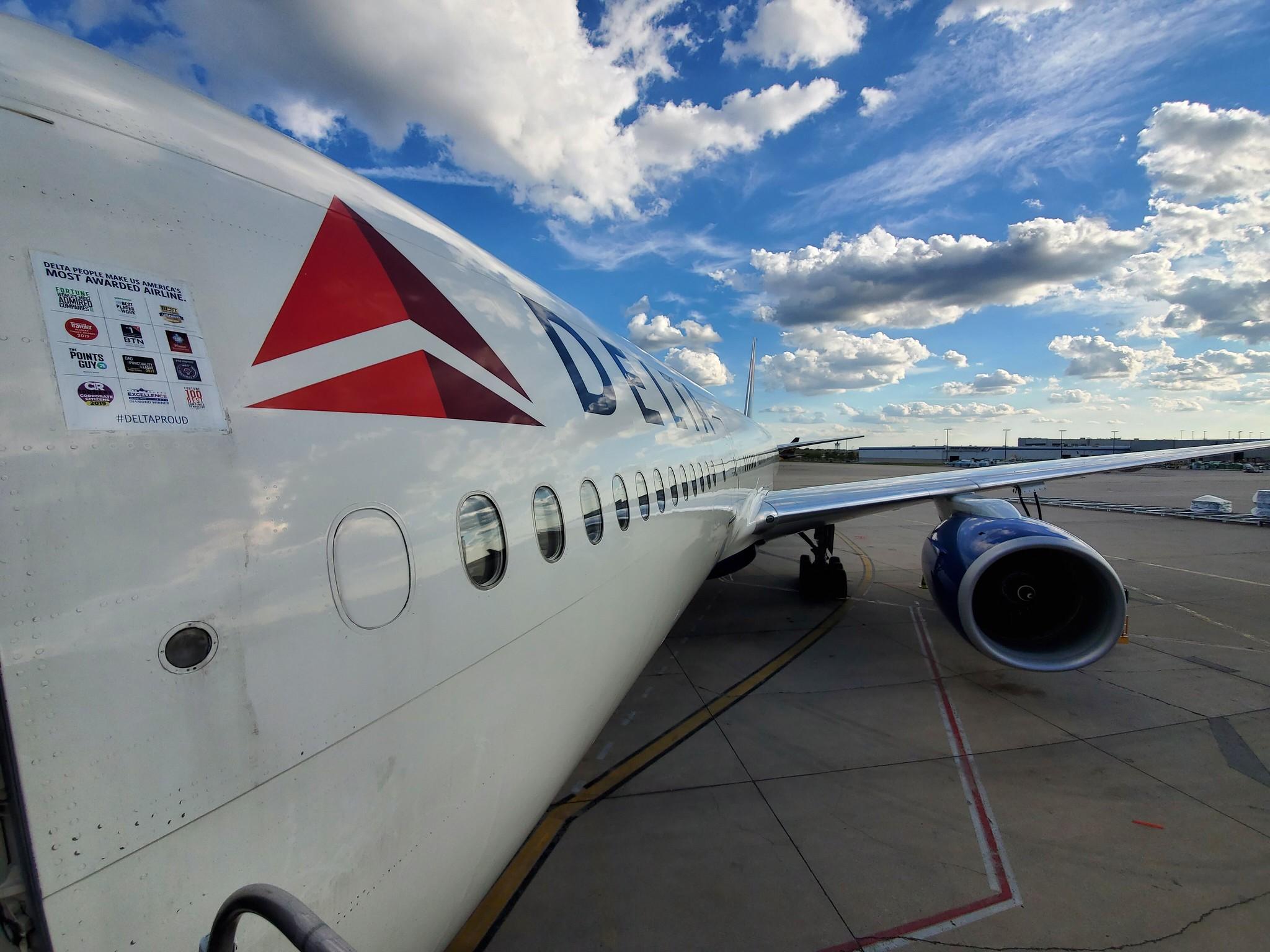
Credit: Delta
During the COVID-19 pandemic, Delta Air Lines and its subsidiaries have focused on adapting business and developing innovations to solve new challenges. Read on to find out more about how the pandemic has affected its operations and how workflows have changed this year.
During the COVID-19 pandemic, Delta Air Lines and its subsidiaries have focused on adapting business and developing innovations to solve new challenges. Read on to find out more about how the pandemic has affected its operations and how workflows have changed this year.
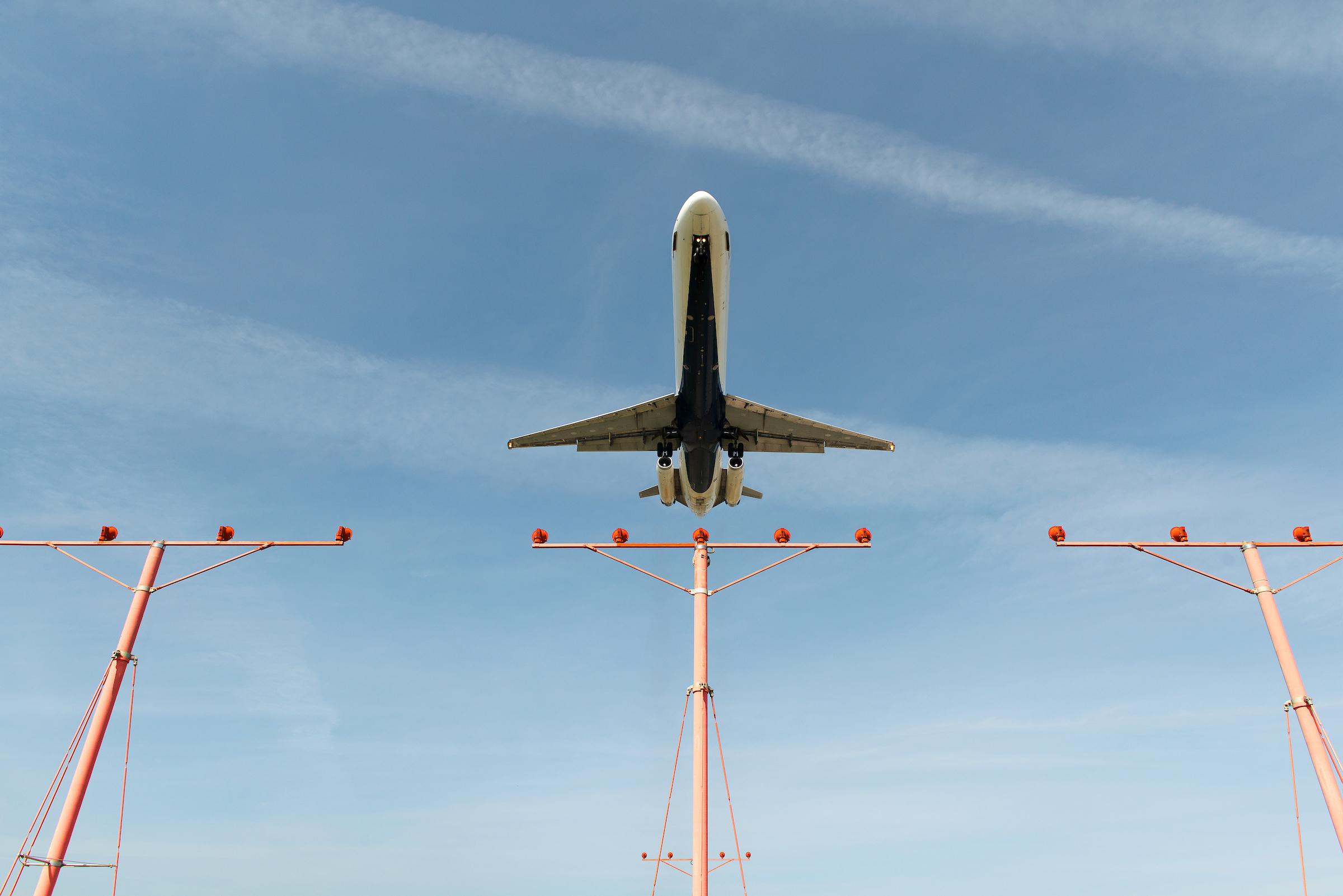
Changes to Fleets and Passenger Loads
Credit: Delta
Like other carriers around the world, Delta’s passenger load has dropped in 2020 as a result of the COVID-19 pandemic. While it has seen a slight bump since September, Delta says its recent passenger loads are down about 30% compared to 2019.
The airline is using the downturn as an opportunity to retire some of its aging fleets, including MD-88 and MD-90, and Boeing 777-200/717-200/767-300ER aircraft. Still remaining in its portfolio or on order are Airbus A220/A320 family/A330ceo/A330neo and Boeing 737NG/757-200/767-400 aircraft.
Like other carriers around the world, Delta’s passenger load has dropped in 2020 as a result of the COVID-19 pandemic. While it has seen a slight bump since September, Delta says its recent passenger loads are down about 30% compared to 2019.
The airline is using the downturn as an opportunity to retire some of its aging fleets, including MD-88 and MD-90, and Boeing 777-200/717-200/767-300ER aircraft. Still remaining in its portfolio or on order are Airbus A220/A320 family/A330ceo/A330neo and Boeing 737NG/757-200/767-400 aircraft.
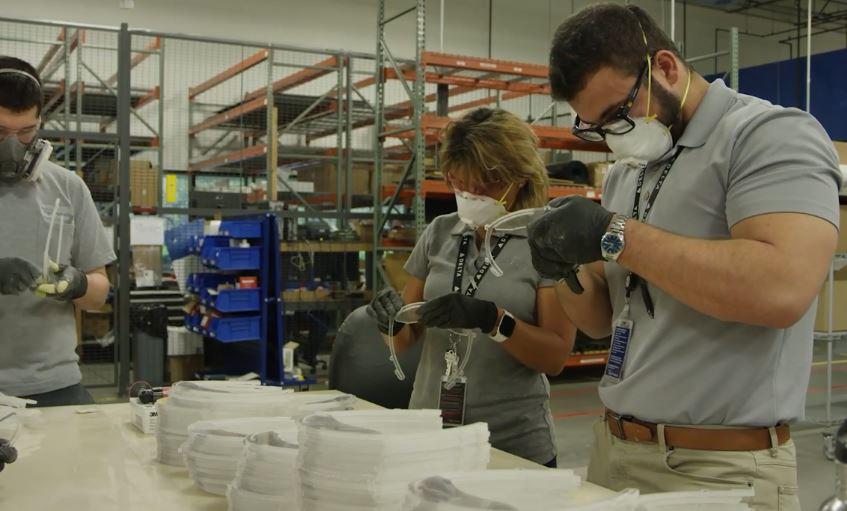
Face Shield Production
Credit: Delta
As part of its efforts to help the global fight against COVID-19, Delta has manufactured masks and more than 100,000 face shields in partnership with its team at subsidiary Delta Flight Products. At the height of production, Delta says it was producing 5,000 face shields per day for frontline healthcare workers.
As part of its efforts to help the global fight against COVID-19, Delta has manufactured masks and more than 100,000 face shields in partnership with its team at subsidiary Delta Flight Products. At the height of production, Delta says it was producing 5,000 face shields per day for frontline healthcare workers.
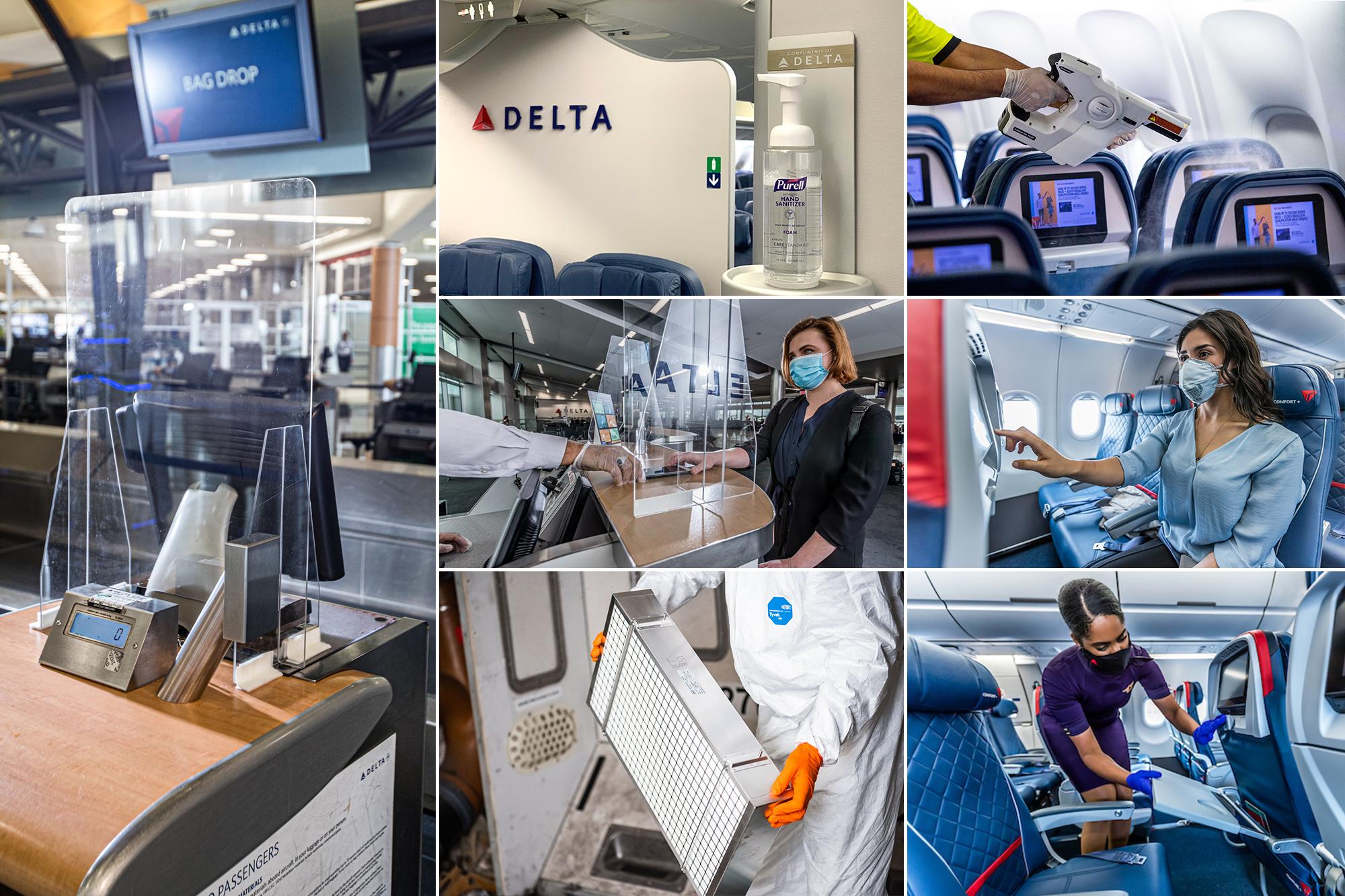
Safety and Sanitization Features
Credit: Delta
To fight the spread of COVID-19 and increase passenger confidence about flying, Delta has added a variety of new safety features and standards. In addition to its partnership with Lysol, it has been blocking middle seats on aircraft and is using advanced air filtration systems. On aircraft it has added hand sanitizer stations near boarding doors and lavatories, as well as hands-free features to reduce touch points. At airports, it has implemented antimicrobial bins at security checkpoints, plexiglass shields at boarding gates and check-in counters, and safe distancing.
To fight the spread of COVID-19 and increase passenger confidence about flying, Delta has added a variety of new safety features and standards. In addition to its partnership with Lysol, it has been blocking middle seats on aircraft and is using advanced air filtration systems. On aircraft it has added hand sanitizer stations near boarding doors and lavatories, as well as hands-free features to reduce touch points. At airports, it has implemented antimicrobial bins at security checkpoints, plexiglass shields at boarding gates and check-in counters, and safe distancing.
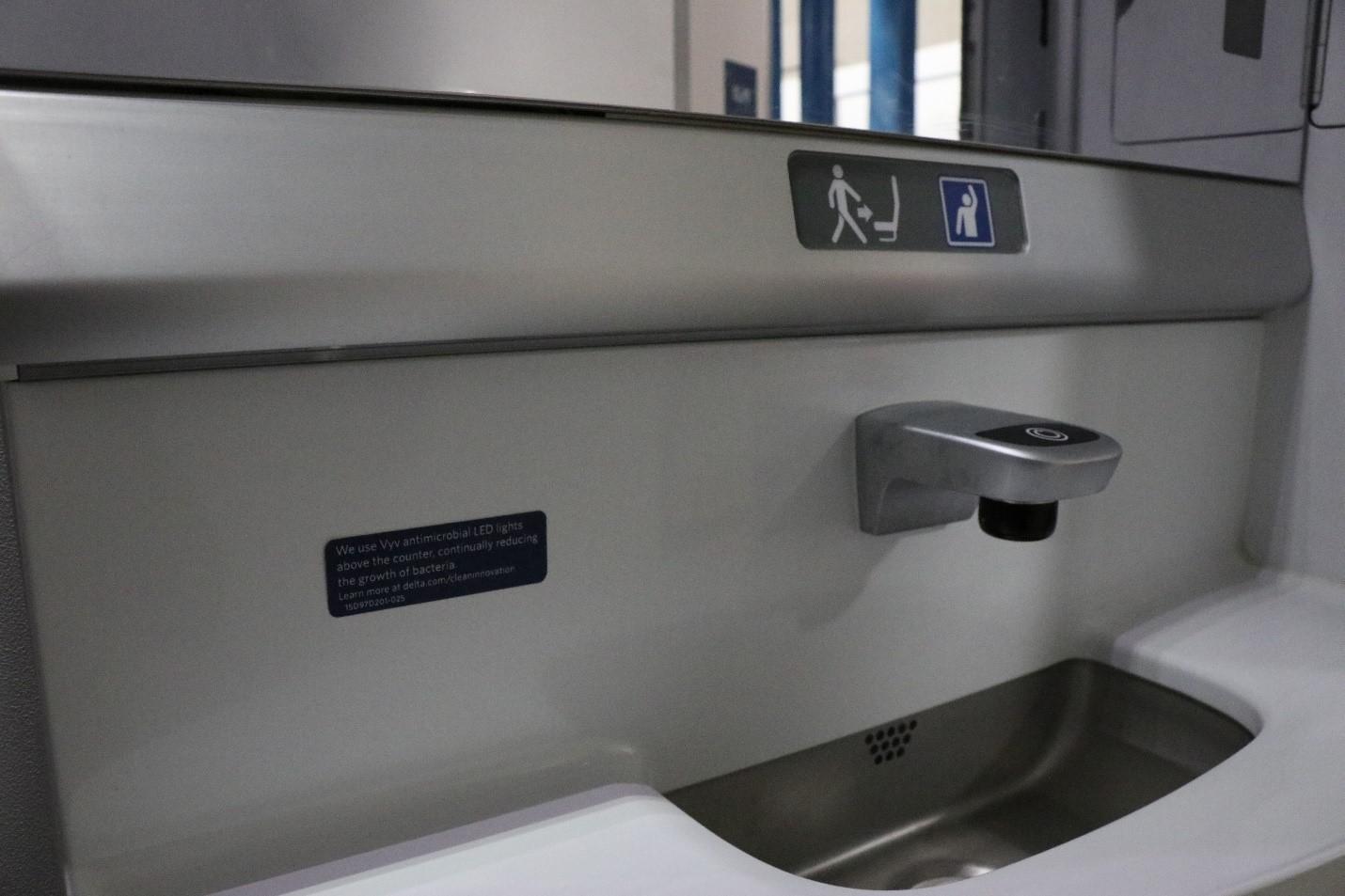
Antimicrobial Technology
Credit: Delta
Delta is exploring the use of surface treatment technology for aircraft cabins and just announced a partnership with antimicrobial LED lighting provider Vyv to install the technology above onboard lavatory sinks and countertops to continually reduce the growth of bacteria. The first installations will happen in mid-November on its 757-200 fleet, and Delta says it will conduct further tests next year with the hope of expanding installation in the future.
Delta is exploring the use of surface treatment technology for aircraft cabins and just announced a partnership with antimicrobial LED lighting provider Vyv to install the technology above onboard lavatory sinks and countertops to continually reduce the growth of bacteria. The first installations will happen in mid-November on its 757-200 fleet, and Delta says it will conduct further tests next year with the hope of expanding installation in the future.
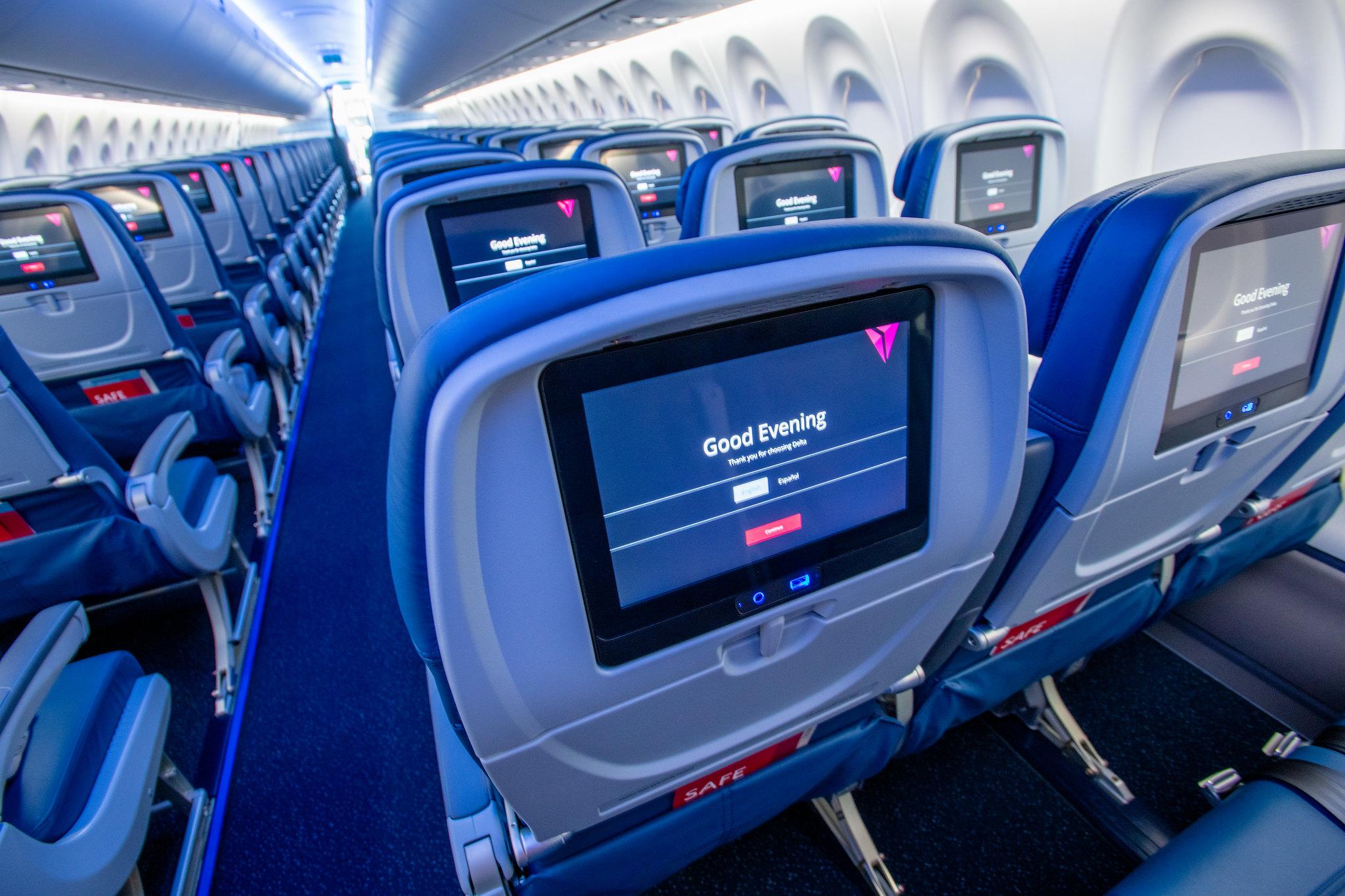
In-flight connectivity is increasingly becoming a hygiene factor on flights, especially medium- to long-haul flights.
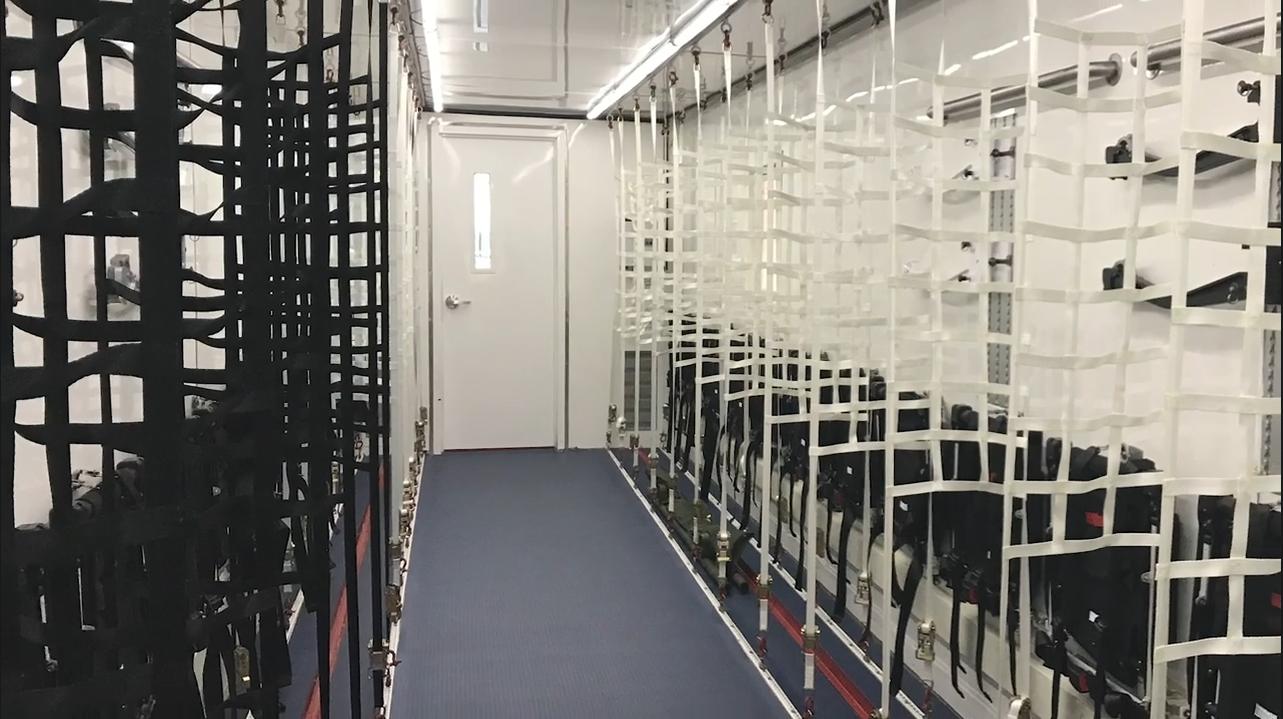
Negative Pressure Containers
Credit: Delta
The airline and Delta Flight Products have also partnered with the U.S. Air Force to design a creative solution to help transport troops infected with COVID-19. The idea was initially conceived by an Air Force officer who proposed taking a 40-ft. shipping container and converting it into a format that could be quickly reconfigured for safe troop transport.
The teams worked to produce negative pressure containers (NPC) that filter and move air outside. They feature a patient room with military stretchers and jump seats, as well as an anteroom for medical staff to suit up before attending to troops. The NPC was first designed for C-17 aircraft and Delta is also producing a lighter version to be carried on C-130 aircraft. The teams took the idea from concept to production in 88 days and currently has nine units flying.
The airline and Delta Flight Products have also partnered with the U.S. Air Force to design a creative solution to help transport troops infected with COVID-19. The idea was initially conceived by an Air Force officer who proposed taking a 40-ft. shipping container and converting it into a format that could be quickly reconfigured for safe troop transport.
The teams worked to produce negative pressure containers (NPC) that filter and move air outside. They feature a patient room with military stretchers and jump seats, as well as an anteroom for medical staff to suit up before attending to troops. The NPC was first designed for C-17 aircraft and Delta is also producing a lighter version to be carried on C-130 aircraft. The teams took the idea from concept to production in 88 days and currently has nine units flying.
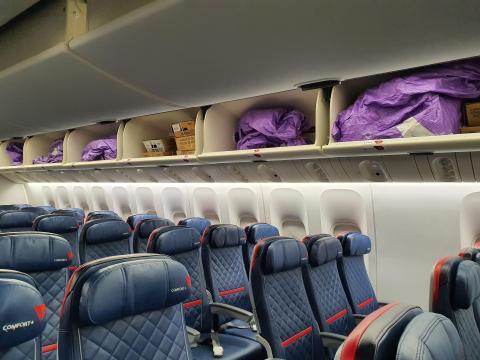
Cargo Flexibility
Credit: Delta
Also getting creative with cargo has been Delta TechOps, which obtained an FAA STC earlier this year to haul package cargo on the main deck of Delta’s 777 fleet. Although the airline plans to retire the 777 by the end of 2020, it says its 777 fleet “has been the workhorse of Delta’s cargo, mail and U.S. citizen repatriation operations amid the pandemic.”
Also getting creative with cargo has been Delta TechOps, which obtained an FAA STC earlier this year to haul package cargo on the main deck of Delta’s 777 fleet. Although the airline plans to retire the 777 by the end of 2020, it says its 777 fleet “has been the workhorse of Delta’s cargo, mail and U.S. citizen repatriation operations amid the pandemic.”
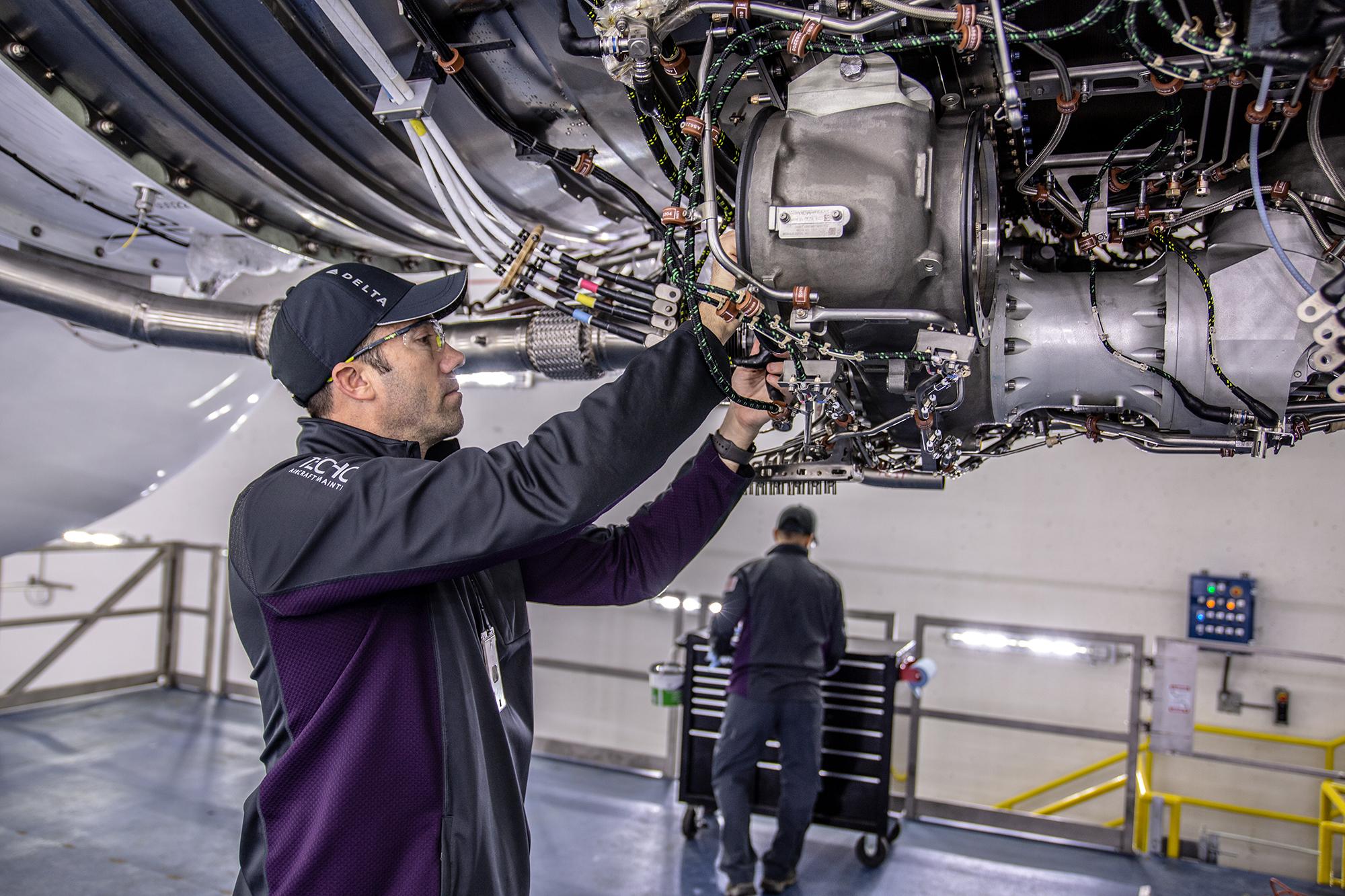
Changes to MRO Demand
Credit: Delta
Although MRO demand has been down this year due to parked aircraft, Delta TechOps is now seeing a slight resurgence with aircraft coming back into service. According to Sonny Stern, vice president of sales and customer service for Delta TechOps, there is still demand for lighter engine work with the goal of getting aircraft back into service or transitioning aircraft from airlines to lessors and vice versa.
“We have been seeing an uptick in some of those lighter visits, as well as component business for airlines that are starting to get back up and running, as aircraft have been sitting in the desert or in other locations and they need to get resurrected to be back in service. We’re seeing component volumes pick up as well,” he says.
Although MRO demand has been down this year due to parked aircraft, Delta TechOps is now seeing a slight resurgence with aircraft coming back into service. According to Sonny Stern, vice president of sales and customer service for Delta TechOps, there is still demand for lighter engine work with the goal of getting aircraft back into service or transitioning aircraft from airlines to lessors and vice versa.
“We have been seeing an uptick in some of those lighter visits, as well as component business for airlines that are starting to get back up and running, as aircraft have been sitting in the desert or in other locations and they need to get resurrected to be back in service. We’re seeing component volumes pick up as well,” he says.
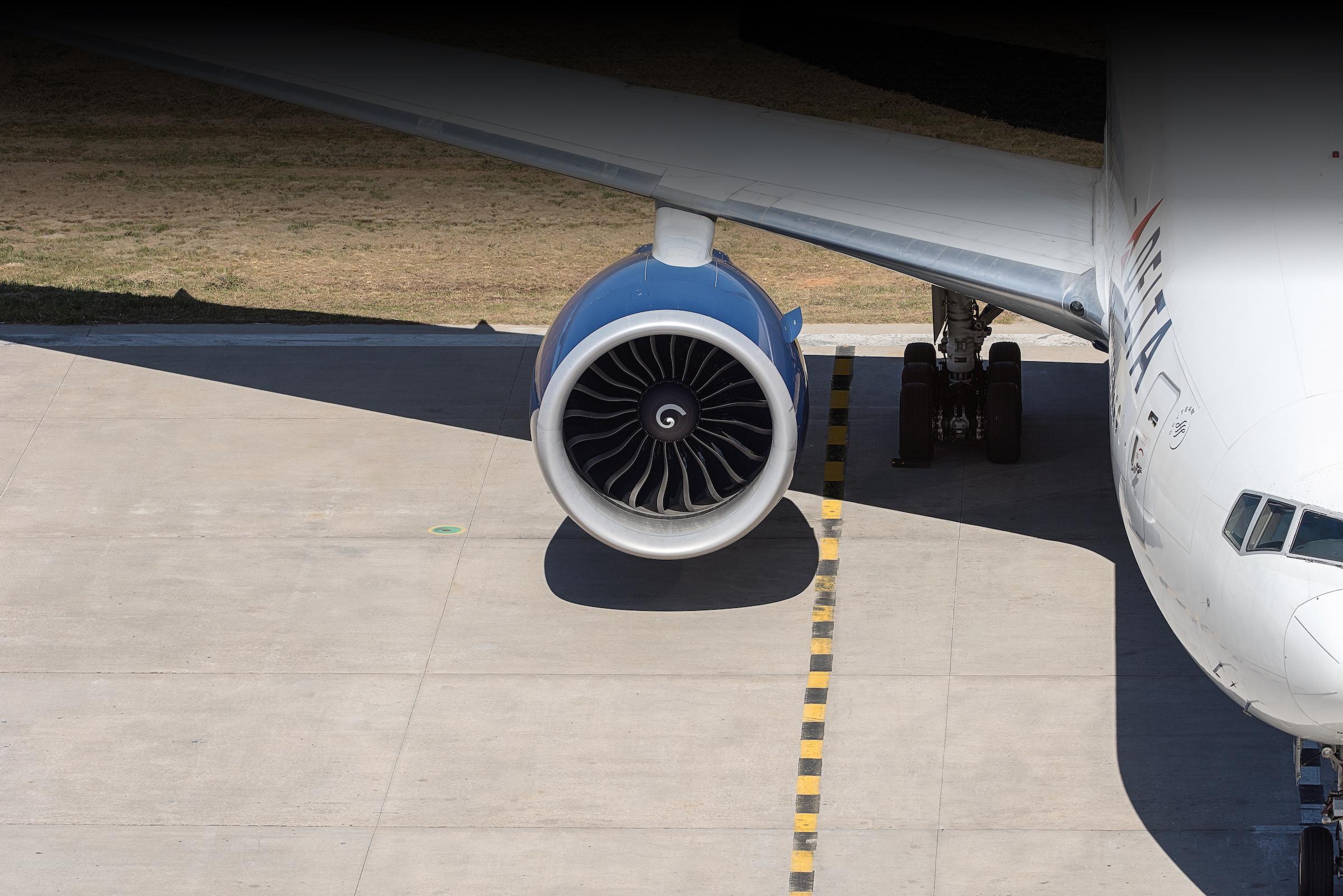
Used Serviceable Materials
Credit: Delta
Component work also will likely grow in the near future due to Delta TechOps’ partnership with Delta Material Services, the airline’s aftermarket provider for used serviceable materials. According to Sally Oboussier-Lowe, supply chain manager at Delta Material Services, the early retirements of Delta’s fleet will position it to provide long-term and extensive materials support across Airbus and Boeing airframes and GE, Pratt & Whitney and Rolls-Royce engine platforms.
In 2021, it expects to part out around 75 engines and 20 airframes in partnership with Delta TechOps, which can tear down assets, inspect and repair material in-house.
Component work also will likely grow in the near future due to Delta TechOps’ partnership with Delta Material Services, the airline’s aftermarket provider for used serviceable materials. According to Sally Oboussier-Lowe, supply chain manager at Delta Material Services, the early retirements of Delta’s fleet will position it to provide long-term and extensive materials support across Airbus and Boeing airframes and GE, Pratt & Whitney and Rolls-Royce engine platforms.
In 2021, it expects to part out around 75 engines and 20 airframes in partnership with Delta TechOps, which can tear down assets, inspect and repair material in-house.
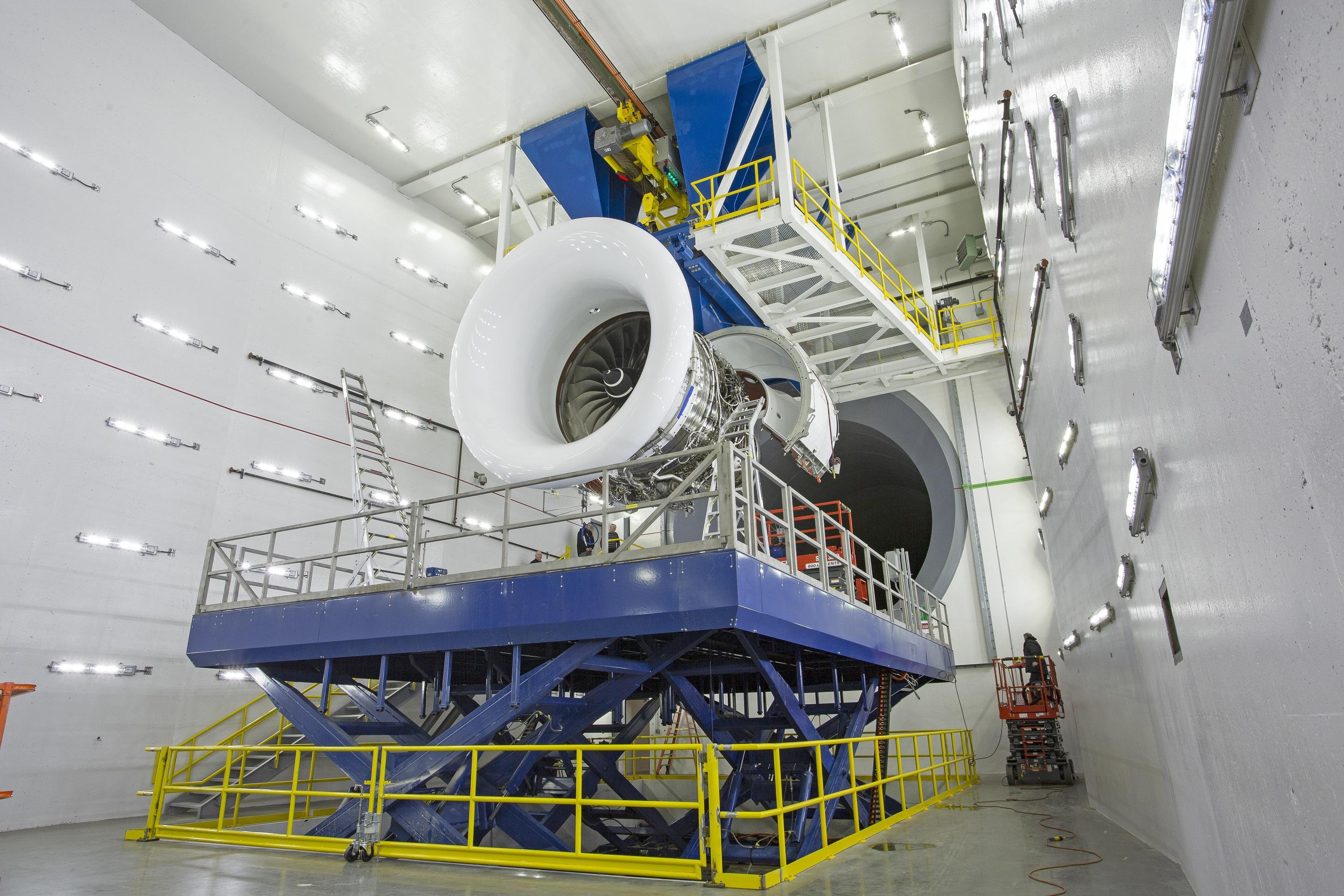
New Engine Investments
Credit: Delta
Delta TechOps has continued work this year in line with its investments into new and emerging engine lines. It opened the world’s largest test cell in Feb. 2019, a $100 million investment that it says will be capable of testing engines that have yet to be designed. It has invested heavily in hot section repairs and says it will be prepared to start providing support to the market for Rolls-Royce Trent XWB nozzle guide vanes, outlet guide vanes and fan blades moving into 2021.
Delta TechOps has continued work this year in line with its investments into new and emerging engine lines. It opened the world’s largest test cell in Feb. 2019, a $100 million investment that it says will be capable of testing engines that have yet to be designed. It has invested heavily in hot section repairs and says it will be prepared to start providing support to the market for Rolls-Royce Trent XWB nozzle guide vanes, outlet guide vanes and fan blades moving into 2021.
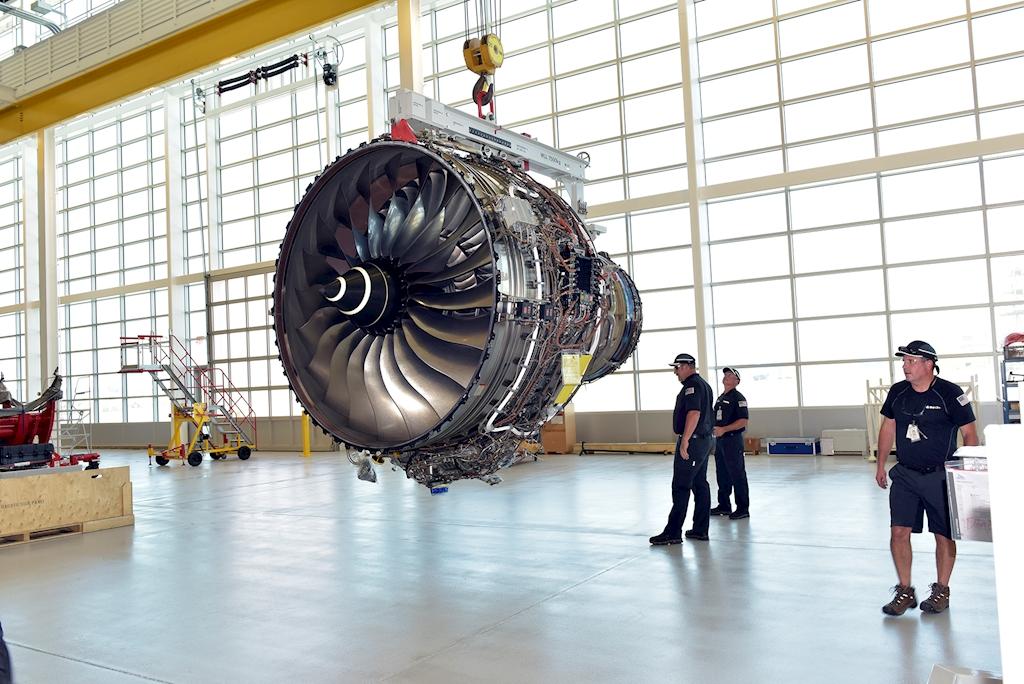
Engine OEM Partnerships
Credit: Delta
It also recently converted an airframe hangar to accommodate new requirements for engines as part of its partnerships with Pratt & Whitney and Rolls-Royce. This year it completed eight low-pressure turbine quick turn visits using a specialized process for Pratt & Whitney GTF engines and it will be adding tooling and manpower for up to 20 PW1100 engines being worked on in parallel in 2021.
It started its first Rolls-Royce Trent 1000 check and repair induction this month. In 2021 it will begin work on XWBs and introduce Danobat tooling and blade tip grind installation to support full-service MRO capabilities for Trent and other shop lines. It expects to induct its first Trent 7000 for refurbishment in 2022.
It also recently converted an airframe hangar to accommodate new requirements for engines as part of its partnerships with Pratt & Whitney and Rolls-Royce. This year it completed eight low-pressure turbine quick turn visits using a specialized process for Pratt & Whitney GTF engines and it will be adding tooling and manpower for up to 20 PW1100 engines being worked on in parallel in 2021.
It started its first Rolls-Royce Trent 1000 check and repair induction this month. In 2021 it will begin work on XWBs and introduce Danobat tooling and blade tip grind installation to support full-service MRO capabilities for Trent and other shop lines. It expects to induct its first Trent 7000 for refurbishment in 2022.
A look at how Delta and its TechOps, Flight Products and Material Services groups have adapted to COVID-19 challenges.