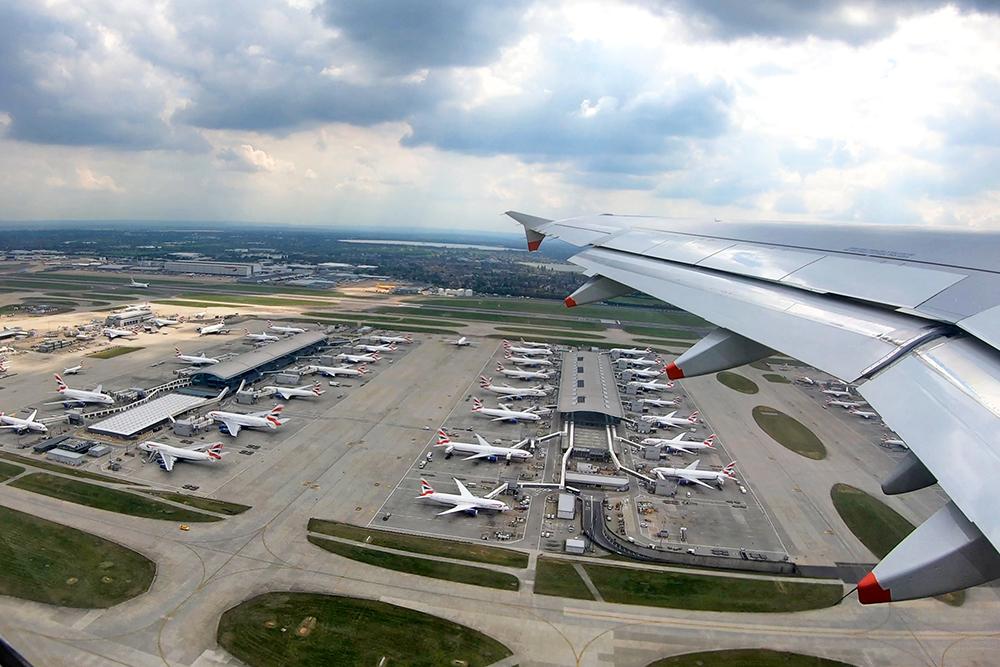
Credit: Depositphotos/rixpix
Paperwork that links a new part to its production approval holder “is a requirement” under the U.S-European Union (EU) aviation safety bilateral, meaning proof inspection and approval by a U.S. repair station will no longer be accepted for parts being installed on EU-registered aircraft, the FAA has...
Subscription Required
FAA Changes Position On Parts Validation Process is published in Aviation Daily, an Aviation Week Intelligence Network (AWIN) Market Briefing and is included with your AWIN membership.
Already a member of AWIN or subscribe to Aviation Daily through your company? Login with your existing email and password
Not a member? Learn how to access the market intelligence and data you need to stay abreast of what's happening in the air transport community.