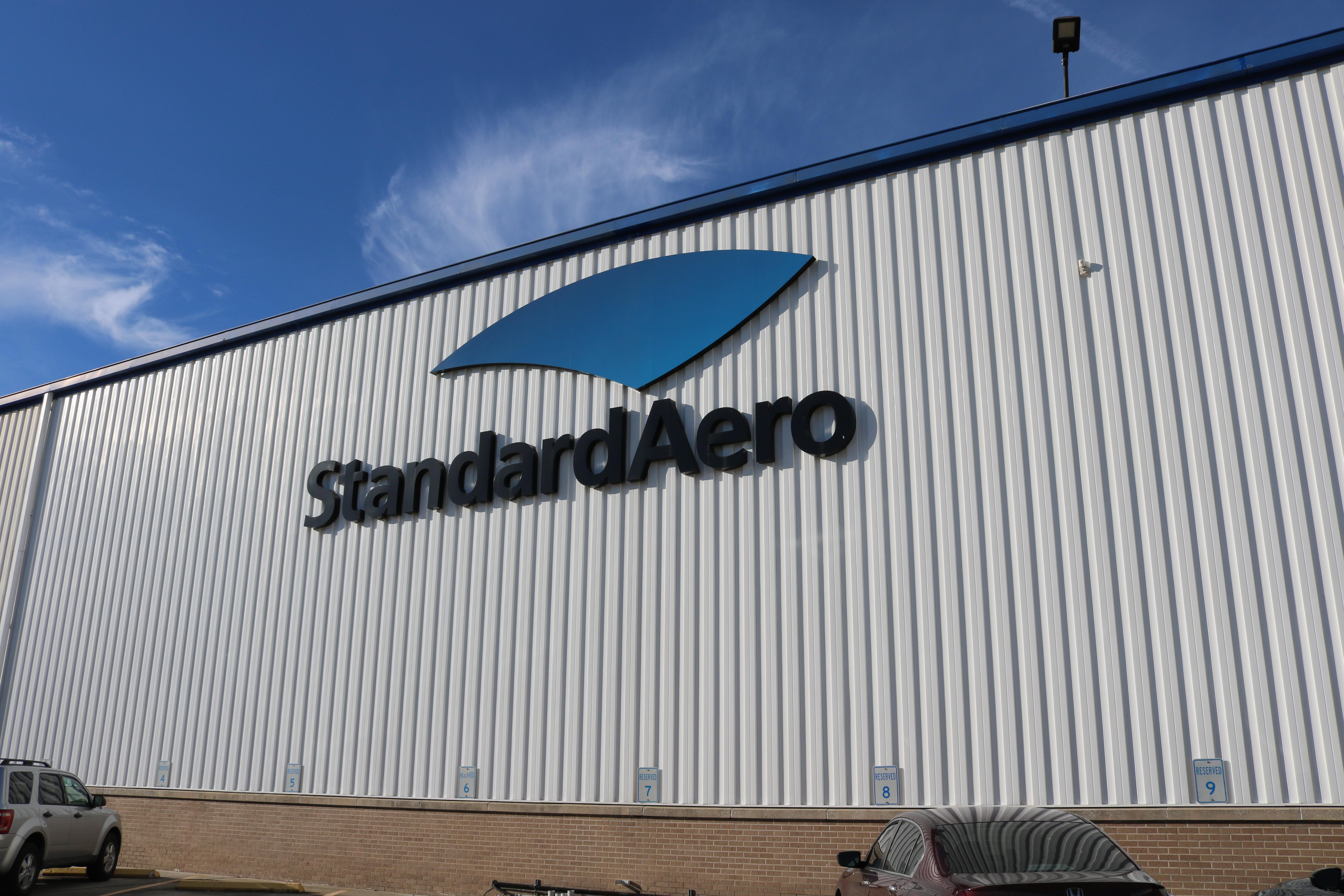
Credit: Lindsay Bjerregaard/Aviation Week
StandardAero recently celebrated its 20th anniversary at Port San Antonio. Aviation Week got a behind the scenes look at the 810,000 ft.2 facilities as the site ramps up work for Rolls-Royce, GE and the U.S. Air Force.
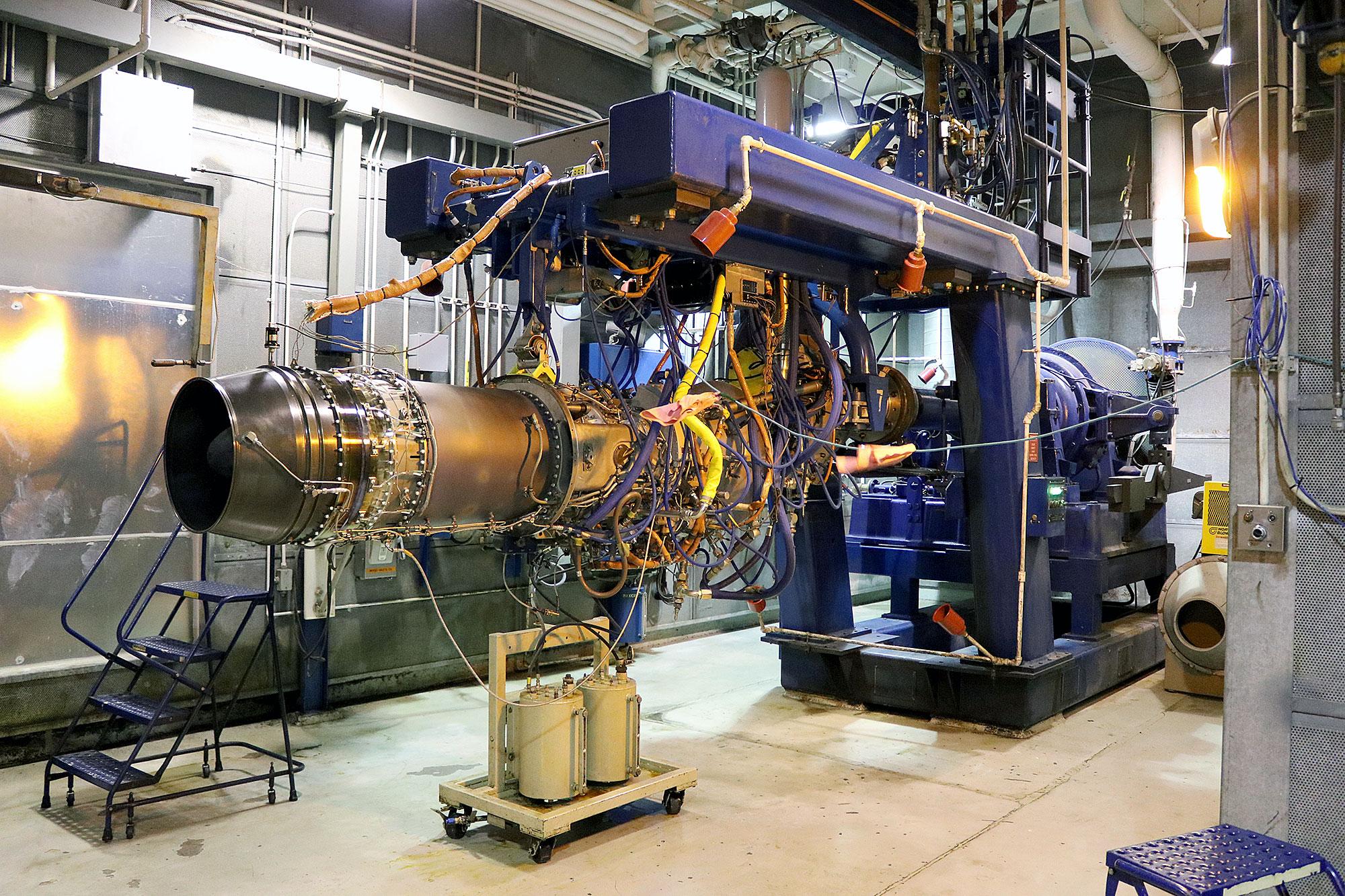
Credit: Lindsay Bjerregaard/Aviation Week
Built in the home of a former U.S. Air Force propulsion depot, StandardAero’s San Antonio site consists of space for engine MRO, warehousing and engine test cells. According to Mark Buongiorno, vice president and general manager of the San Antonio site, it follows StandardAero’s design principles of an open, well-lit cellular structure.
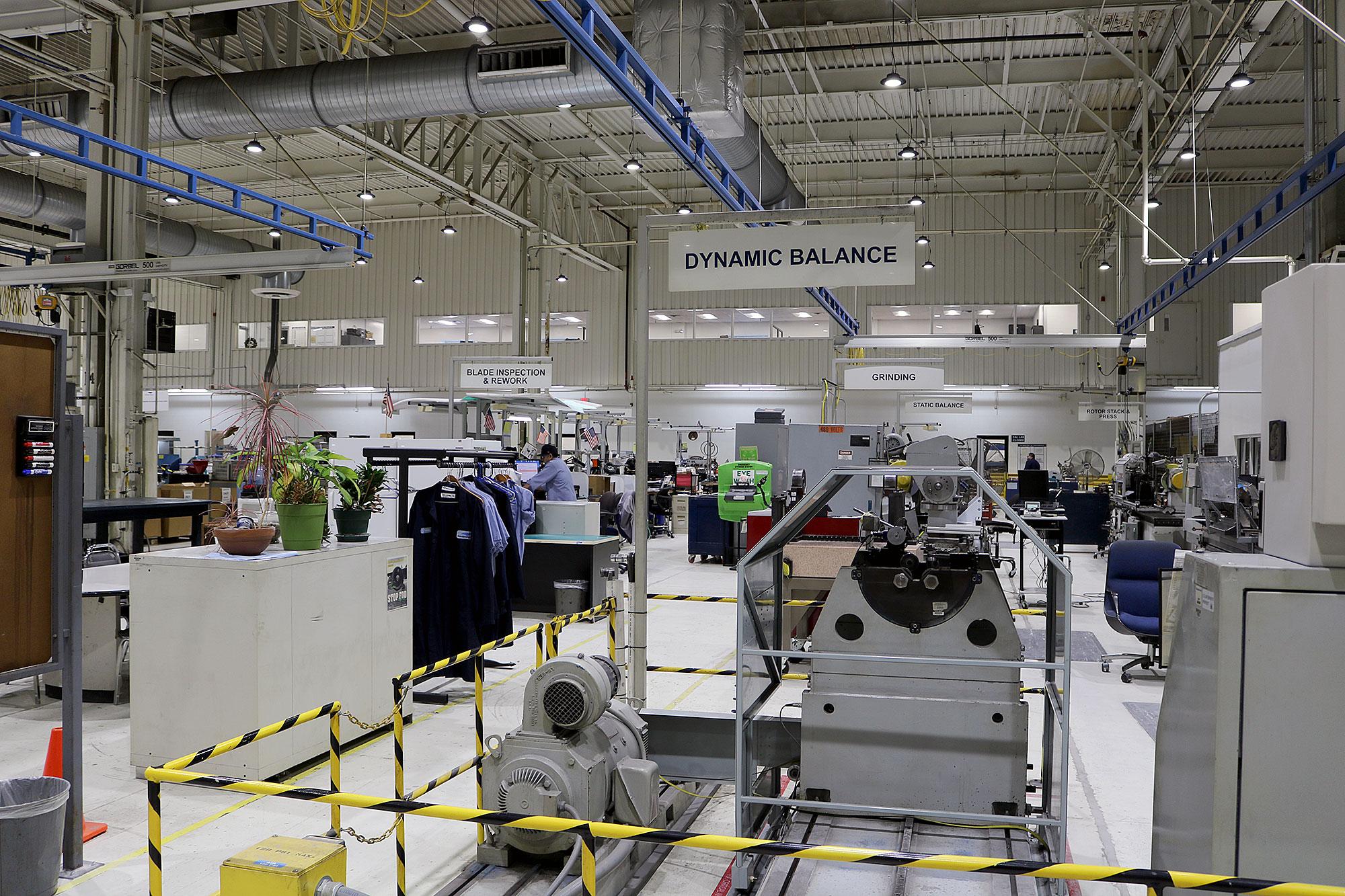
Credit: Lindsay Bjerregaard/Aviation Week
“Our hallmark in engine MRO is to create flow, so we try to break it down into logical pieces that are of similar size, technology and capability,” Buongiorno explains. “We build cells along that path that have the resources, trained people, equipment, tooling and any special equipment necessary to execute what’s required to do the teardown, inspection and reassembly of that particular component or model.”
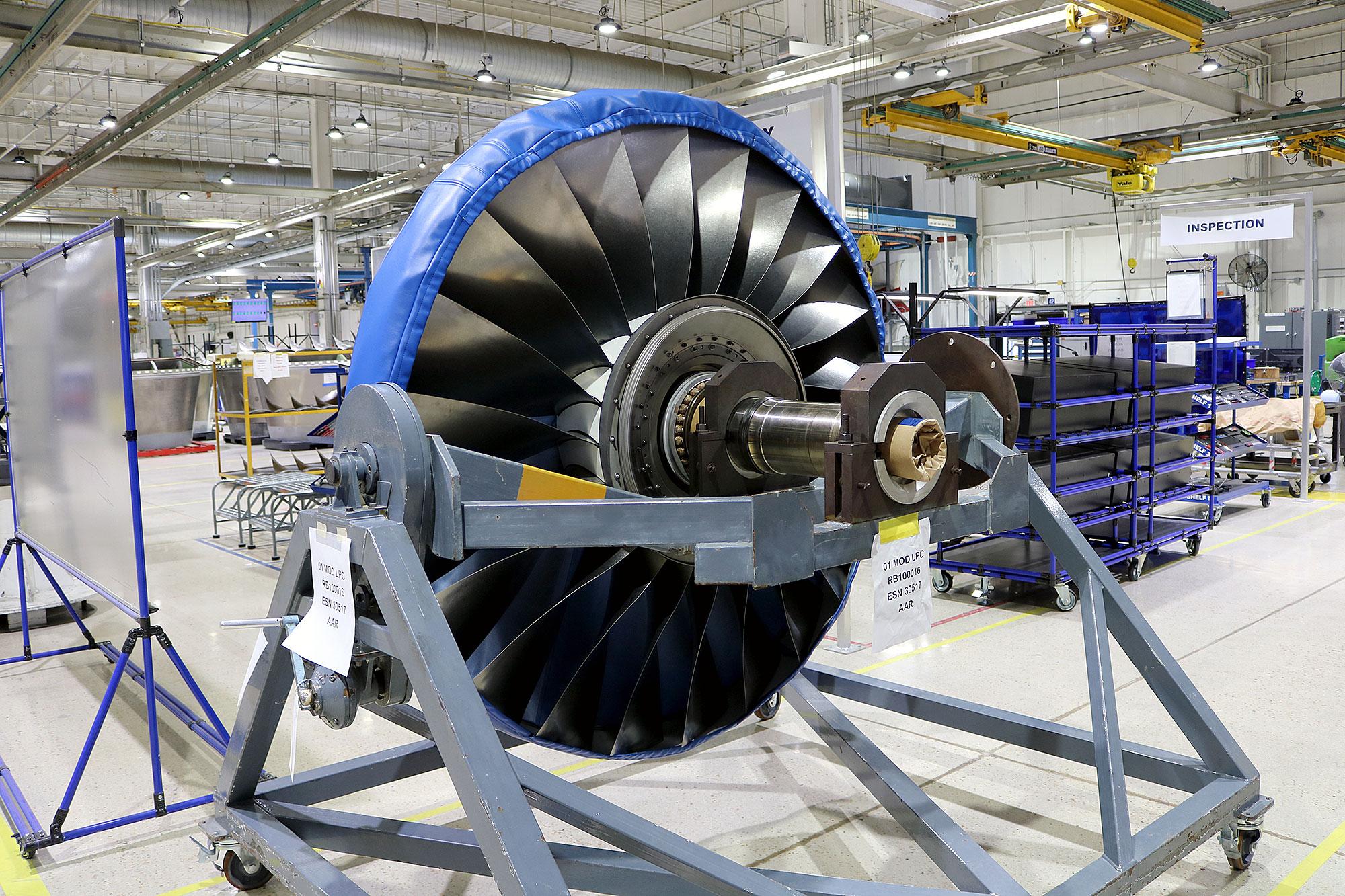
Credit: Lindsay Bjerregaard/Aviation Week
One example of this is the site’s Rolls-Royce RB211 line, which is divided into specialized cells that contain all the tools and components needed to break down and rebuild the engine type step-by-step. The engines, which power the Boeing 757, are broken down into their individual assemblies, cleaned, inspected, put into kits and released.
StandardAero was chosen by Rolls-Royce in 2018 as its “life of type” maintenance service provider for the RB211 and in-service support is being transferred from Rolls-Royce’s Derby, UK location to StandardAero San Antonio.
StandardAero was chosen by Rolls-Royce in 2018 as its “life of type” maintenance service provider for the RB211 and in-service support is being transferred from Rolls-Royce’s Derby, UK location to StandardAero San Antonio.
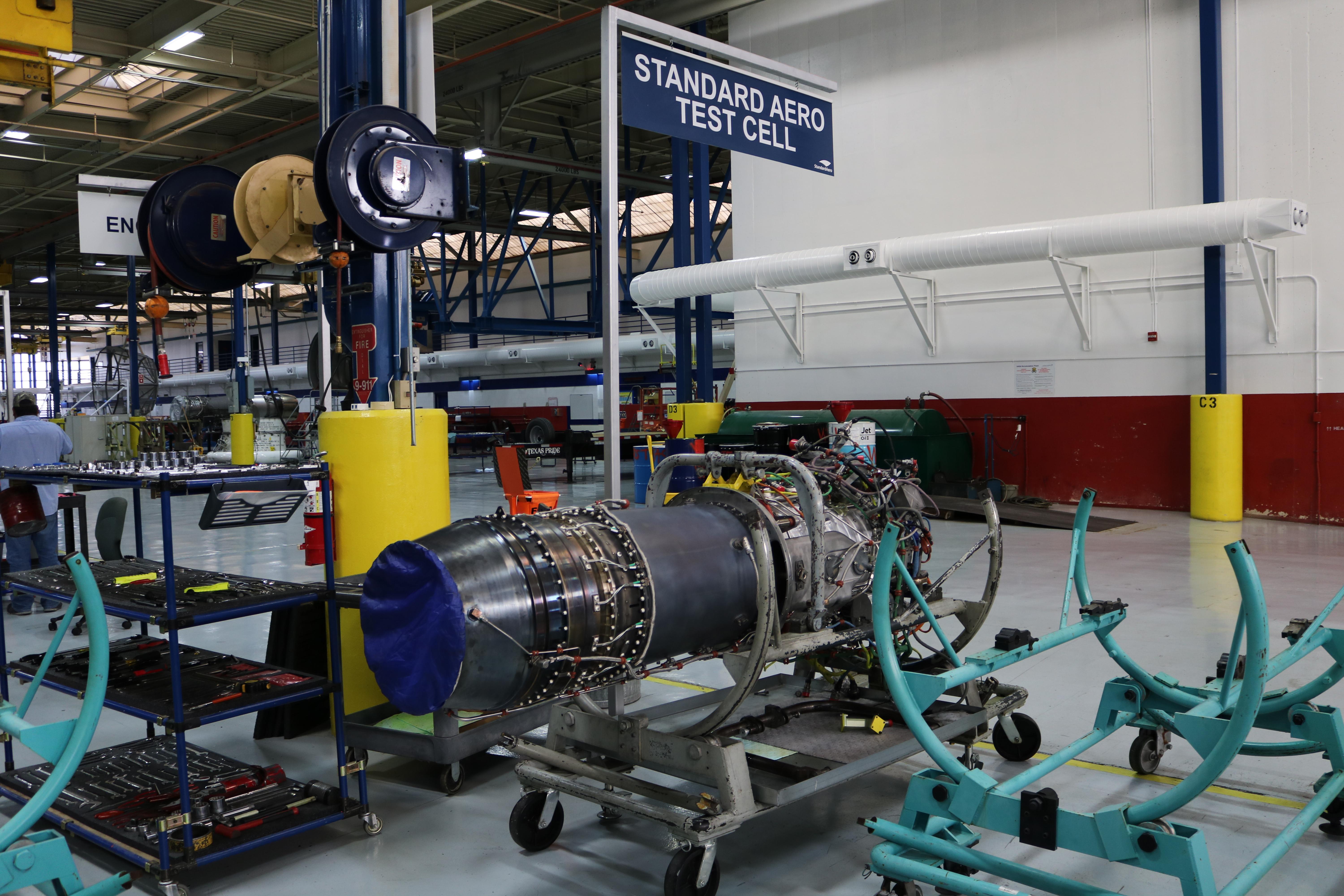
Credit: Lindsay Bjerregaard/Aviation Week
The San Antonio facility holds FAA and EASA certification for RB211 disassembly, cleaning, inspection, repair, assembly and test. In November 2019 it received FAA approval for acceptance testing of the engine type, which will enable engine performance testing to be completed on-site before engines are redelivered to customers.
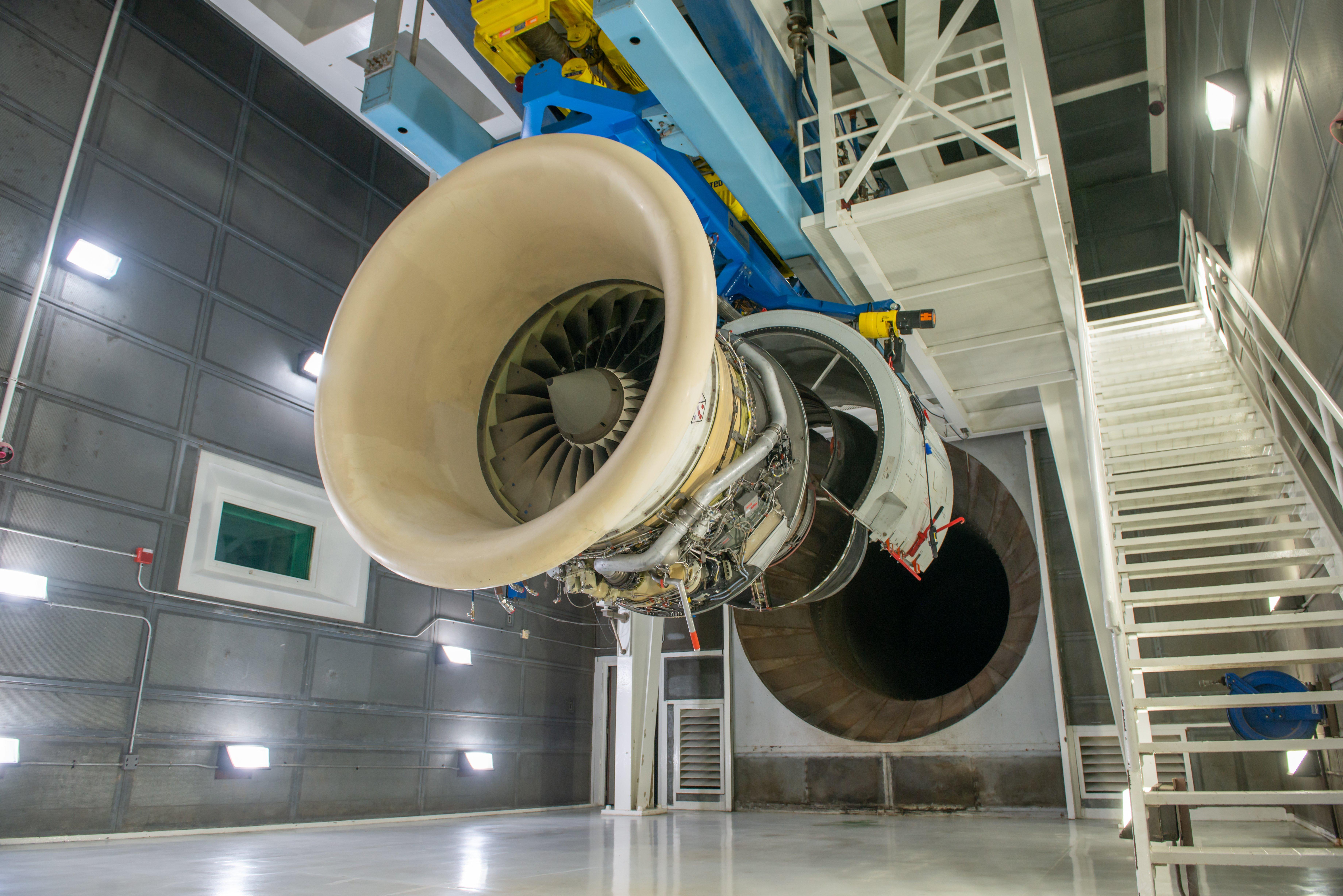
Credit: Port San Antonio
Once engines complete the repair and overhaul process, they are brought to the site’s test facility. StandardAero San Antonio is equipped with four indoor, high-bypass afterburning test cells, two turboprop test cells and two outdoor turboprop test cells. According to Buongiorno, three of the site’s test cells are in the process of being upgraded, including rewiring and installation of LED lights.
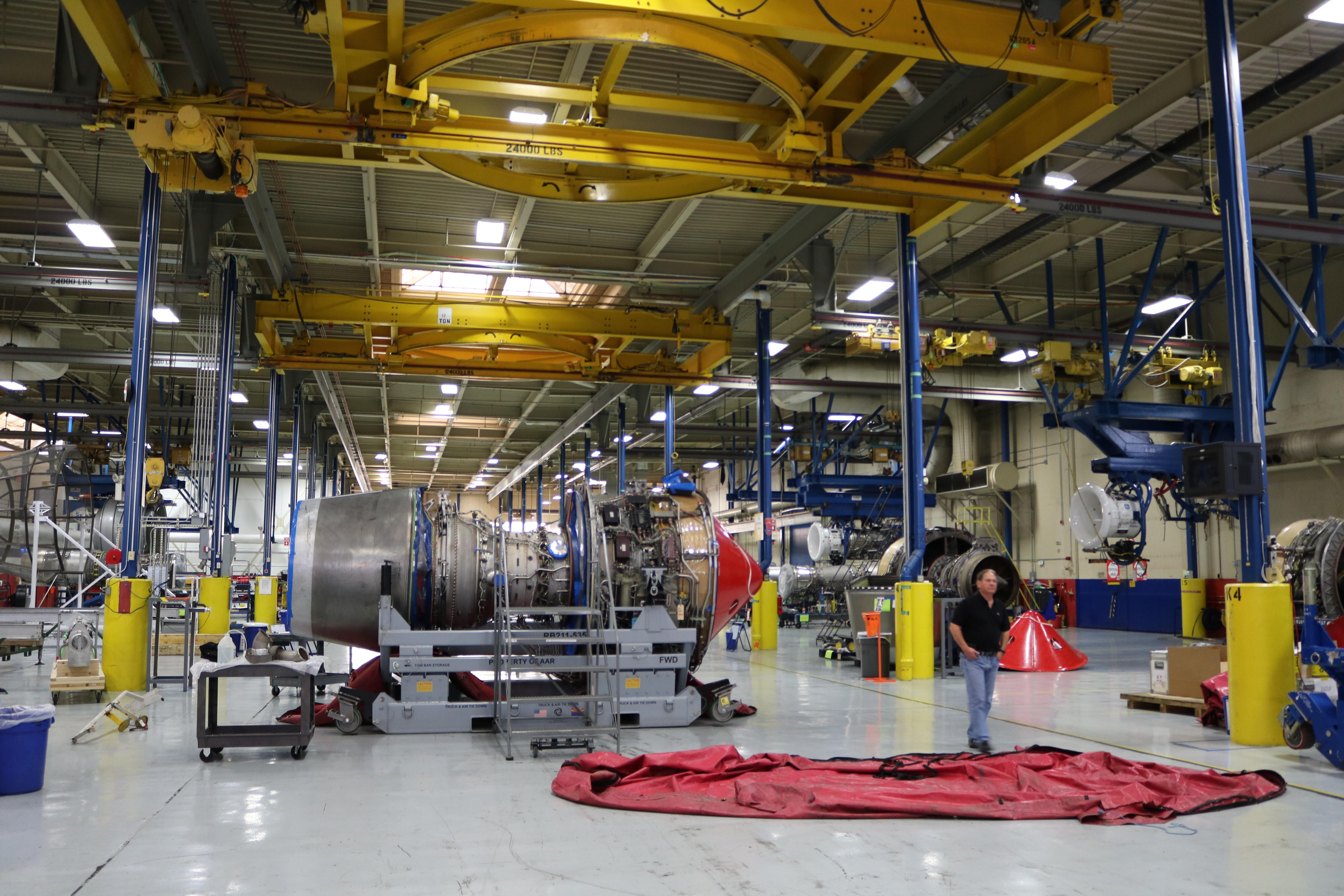
Credit: Lindsay Bjerregaard/Aviation Week
Buongiorno says the site benefits from infrastructure created when the building was purpose-built for jet engine overhaul and repair for the U.S. Air Force, including good crane coverage and a monorail system to move engines around the facility.
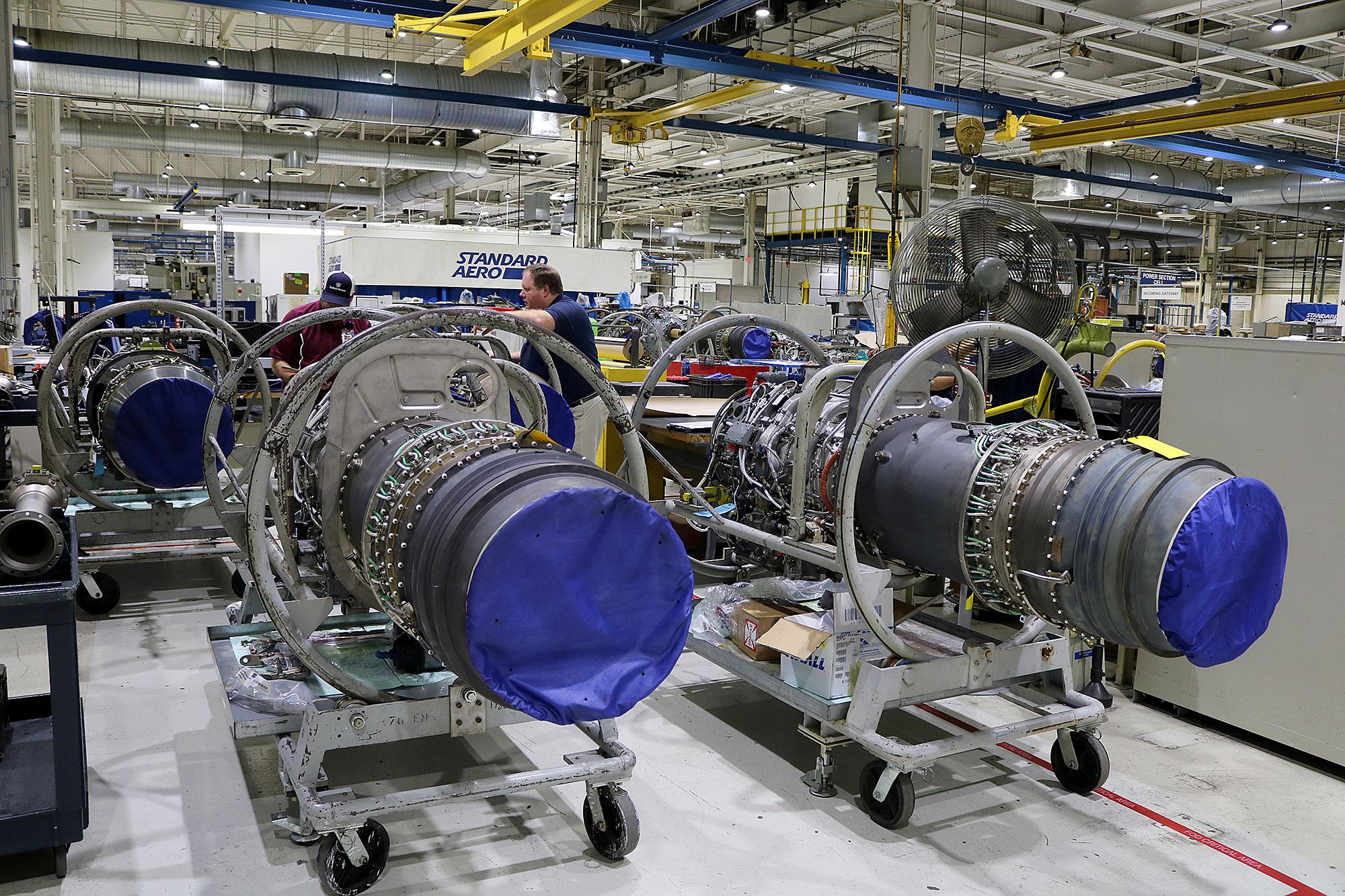
Credit: Lindsay Bjerregaard/Aviation Week
In addition to a ramp-up in work for the RB211, StandardAero has been growing to accommodate other new projects for both Rolls-Royce and GE Aviation. The site was recently selected to provide MRO services for Rolls-Royce AE 2100, AE 1107 and T56 Series IV engine models through 2038. “We are delivering product on all three of those products right now and are ramping up to our full production rate,” says Buongiorno.
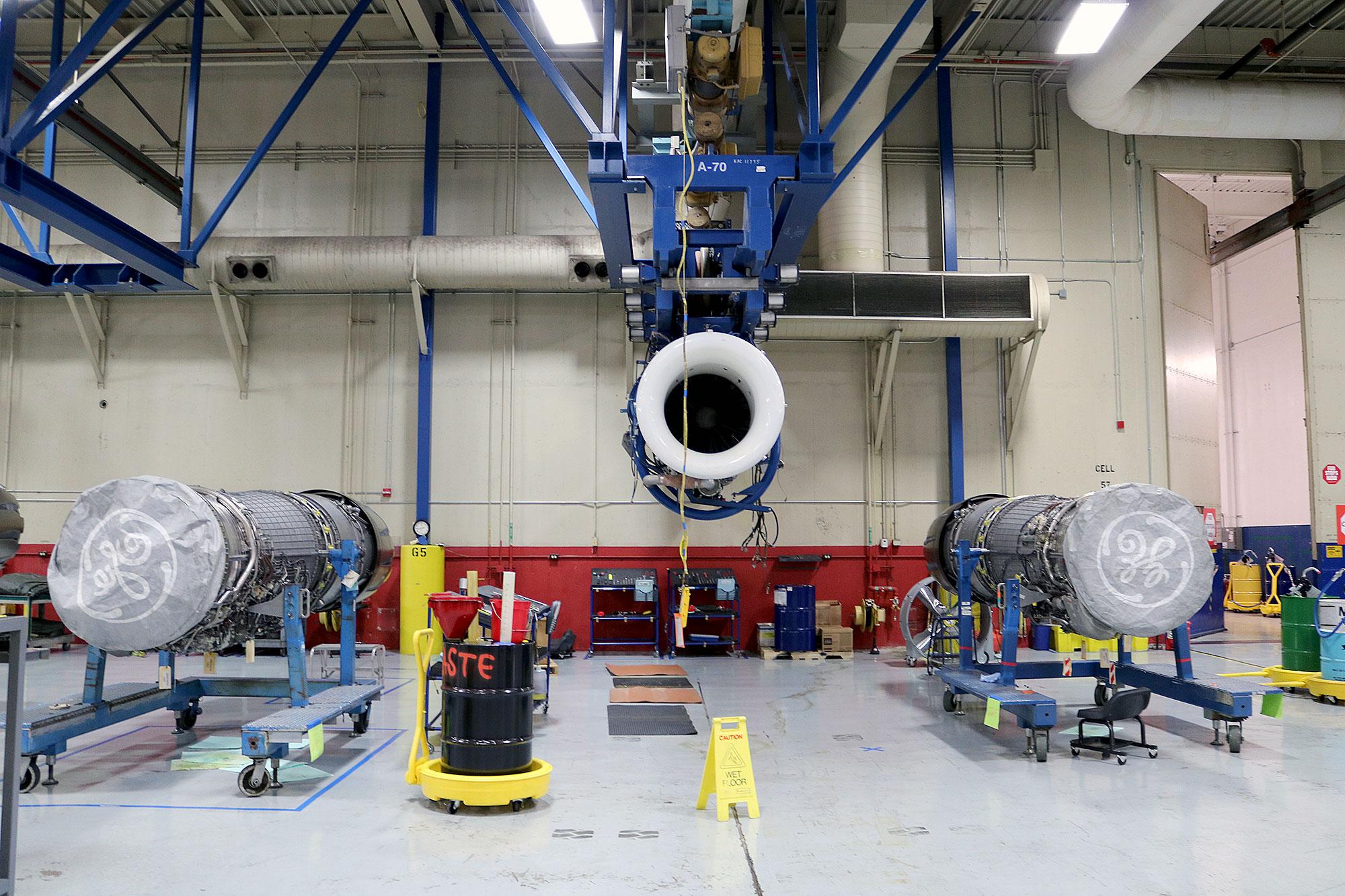
Credit: Lindsay Bjerregaard/Aviation Week
Last summer, StandardAero also inducted its first engine for the Pacer Pharaoh Program, which is a collaboration between the MRO, GE Aviation, the U.S. and Egyptian Air Forces, and Defense Logistics Agency. StandardAero is providing engine level disassembly, reassembly and testing for GE F110-100 engines for F-16 Falcon aircraft.
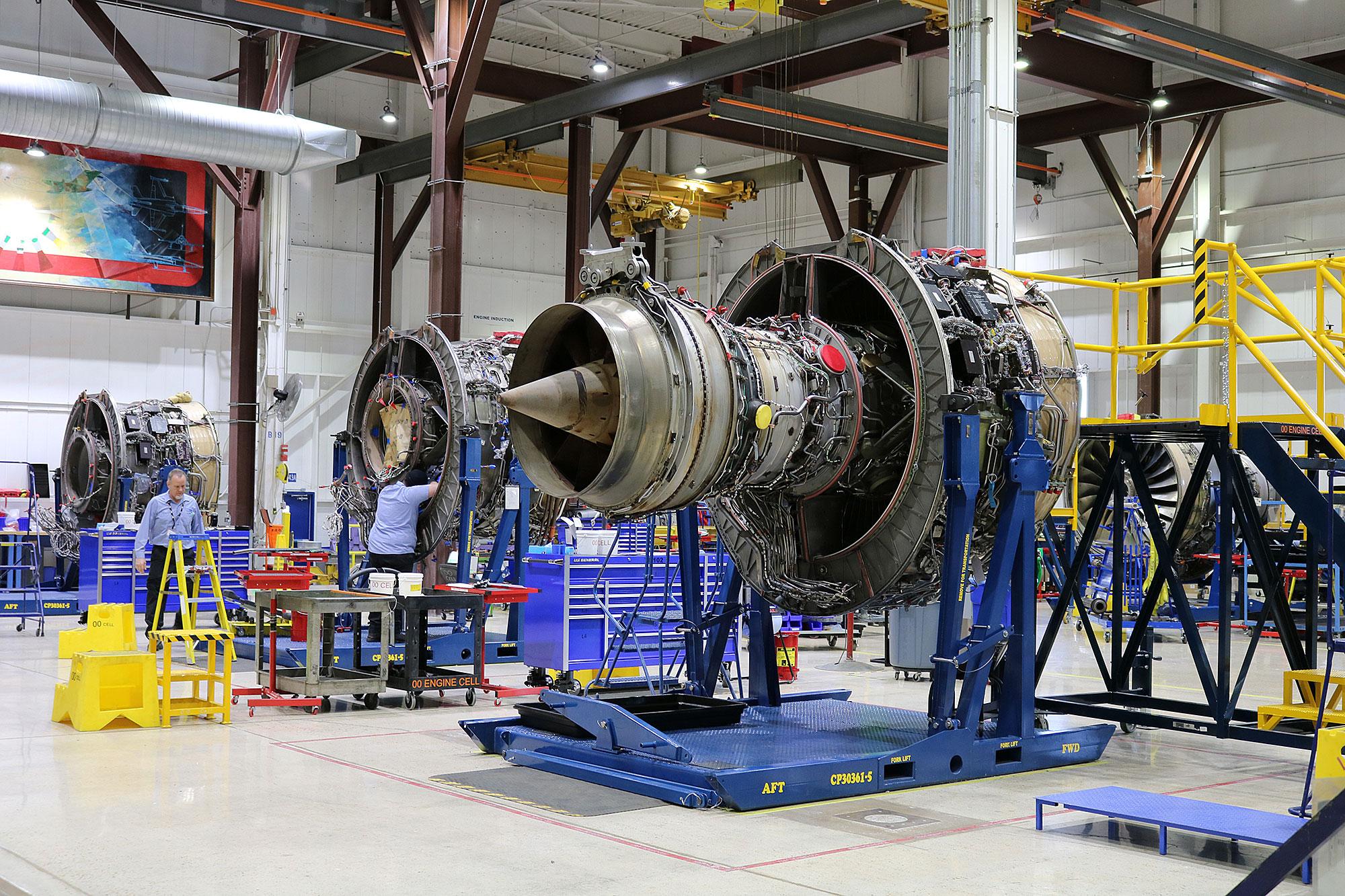
Credit: Lindsay Bjerregaard/Aviation Week
With its commercial aviation business the hardest hit, StandardAero expects engine MRO volumes to stay low throughout 2020.
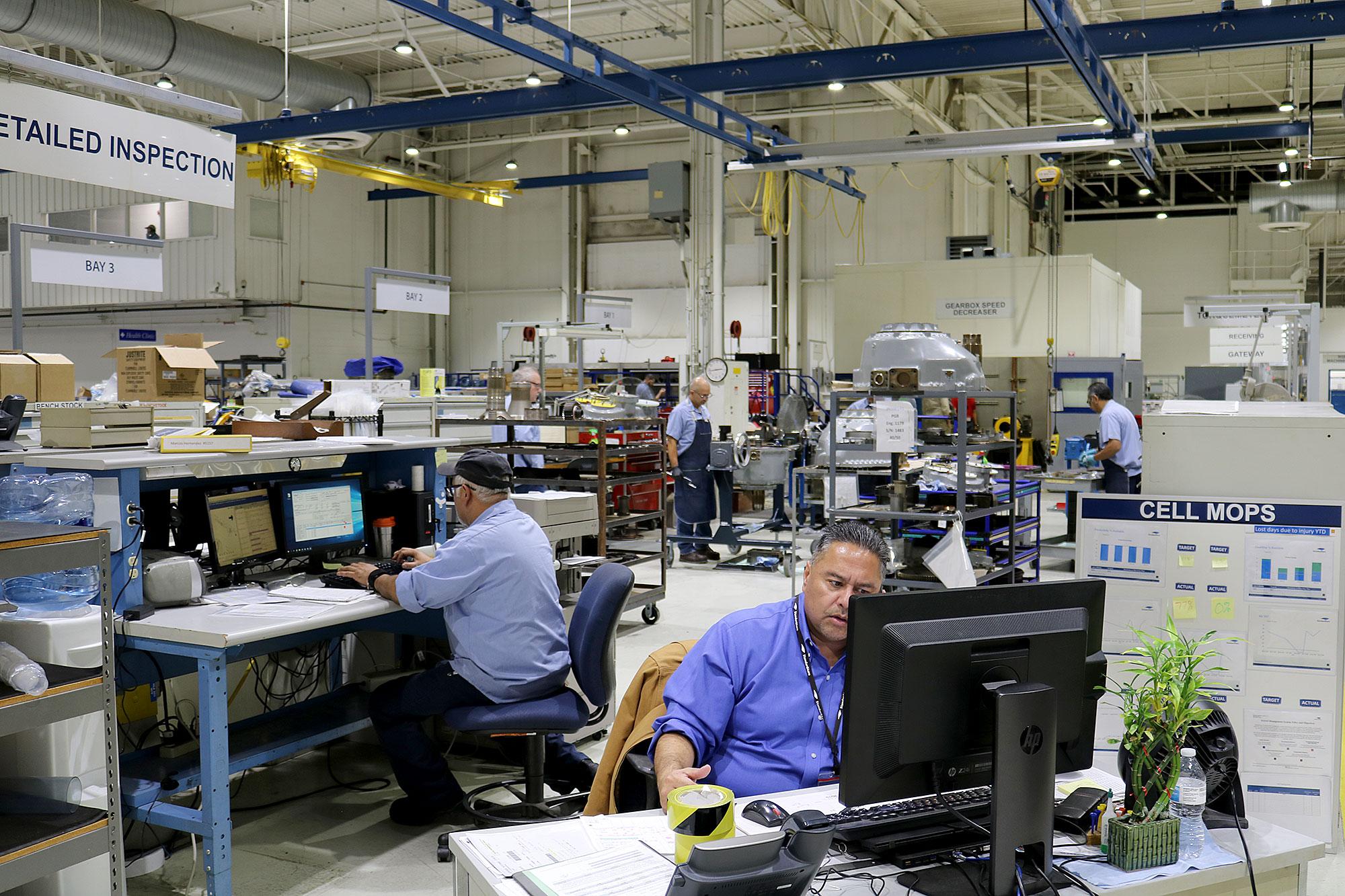
Credit: Lindsay Bjerregaard/Aviation Week
Also continuing to grow is the site’s technology innovation. StandardAero San Antonio runs a totally paperless operation using an enterprise MRO system tailored to support third-party MRO. Buongiorno says the system “touches every aspect of StandardAero’s MRO business,” including managing, planning and overseeing work as it transitions through the floor.
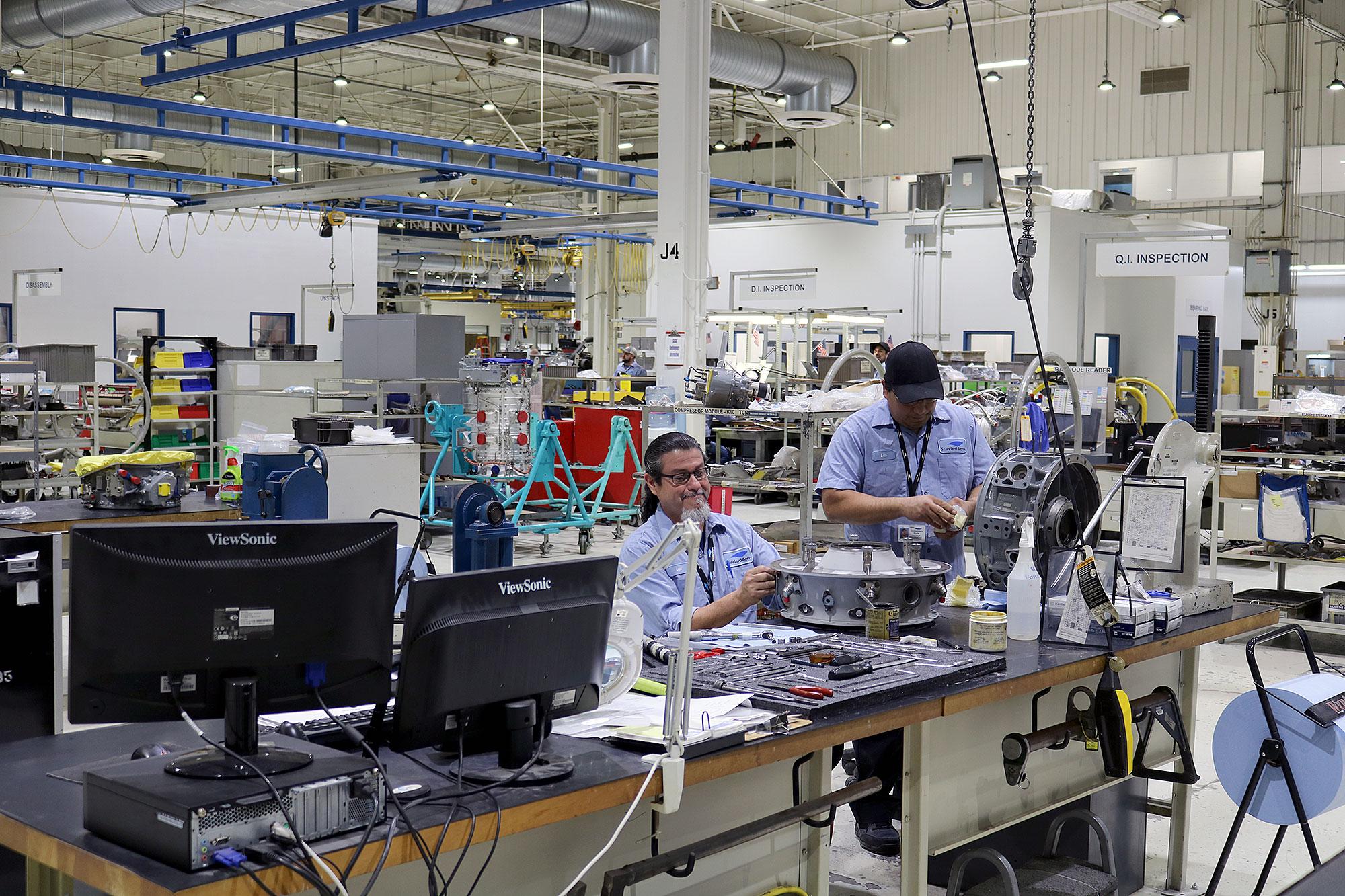
Credit: Lindsay Bjerregaard/Aviation Week
Technicians use tablets to access technical data, record inspection results and track labor and time. The system is also used for supply chain management, so when parts are inspected and designated as serviceable, repairable or scrap, it triggers the next step in the process—such as placing orders with parts providers.
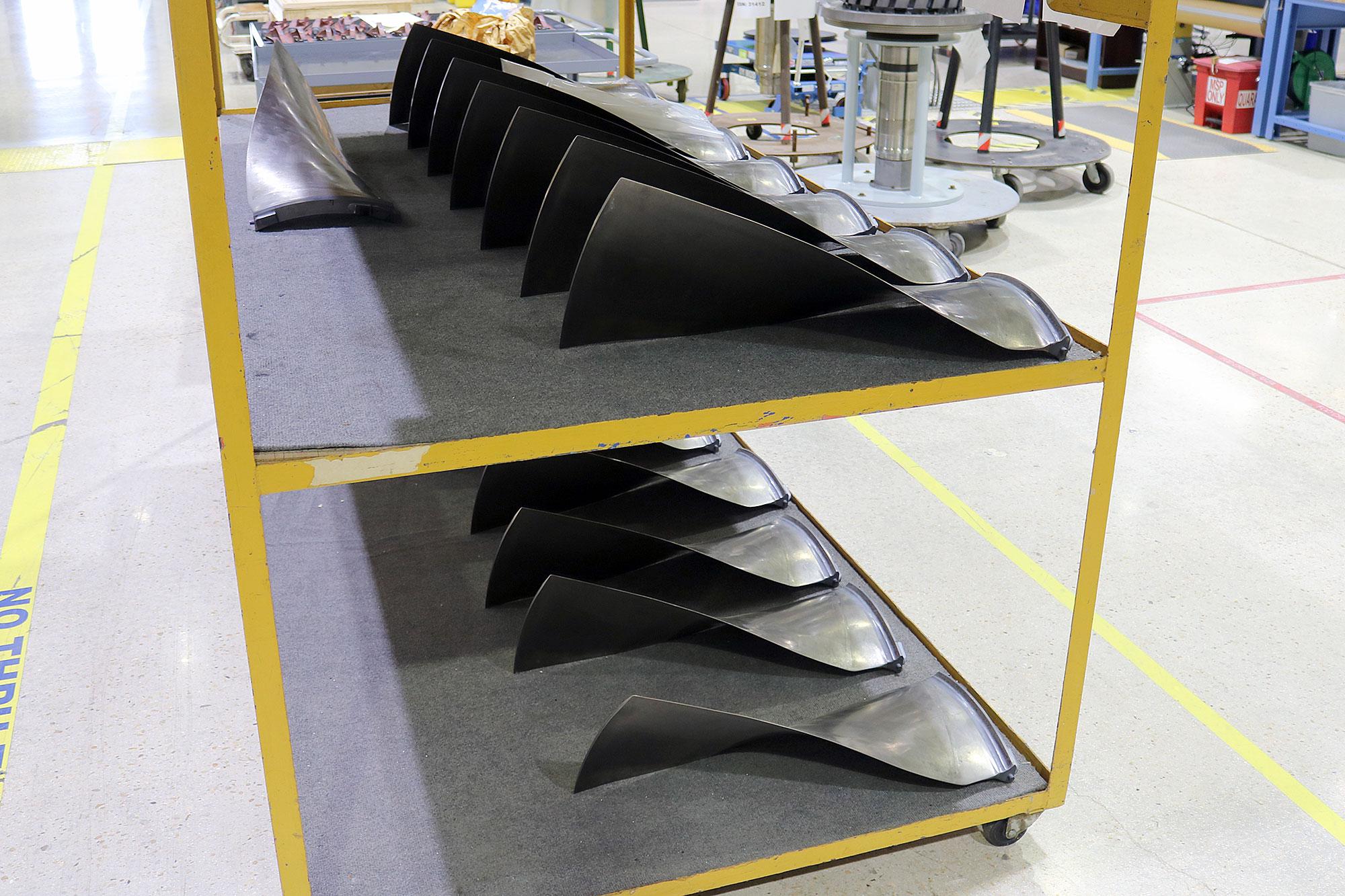
Credit: Lindsay Bjerregaard/Aviation Week
In terms of future technology implementation, Buongiorno says the site is looking at RFID for tooling tracking, 3D inspection technologies and laser measurement systems. He adds that laser measurement systems could be particularly helpful for blade inspections while blades are installed on the rotor. “A lot of our rotor grind equipment is already fitted with laser measurement systems, so you don’t have to stop your operation, break out a set of calipers or a large micrometer, or use some kind of integrated gauge, which is very time consuming,” he says.
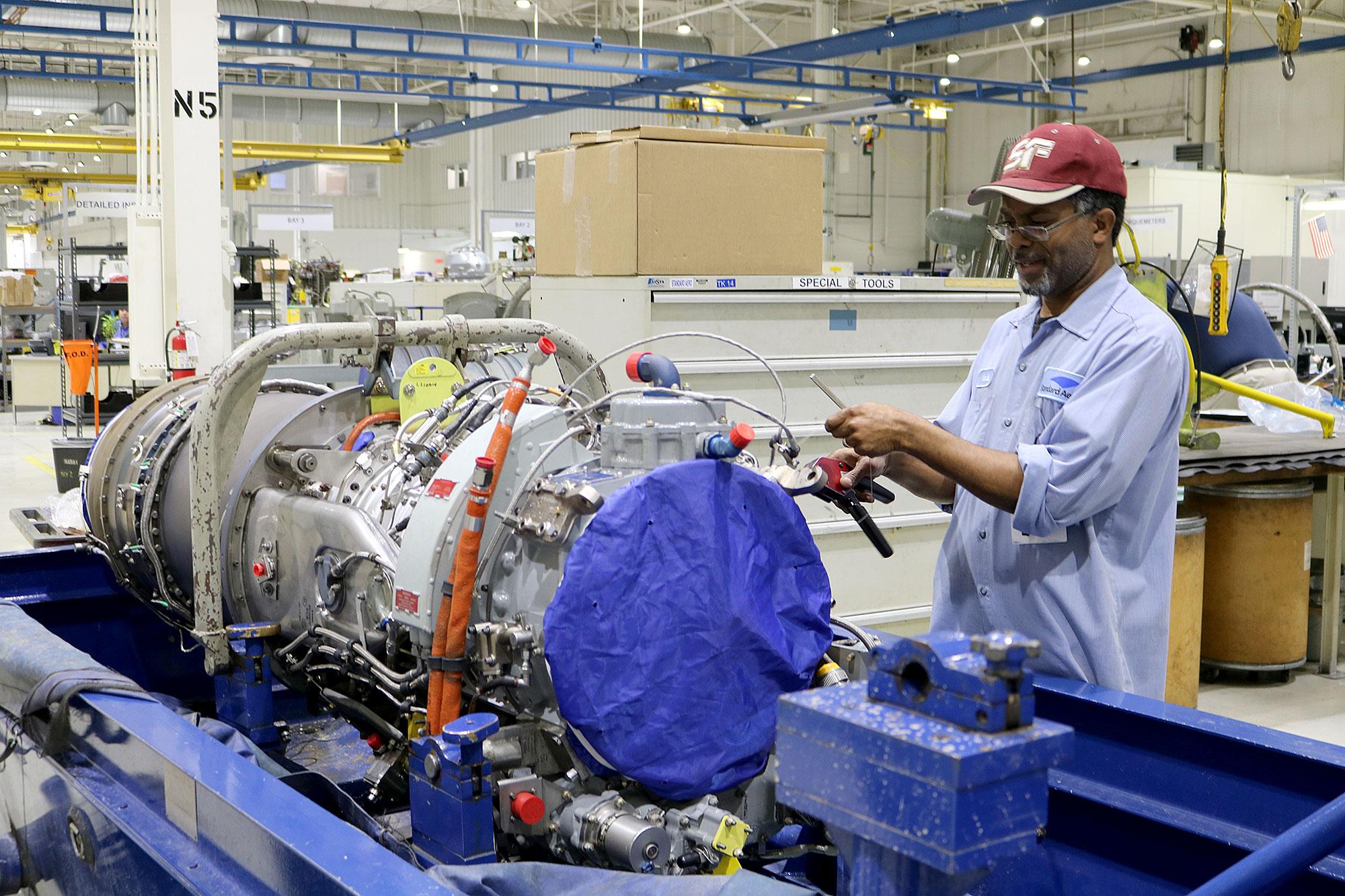
Credit: Lindsay Bjerregaard/Aviation Week
StandardAero is also leveraging the site’s Port San Antonio location to collaborate with other aviation companies on projects and workforce growth. According to Buongiorno, StandardAero collaborates with neighboring Knight Aerospace in areas such as test cell usage and with Boeing on influencing the city of San Antonio to provide support for growth and awareness of aerospace.
As the site ramps up commercial and military engine MRO projects, Aviation Week gets an inside look at StandardAero’s engine MRO and test cell facilities.