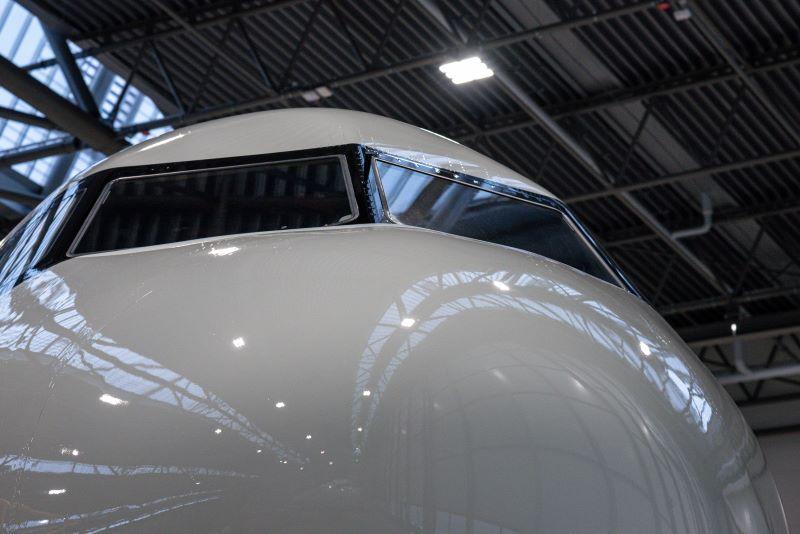
Industry input on the FAA’s proposed cockpit secondary barriers mandate is split into two distinct camps—those calling for more time to develop and roll out the safeguards and those concerned the new standards are both too narrow and not coming fast enough.
The FAA in July issued the draft rule, which proposes requiring installed physical secondary barriers (IPSBs) on all aircraft delivered within two years of a final rule’s adoption. The barriers, which would go between the front cabin passenger seating and the cockpit, add protection for when the flight deck door is open, such as when food is being delivered to the pilots.
Labor groups, led by several pilots’ unions, argue the mandate does not go far enough. The Air Line Pilots Association (ALPA), Coalition of Airline Pilots Associations and Southwest Airlines Pilots Association (SWAPA) want the new rules to go into effect within one year, pointing out that industry has been working on the issue for nearly 20 years. Technical standards are in place, and some carriers, such as United Airlines, have installed barriers.
More significantly, several groups, including ALPA and CAPA, want the mandate expanded to include both the current fleet and the estimated 3,400 foreign-carrier aircraft that serve the U.S. under FAA’s Part 129, mirroring requirements for hardened cockpit doors prompted by the 9/11 hijackings.
“There is a significant security concern that the flightdecks of foreign aircraft being operated into the United States under Part 129 could quickly become more attractive targets for terrorists or other bad actors if IPSBs are not installed,” ALPA told the FAA. “These security concerns are similar to those considered when the FAA adopted the reinforced flightdeck door requirements in Part 121 operations in 2002, which led to the FAA’s adoption of 14 CFR 129.28 requiring hardened flight deck doors for foreign passenger airlines operating within the U.S.”
Airlines, manufacturers, and their respective trade groups believe the proposal is too aggressive. Airlines For America (A4A) argues that the new mandate should apply to newly certificated aircraft, as opposed to all aircraft—including current-production programs such as the Boeing 737 MAX and Airbus A320neo. Current protocols such as using catering carts as temporary barricades are effective and adding new hardware to existing designs will create fleet-commonality headaches, the association argued.
“Application to only newly type-certificated aircraft will avoid non-commonality issues within fleets (or sub-fleets), which include unnecessary and unjustifiable increases in aircraft purchase, post-purchase reconfiguration (e.g., retrofit), maintenance, and crewmember training costs that have no measurable safety or security benefit,” A4A told the FAA.
A4A also said cargo airlines should be exempt, arguing that the 2018 congressional mandate behind FAA’s push to get the rule done specifically targets “passenger” air carriers.
“Without doubt, Congress excluded all-cargo air carriers and the FAA cannot read the legislative text as authorizing applicability to all-cargo air carriers,” A4A said.
Airbus, Boeing and Embraer expressed concern with the lead time needed to develop, certify and produce the new barriers, arguing that a three-year timeline is more appropriate.
“Without an existing commercially available ‘drop in’ product it should be anticipated that significant effort would be required to develop, fabricate and certify one or more [IPSBs] to satisfy the proposed rulemaking,” Boeing told the FAA. “It should also be anticipated that due to various aircraft interior architectures and configurations multiple IPSB’s will need to be developed concurrently. Typical product development programs that impact multiple airplane models, interior configurations, and require new methods of compliance require closer to 36 months (3 years) from start to finish,” the U.S. manufacturer added.
“A typical new product development can take 12 months just to develop specifications, solicit responses from suppliers, and award contracts,” Airbus said in its comments on the draft rule. “The following product development and qualification phases and finally the industrialization of the qualified designs will need a full 36-month period. Hence, a compliance period of three years is better suited to successfully bring these solutions to market.”
A4A also called for a 36-month implementation period if the new standards are not limited to newly certificated aircraft, while the Aerospace Industries Association echoed the manufacturers’ views.
“These new designs would have to go through the FAA’s certification process and two years does not provide adequate time,” AIA told the agency. “Therefore, a 36-month timeline for compliance would be more appropriate. This would ensure that manufacturers would be able to work with FAA to bring the applicable aircraft into compliance with this new requirement.”