Gallery: Key Takeaways From Aviation Week’s Digital Transformation Summit
Lindsay Bjerregaard October 12, 2023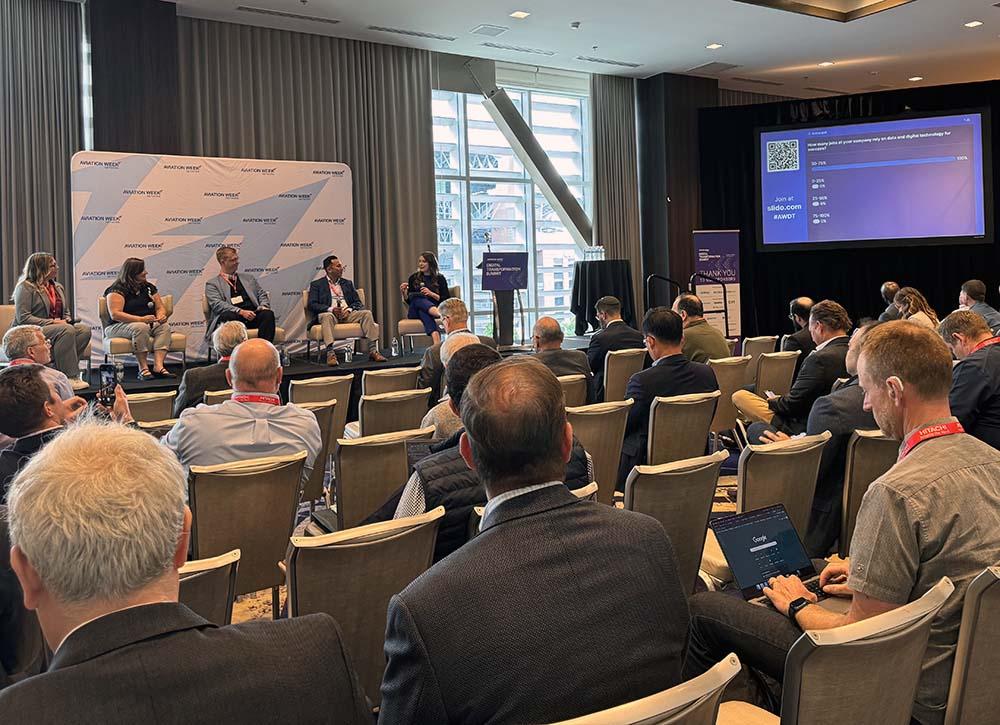
Stakeholders from across the aerospace, defense and commercial aviation markets gathered at Aviation Week’s 2023 Digital Transformation Summit in Seattle Oct. 3-4 to discuss key data and digitalization issues impacting the industry. Read on for some of the key insights from the conference, including workforce impacts, data concerns, best practices and barriers to new technology.
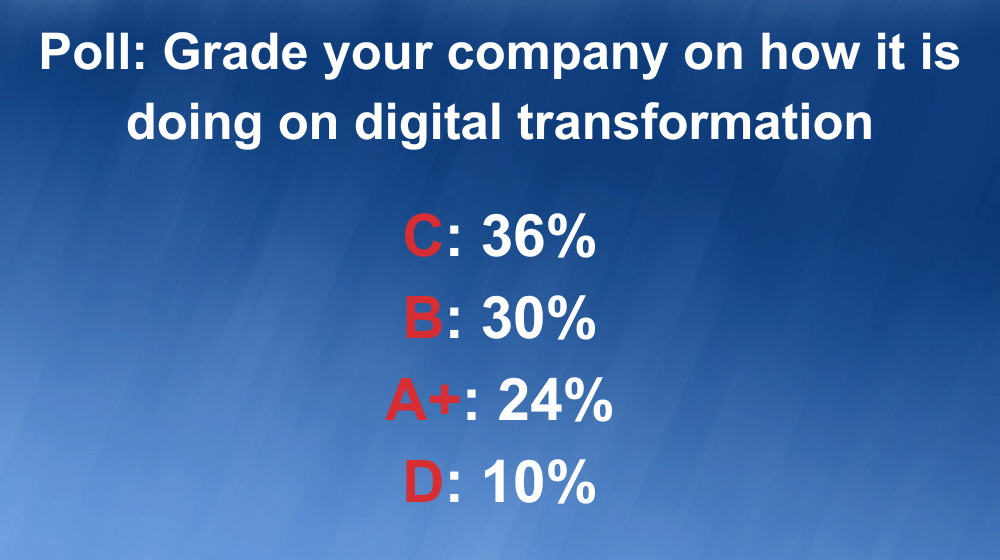
Digital Transformation Progress
Most conference attendees seemed to think their companies are headed in the right direction, but still have room for progress when it comes to digital transformation. In response to a poll asking respondents to grade their companies on digital transformation progress, the majority of people rated their company’s performance at a B or C level.
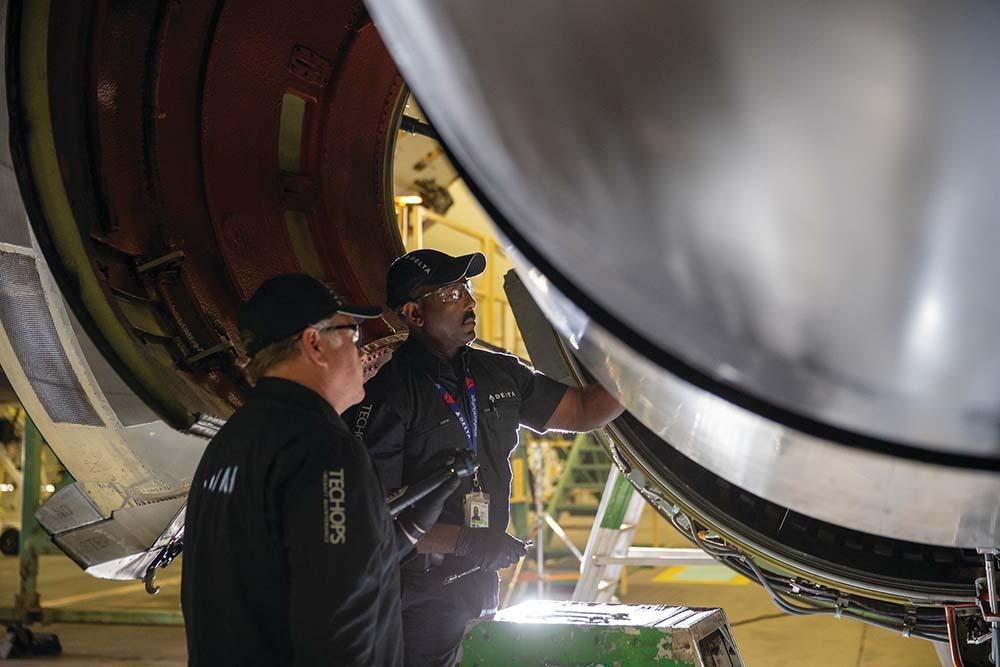
Addressing The Workforce Shortage
Much of the conference’s discussion revolved around how technology could be used to address the industry’s workforce shortage. Amanda Bramlett, manager of engineering analytics at Delta Air Lines, stressed the significance of the problem. “Delta had a bow wave of retirements looming, but with the pandemic it wasn’t a trickle, it was a flush,” she says. “We had a collective 57,000 years of experience that walked out the door and that’s a tremendous loss. We do our best, but filling that experience gap is quite a mountain to climb.”
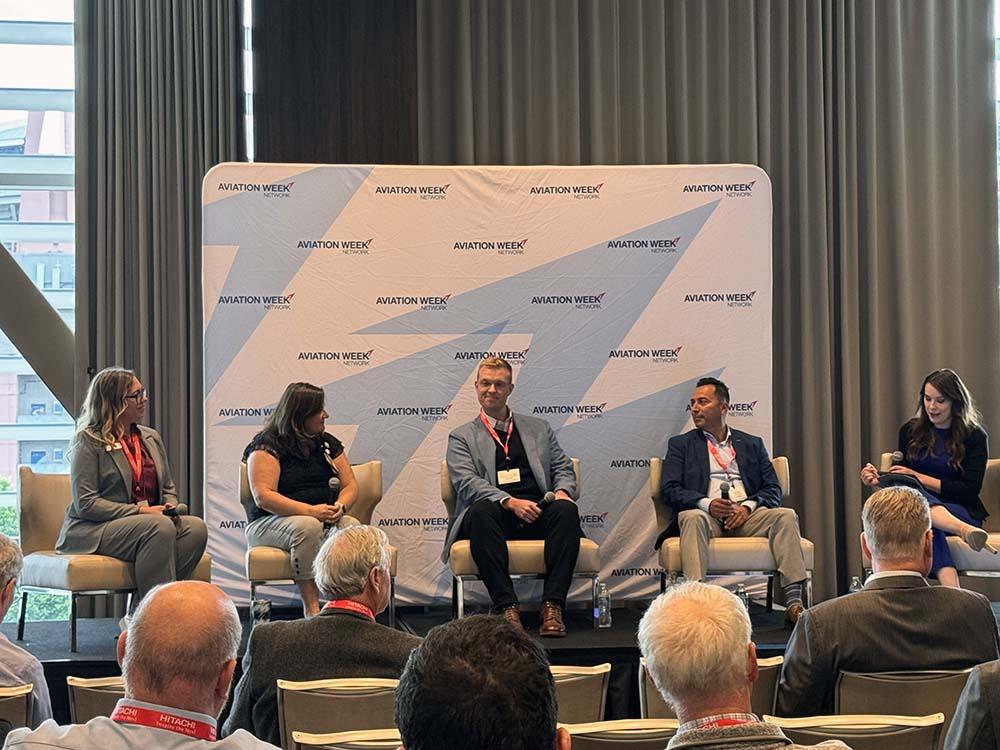
Technology Training Considerations
Although the consensus at the conference seemed to be that technology will be crucial for accomplishing more with a leaner workforce, several panelists cautioned that good technology training strategies must be in place.
“The technology changes so fast,” says Amanda Brown, director of digital and agile transformation for military development programs at Pratt & Whitney. “If you wait until you have the perfect solution, it’s going to be out of date before you even get it out there, so building the budget and time for training into our workforces’ calendars is going to be an expectation that we want to look to our leaders to set. I don’t think it goes away. We are never finished with digital transformation—it’s a new way of life, so there’s always work to be done.”
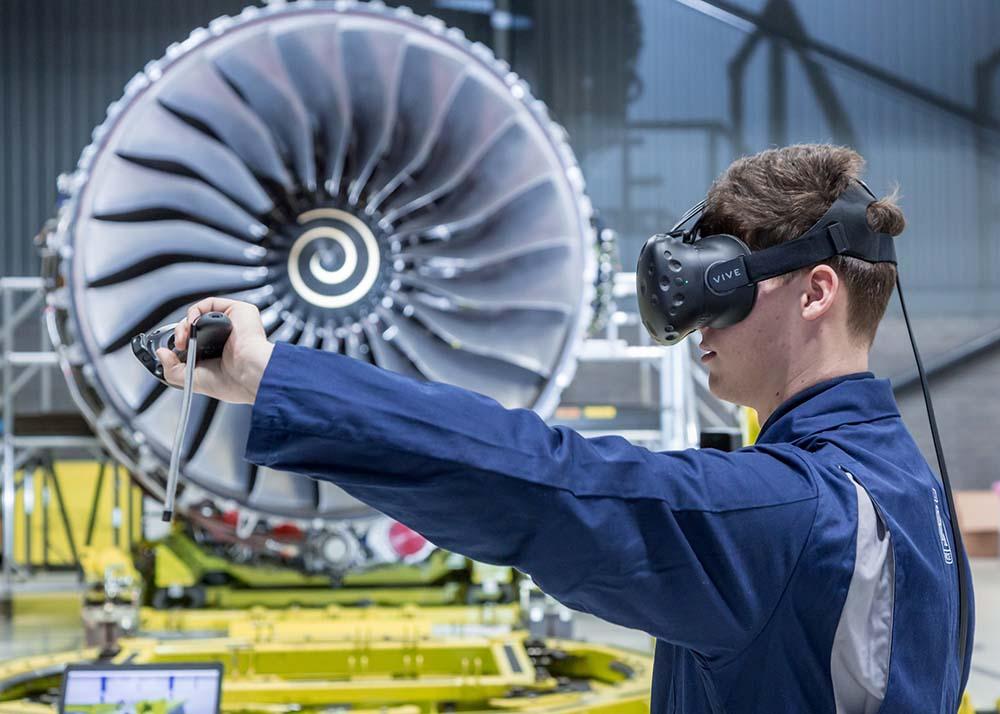
Technology Training Considerations (Continued)
Nicole Ellis, senior director of business intelligence at TrueAero, argues digital skills should be a priority for success. “Our executive teams have to be shouting this from the rooftops. They have to be enforcing this in our key performance indicators and making sure that we’re all making it a priority for ourselves and our teams to upskill,” she says. “And it’s not necessarily just making people digitally savvy—it’s also the soft skills that are now more required than ever to be able to communicate in a digital first environment that so many of us still need and maybe have not gotten in our careers in this industry so far.”
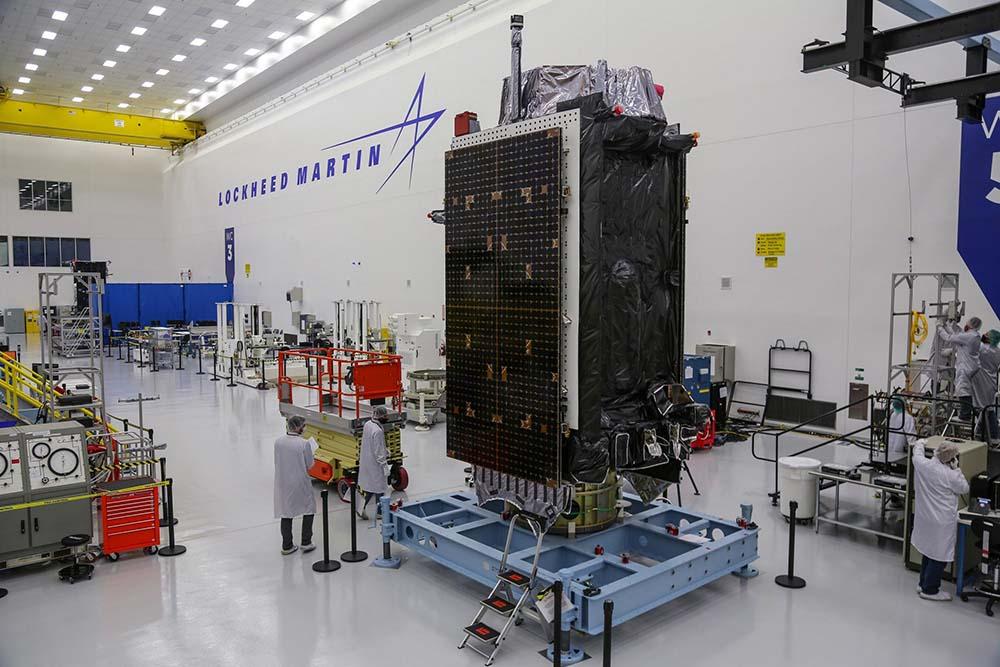
Technology And Labor Concerns
As part of recent labor contract negotiations at some of its facilities, Lockheed Martin Aeronautics considered its workforce’s technology concerns. “We’ve been able to strike new job codes that didn’t exist based off how we’re going to harness technology and how the future of manufacturing is shifting,” says Travis Reed, operations strategy and technology director at Lockheed Martin Aeronautics.
“We’ve been able to work together with the union teams to insert technology, and have technology review councils that consider the impact on upskilling and training. It’s really a matter of working toward synergies and goals that are mutual wins. We’ve had some really good examples where we’ve been able to introduce technology and continue to mature the thinking, even to the point where we have team members bringing ideas forward of mundane tasks [that could be automated.] Often, it’s clear where automation and solutions like that can benefit the employee from an ergonomic or injury reduction standpoint, so it’s about listening to the team, driving those insertions to be smart and not overdoing it.”
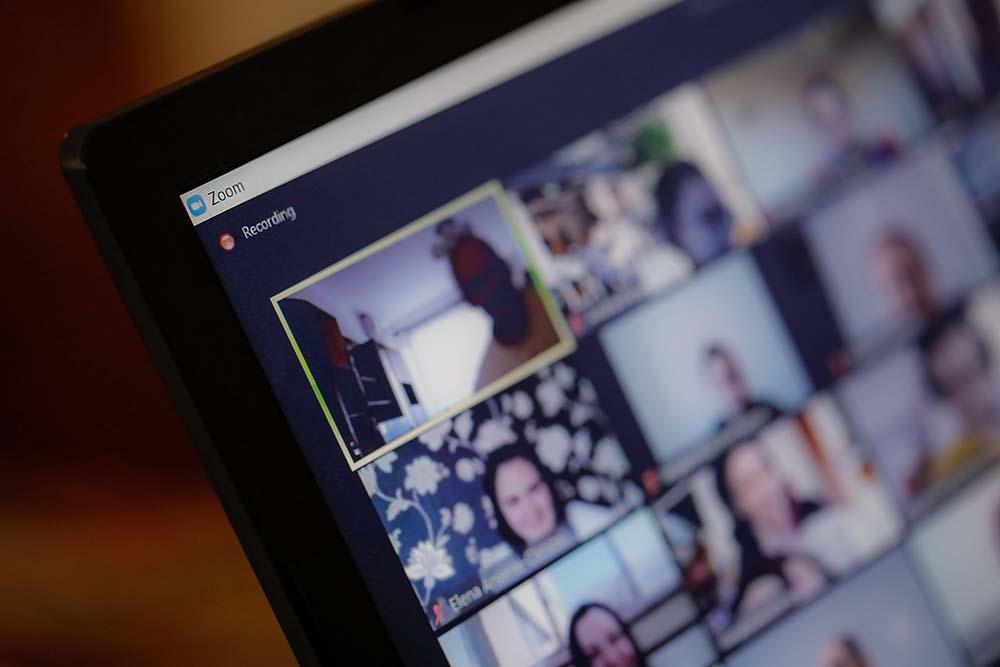
How Digitalization Has Changed Workforce Attitudes
Mike Dunlop, CEO and founder of Autonomous Machining, argues the eight-hour work day is not designed for the digital world. “One of the structures that has changed dramatically because of COVID-19 has been the eight-hour workday,” says Dunlop. “We didn’t mean to do it, but we created a massive incentive for people to do their work better. We sent them home, we expected them to do some work and suddenly they realized they were incredibly incentivized to take that eight hours of work and use every technology that’s available to do it in one hour.”
Dunlop also addressed a barrier holding back the use of technology to solve the loss of industry knowledge that has accompanied a wave of industry retirements coming out of the pandemic. “One of the big threats that keeps technology out is tribal knowledge. If I’ve spent my whole life learning something then I don’t want to share it with anybody—that’s my job, my leverage and my pay. You want me to share it, digitize it and make it simple? You’re asking me to sacrifice myself for the idea of technology,” he says.
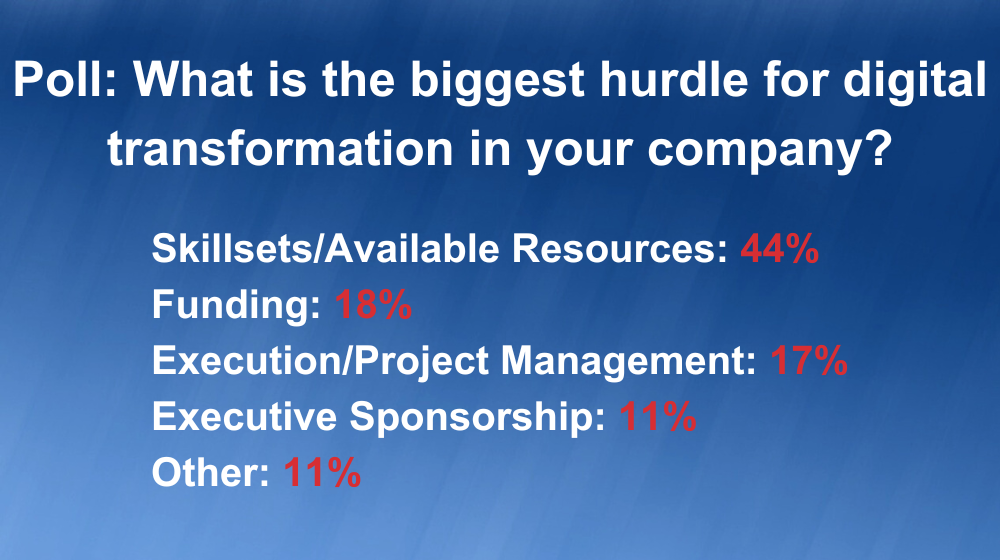
Barriers To Digitalization
Discussions during the conference evaluated many different barriers to digital transformation, but the consensus appeared to be that people power was the main hurdle. In an audience poll about the biggest hurdles for digital transformation at attendees’ companies, the majority of respondents chose “skillsets/available resources.”
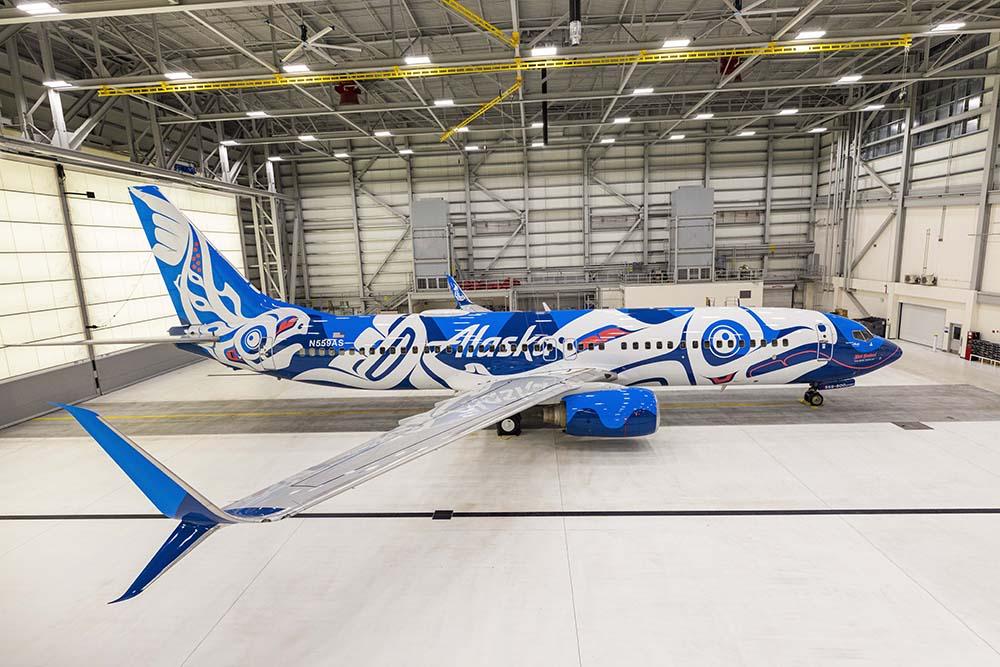
Sharing Maintenance Data
Several panel discussions addressed concerns around data ownership and sharing between OEMs, airlines, MROs and other industry stakeholders. Panelists from Alaska Airlines and Delta Air Lines responded to the following question: “How can an OEM convince an airline to share more maintenance and operational data?”
Bret Peyton, managing director for standards, fleet and operational control at Alaska Airlines: “We have to know as much about the data, its disposition and where it goes from day one, and then internally we have to have buy-in from internal stakeholders across divisions, including maintenance and flight ops. Maintenance might want something for an e-logbook or something like that, which is really useful, but we have to realize that they’re cross-divisional. Even at a small company, there are different stakeholders and they all have to be happy, so speaking to them in a holistic organizational mindset when you’re walking in the door will really help.”
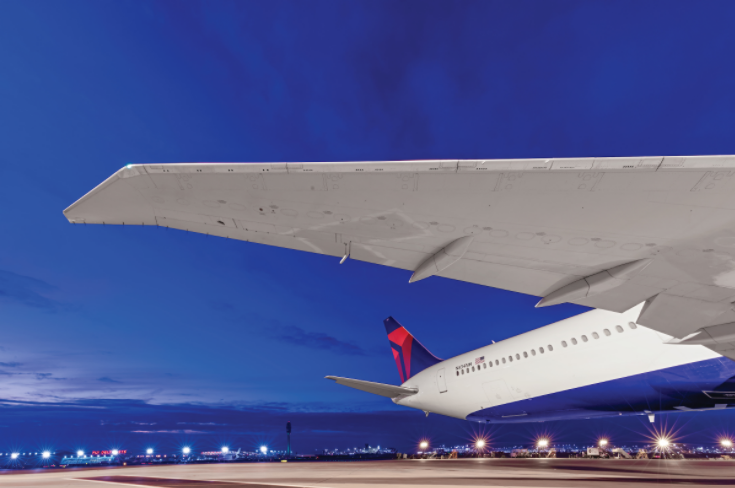
Sharing Maintenance Data (Continued)
Dustin Ames, manager of predictive technology engineering at Delta Air Lines: “I’d say, ‘What are your plans for the data? What is the OEM hoping to achieve if we provide the data? Is this a product or operational improvement of some sort. We’re both looking for the same data for very similar purposes except for the design. The airline is not looking to redesign any components that are failing—we’re relying on the OEMs to do that job. We are using [the data] for predictive purposes, so we’re not looking to take anybody’s intellectual property.”
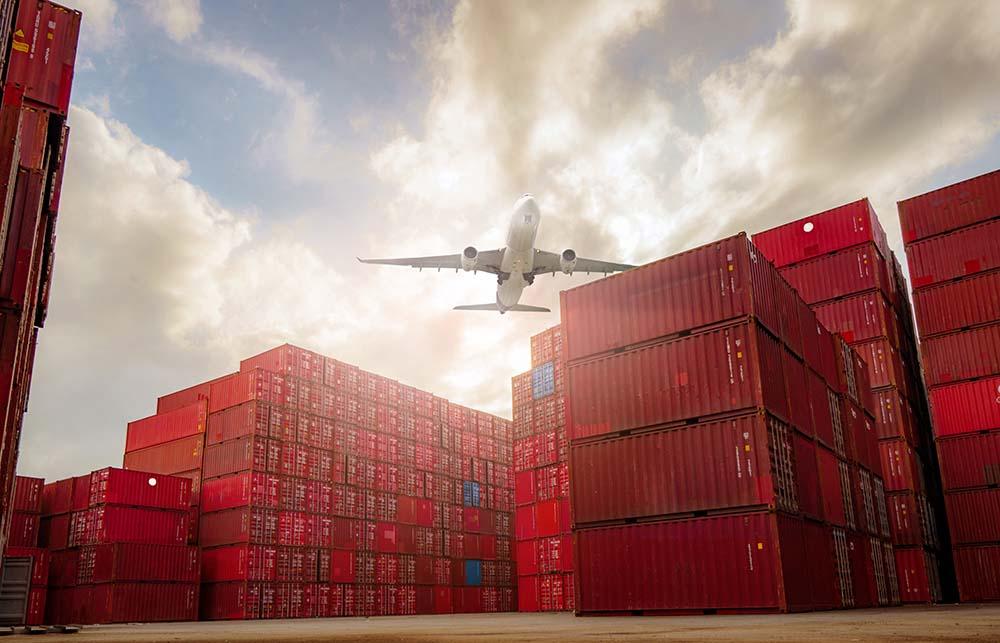
Embracing A Sharing Mindset
During a discussion about companies’ hesitancy to share data, Derek Baggery, CEO of SupplyOn USA, argued that the problem stemmed from attitudes, not technical constraints. “A lot of these things aren’t technology problems anymore, they’re mindset problems. Changing the mindset to more [data] sharing is good, and not just from the supplier side but from the customer side as well,” says Baggery. “There are some legitimate concerns [about sharing data] that need to be addressed either through creative technology or operations, such as saying, ‘Don’t tell me what your secret sauce is. Just tell me how many steps and how long it takes to get there.’ Today, I can track my Domino’s pizza from dough to oven to car to my door—why can’t I do that with a million dollar assembly?”
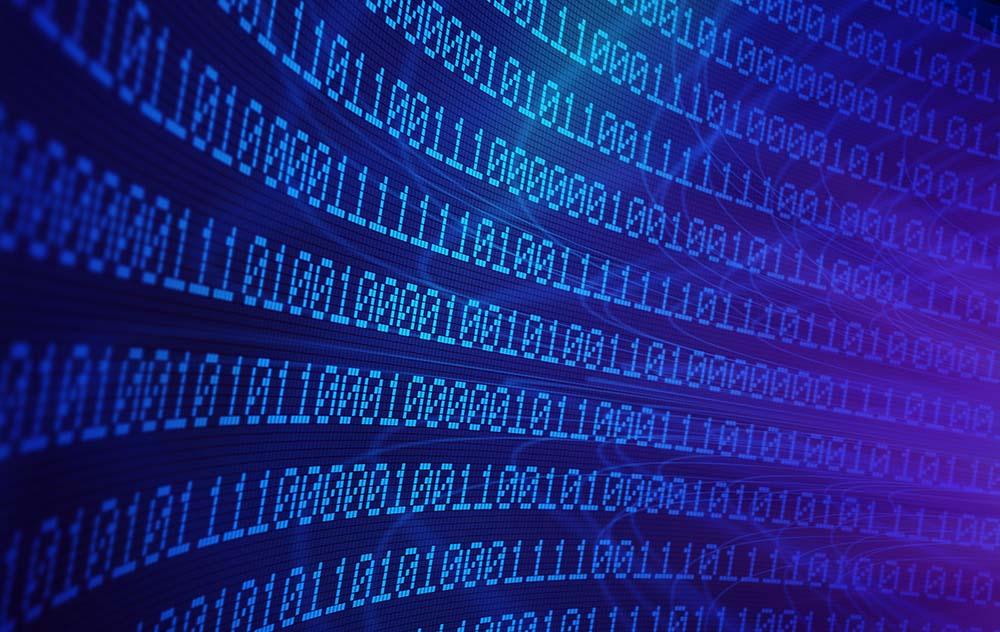
Addressing Dirty Data Concerns
Many panelists encouraged companies to consider a more open, collaborative environment when it comes to the data they collect. Emmeram Morning, president of supply chain automation specialist Robot Morning, shared his perspective: “We have a lot of [supply chain customers] who constantly say, ‘I’m not ready to share the data yet because it’s dirty.’ We need to flip that conversation. If you don’t go look at [your child’s room], it doesn’t mean the room is not dirty—it probably is. But it’s not until you actually go look at their room that you’re going to see the mess and anything’s going to be done about it. Sunlight is the best disinfectant. You’ll finally start paying attention and improving because there’s a customer who’s paying attention to the data, and that customer is now calling to tell me, ‘Your data is causing me a problem.’”
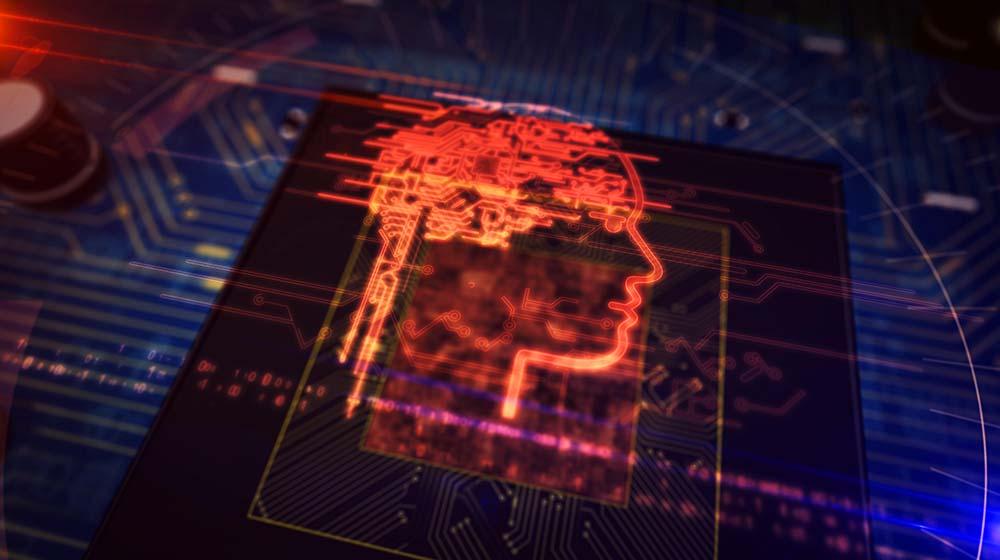
Weighing AI Benefits
Artificial intelligence (AI) was a hot topic in nearly every panel discussion at the Digital Transformation Summit. Although her startup offers AI technology for industries such as aviation, Loopr AI Founder and CEO Priyansha Bagaria asserts that the technology should be applied strategically. “Not every technology is applicable for every company. You don’t need to fit AI in everything—it doesn’t make sense,” she says. “The way to [approach it] is to start small, see [the technology’s] value and grow from there. It could be a quality inspection application on a factory floor. Try it out for two or three months, do a pilot and see the value of it, then expand from there. Because if you don’t have the business value, no matter how exciting the technology is, it’s of no use for you.”

Achieving Technology Buy-In
Even if technology leaders at A&D companies are convinced technology can solve recurring headaches, some panelists stressed the importance of working across teams to get buy-in from all stakeholders impacted. “Bringing [IT teams] in early to get their buy-in is almost even more critical than making sure [technology] is viable on the shop floor,” says John Mathis, manager of technology development engineering at Delta Air Lines. “You’ve very likely to get executives involved and they’ll get very excited about [technology], but it’s that middle group of people (i.e. technicians) who are incredibly important. Getting feedback on what’s going to work for them is a critical juncture in being successful.”
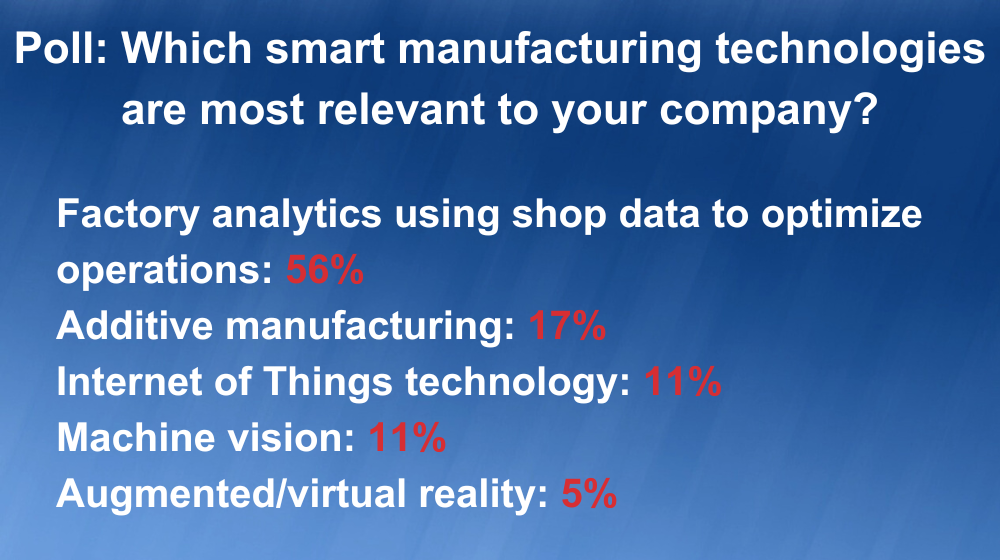
Smart Manufacturing Technologies
Although many emerging technologies have received hype in recent years as a way to make industries such as aerospace manufacturing more efficient, many stakeholders believe simple data analysis may prove the most useful. In an audience poll of attendees at the conference, 56% of respondents chose “factory analytics using shop data to optimize operations” as the most relevant technology over additive manufacturing, Internet of Things, machine vision, and augmented and virtual reality.
Industry insights on data and digitalization for aerospace, defense and commercial aviation.