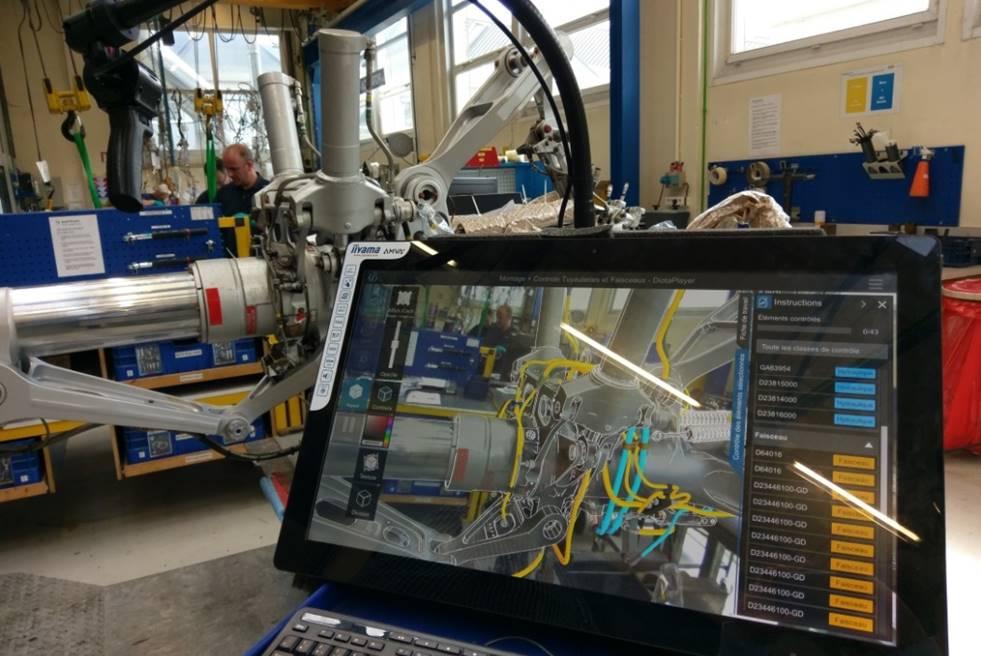
Safran Group is using specialized augmented reality (AR) and robotics tools from French startup Diota to improve efficiency and accuracy on the shop floor. The aerospace group is leveraging Diota’s technology for a variety of manufacturing and MRO use cases across many of its business units, including Safran Aircraft Engines, Safran Landing Systems, Safran Nacelles and Safran Seats.
Safran began working with Diota in 2015 and in 2016 made a 3 million euro ($3.57 million) investment in the startup through its venture capital subsidiary Safran Corporate Ventures, which it said would help accelerate the development of Diota’s technological solutions. Within its manufacturing activities, Safran is using Diota’s Digital-assisted Operator product, which provides fully contextualized work instructions via AR to help workers more easily and efficiently assemble complex products, such as aircraft fuselage electrical harnesses or engine components. It can also automatically detect compliance problems, such as incorrectly positioned or missing elements.
It is also using Diota’s Digital-based Robotics tool for tasks such as quality inspections, which automatically programs the movements of robots to carry out inspections. According to Diota, this has benefits for applications such as inspections of aircraft engines after final assembly, since the robot can automatically check approximately 600 elements in an hour and send a report of conformity to a quality engineer located anywhere in the world.
Safran Landing Systems is using Digital-assisted Operator to track, trace and report on MRO processes more efficiently. According to Francis Rossignol, vice president of SMART Factory solutions at Safran Landing Systems, this is helpful for use cases such as maintenance on an A320 landing gear, which has up to 40 different configurations for its lock arm. Landing gear require an inspection upon arrival at Safran’s workshops, and prior to Safran’s implementation of Diota technology, Rossignol says this process took four people and significant work to copy and paste photos, so reports were not very customized for customers. Rossignol says Diota’s technology has simplified this by enabling only one worker to complete this task in significantly less time than it previously took. He also says Safran has had 10-12% gains in operating time for tasks such as paint masking.

Dassault Aviation is using Diota's augmented projection technology to pin work instructions directly on aircraft wings.
According to Arthur Brassart, head of sales at Diota, one element that makes its Digital-assisted Operator AR tool unique is the ability to not only deliver AR work instructions via tablet or computer screens, but by projecting relevant information on an actual work surface.
“We are one of the few companies in the world that is able to offer augmented projection,” says Brassart. “When you have AR, most of the time you see the digital content through the screen, but that requires you to have something in your hand. We developed an augmented projection system that not only shows you on the screen what you have to do and what is superimposed onto your physical object, but we project information directly on your work zone so you don’t have to carry anything.”
The augmented projection system is being used by aerospace customers such as Dassault Aviation, which uses it to pin work instructions directly on the wings of Rafale aircraft and to digitally mark up surfaces instead of performing markings manually with chalk. According to Dassault, the technology helps workers know exactly where to carry out the right tasks on aircraft structures.
Brassart says approximately 70-80% of all aerospace manufacturers or suppliers in France and Europe are now using Diota’s solutions for tasks such as MRO, training, quality control and assembly manufacturing processes. According to Brassart, Diota’s technology products are designed to be “plug and play” by being device agnostic and requiring no IT development for integration. Diota’s software connects with common manufacturing execution systems (MES) and product lifecycle management (PLM) software.
In June 2020 Diota launched what it calls the 4X Generation of its products, which shifts to a cloud-based model where customers can select various modules on the Diota AppFactory platform. Brassart says the “ecosystem of modules” includes functionality for technology such as digital twins, analytics and connected tools via Internet of Things.