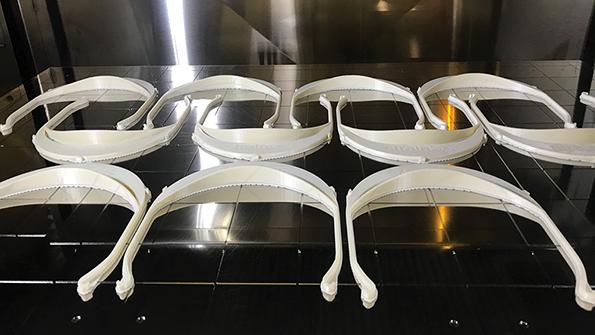
As aerospace OEMs face production cuts, layoffs and liquidity challenges in the midst of the novel coronavirus crisis, the suffering supply chain may force the industry to move more toward innovative solutions such as additive manufacturing (AM) to meet demand for aircraft components and tooling.
Chicago-based AM specialist Fast Radius is finding that additive’s ability to ramp up production quickly in uncertain times makes it a valuable piece of the supply chain—as evidenced by its role in increased production of medical equipment such as face shields and parts for ventilators.
“That’s really kind of proven out over the past month or so here, and similarly we’re seeing the same situation with other customers such as those in aerospace or large industry where, especially earlier this year when the virus was over in the [Asia-Pacific] region, they were experiencing supply shortages. We were able to meet some of those demands by converting some of those products to additive to be able to ensure that they were still able to operate their factories,” says Matt Schroeder, senior application engineer at Fast Radius.
“It’s really offered an interesting alternative without the need to convert the entire manufacturing line over to an entirely new process that it hasn’t been equipped for,” says Schroeder. “Additive allows for a much quicker digital alternative to cutting an injection molding tool or setting up a line for stamping or any other traditional manufacturing technology where it just takes a very long time to ramp that up.”
Scott Sevcik, vice president for the aerospace business segment at Stratasys, notes that U.S. aerospace companies with 3D-printing expertise were called upon by the government during the COVID-19 crisis to help produce medical equipment for the Federal Emergency Management Agency, and they were able to deliver it within just a few days.
“An industry that’s often viewed as stodgy and cumbersome really turned on a dime, and they could do it because they’ve built up a level of expertise with industrial 3D printing and equipment,” says Sevcik. “I think what it demonstrated very loudly within those organizations, and hopefully even more broadly to organizations that haven’t started down that path, was that the technology can be effectively used within aerospace to effect rapid change, which is exactly what you need when you’re looking at the challenges an MRO environment experiences.”
Paula Hay, vice president for advanced manufacturing engineering and technology at Collins Aerospace, says additive has demonstrated its ability to adapt quickly to the current environment, but that does not mean it will be fast-tracked everywhere.
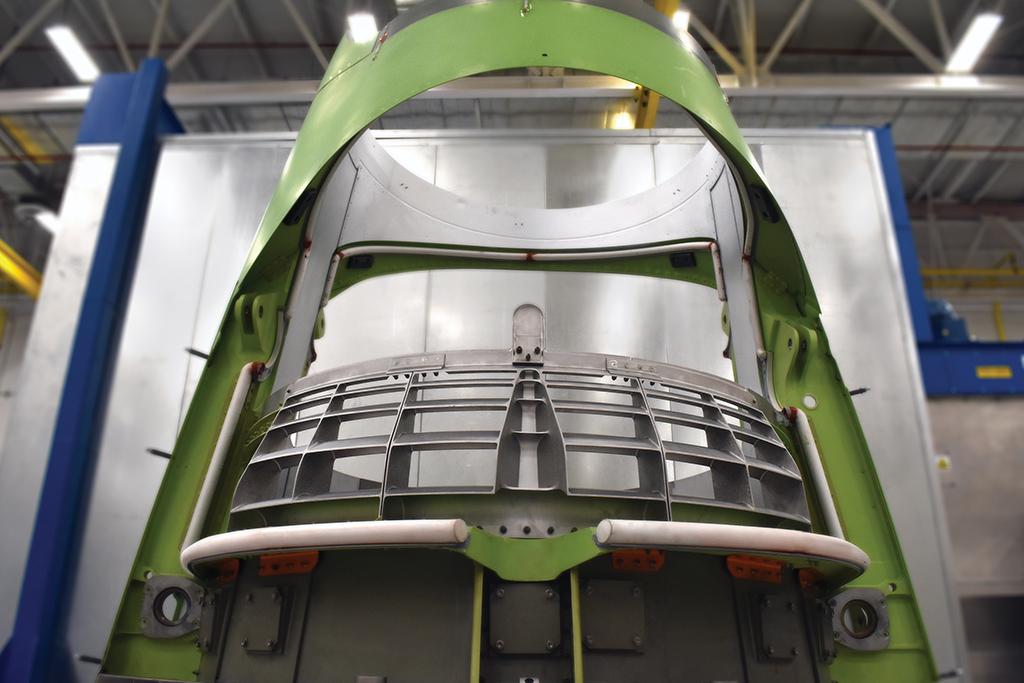
“Because there is so much uncertainty and slowdown in aviation right now, it’s not clear whether or not organizations will invest the resources to advance additive or reserve them for running daily operations,” says Hay. “If we do see an uptick in new adoptions, it will most likely be first in the area of tools and then spread more to parts.”
Sevcik notes that tooling remains a growth area within additive, and at Collins—which is in the process of creating several centers of excellence for additive—development efforts have started around directed-energy deposition to both repair damaged parts and build large-scale parts and tooling.
Additive materials themselves are also an area where both Stratasys and Fast Radius see innovation happening within aerospace. Fast Radius points to new polymer materials coming to market that are flame-, smoke- and toxicity-rated. Stratasys recently released its Antero material, which can “withstand oils, fuels and hydrocarbons better than any plastic that you’d typically see in 3D printing,” Sevcik says.
In recent projects with the U.S. Air Force, Stratasys has focused on innovations such as colored materials and printed textures to reduce post-processing, meaning parts can go straight from the 3D printer to aircraft. Fast Radius’ Schroeder notes that AM color technology also enables printing of elements such as logos, serial numbers and QR codes directly onto tools and parts. This can enable “true traceability across the entire product life cycle, where that QR code can be specific to that single product, and you can trace [it] all the way back to the machine that [it] was manufactured on.” Innovations like this could allow customers to scan QR codes to quickly order replacement parts or even have implications for blockchain record-keeping systems.
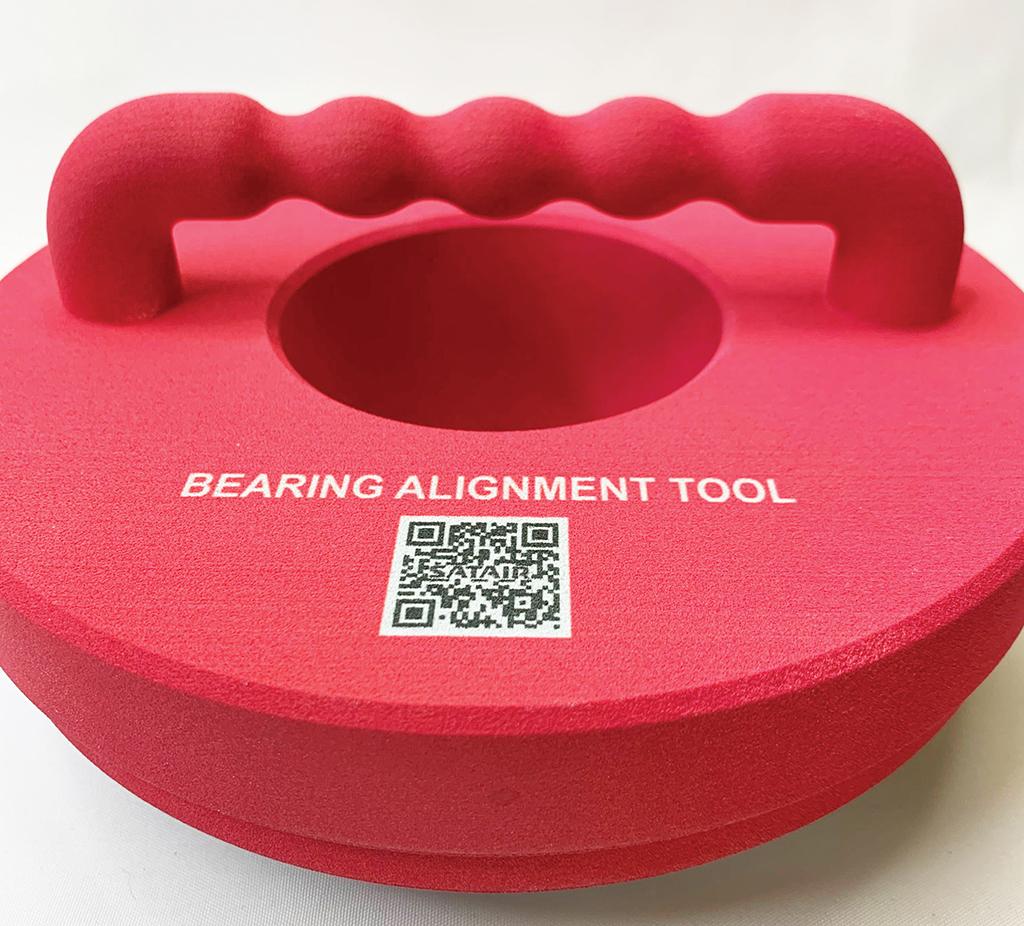
Schroeder believes that some 3D-printing innovations taken from other industries—such as automotive or consumer goods—could also have applications for aerospace. Fast Radius has already created 3D-printed electrical connector parts for automotive uses and is now working with a large aerospace OEM that manufactures electrical components for aircraft.
Schroeder says the 3D-printed electrical connectors can be customized based on a customer’s requirements. “For instance, if there’s a very low-volume application with new electric flying aircraft, we can very quickly design a connector that’s able to meet that application without the need for any capital investment or the need to cut a tool, so we can very quickly ramp up those connectors in the product development cycles,” he says.
“Often we’ll see customers use it for testing in the initial stages, but then also as either a bridge to tooling—where it makes sense to make the first, say, 10,000 using additive before converting over to traditional methods. Or, in some cases, we’re actually able to achieve a performance improvement by using additive, and, if it makes sense, to produce using additive throughout the entire life of the program,” he adds.
One innovation from the consumer goods industry where Schroeder says adaptation for aviation uses could also be possible is the implementation of lattice technology, which entails engineered structures able to dampen vibration or impact. “A lot of the work that we’re doing in those spaces is to really understand how these structures are architected, and how to design these structures is then also being carried over to aerospace, where you can reduce the vibration within a system and you can reduce, in some cases, impact,” he says.
Reducing vibration is a key focus area for the engineering of next-generation electric vertical-takeoff-and-landing aircraft, so this technology could prove useful in their designs. Aircraft used for medical transport also seek to reduce vibration to create a hospital-like environment in the air (see page MRO17), so this could also be advantageous in today’s COVID-19 environment.