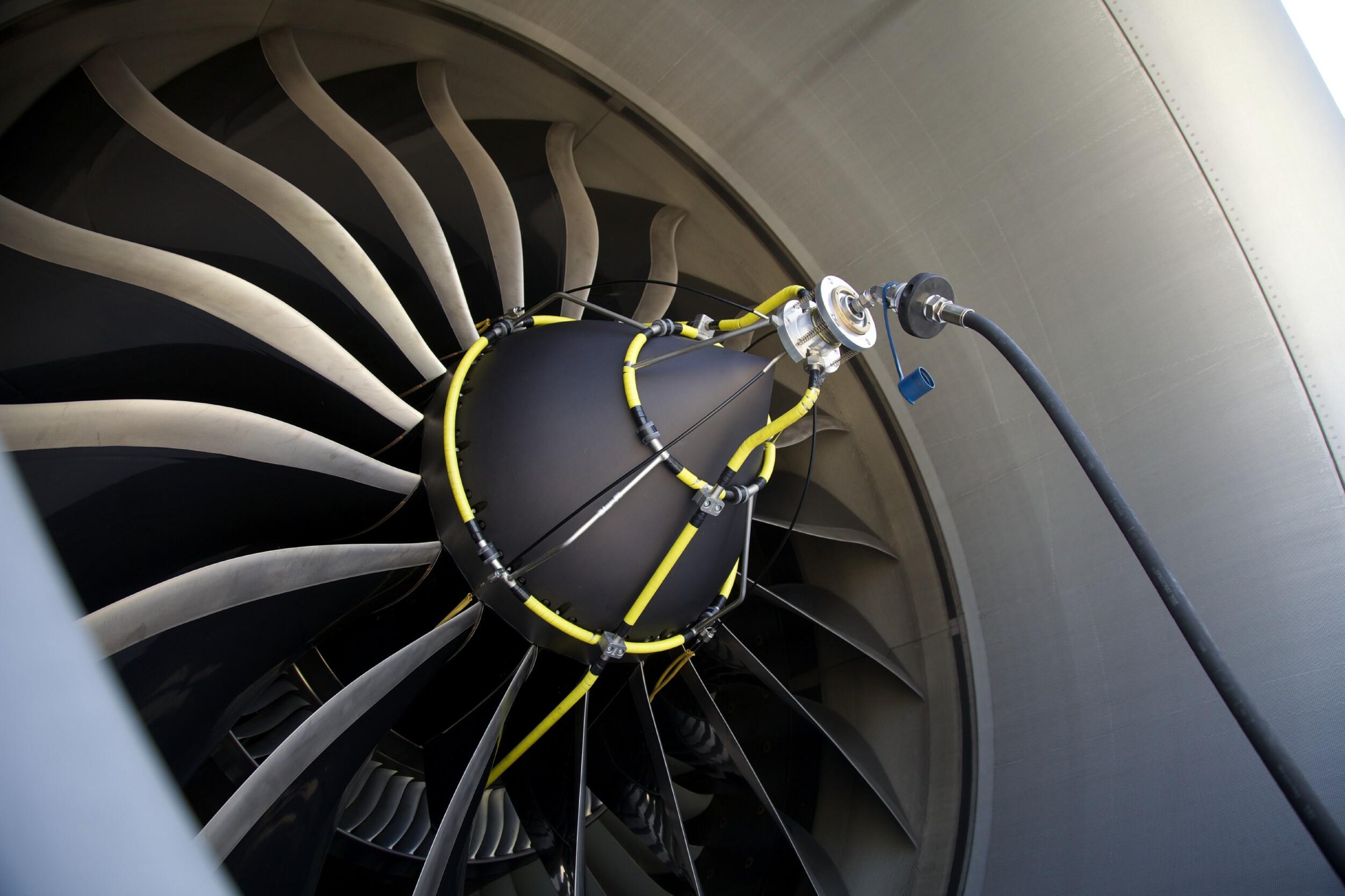
Credit: Sonja Brueggemann/Lufthansa Technik AG
Four engine washes per year strikes the best balance between reducing emissions and costs to operators say researchers from German aerospace center DLR following an analysis of the environmental impact of maintenance on commercial airliners. The study, conducted by the DLR’s Institute of Maintenance...
Subscription Required
This content requires a subscription to one of the Aviation Week Intelligence Network (AWIN) bundles.
Schedule a demo today to find out how you can access this content and similar content related to your area of the global aviation industry.
Already an AWIN subscriber? Login
Did you know? Aviation Week has won top honors multiple times in the Jesse H. Neal National Business Journalism Awards, the business-to-business media equivalent of the Pulitzer Prizes.