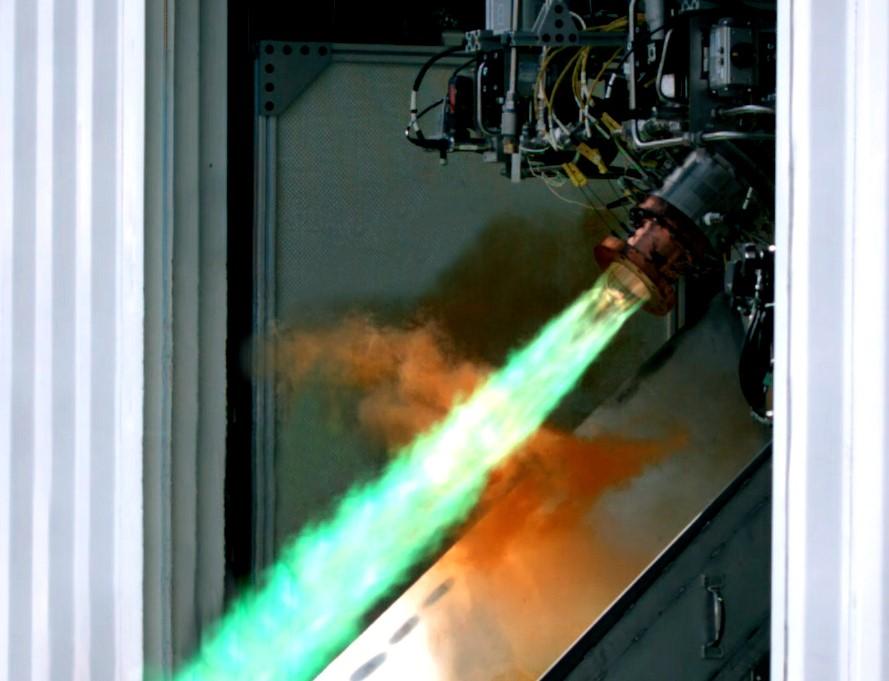
COLORADO SPRINGS—Sierra Space has completed a hot-fire test campaign of a new version of its Vortex hypergolic in-space rocket propulsion family.
The low-cost, additively manufactured VRM1500-H is rated at 1,500 lb. thrust and targeted at spacecraft orbital maneuvering and extraterrestrial landers. Developed at the company’s propulsion test facility near Madison, Wisconsin, the engine is based around a vortex injector concept that produces a swirling propellant flow to cool the combustion chamber. Sierra says both pressure-fed and electric pump-fed variants will be available depending on mission needs.
Test and development of the VRM1500-H began in 2021 and, following design improvements, the rocket was put through a second test campaign beginning in 2022. The engine, which achieved its thrust target in a vacuum test, relies on hypergolic propellants that can be stored long term in space and spontaneously ignite upon mixing, thereby improving reliability.
Another growth version of the Vortex family—the 35,000 lb.-thrust liquid oxygen (LOX)/liquid hydrogen (LH2) engine VR35K-A—is also under development at the 200-acre propulsion Wisconsin test facility. “We’re making our first 35,000-lb. engine there that will scale to 50,000-lb. thrust,” Sierra Space CEO Tom Vice says. “We’re going after a second-stage engine.”
Developed in conjunction with the U.S. Air Force Research Laboratory (AFRL), the VR35K-A is aimed at providing the Defense Department with an alternative upper-stage capability. Compared to existing engines in its class, the VR35K-A will provide both higher thrust and a higher specific impulse for increased capability for a given launch, Sierra says. It also says the use of additive manufacturing will allow the per-engine cost to be lower than existing options.
Sierra Space and AFRL are developing a flight-weight prototype following the completion of a critical design review of the LOX/LH2 upper-stage engine in August 2022. The engine, which passed a preliminary design review in December 2020, incorporates a single-shaft, turbo-pump assembly for mechanically coupled mixture ratio control and a fuel-rich, staged combustion cycle for increased specific impulse.