USAF Chief: New F-35 Engine Development Needed, Even Without Commitment To Buy
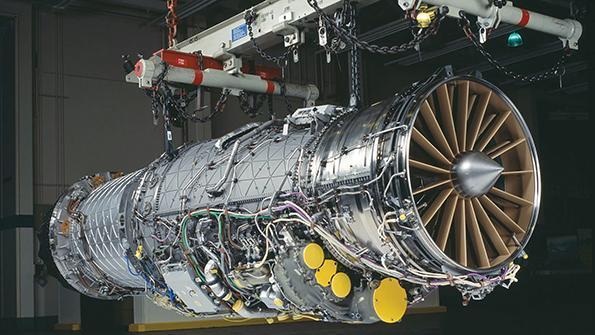
Credit: U.S. Air Force
The continued research and development for a possible F-35 engine replacement is needed, even without a commitment to replace the current F135 powerplant, so the U.S. Air Force can keep the option open and the technology evolving, the top service general said Sept. 8. Chief of Staff Gen. Charles Q...
Subscription Required
This content requires a subscription to one of the Aviation Week Intelligence Network (AWIN) bundles.
Schedule a demo today to find out how you can access this content and similar content related to your area of the global aviation industry.
Already an AWIN subscriber? Login
Did you know? Aviation Week has won top honors multiple times in the Jesse H. Neal National Business Journalism Awards, the business-to-business media equivalent of the Pulitzer Prizes.