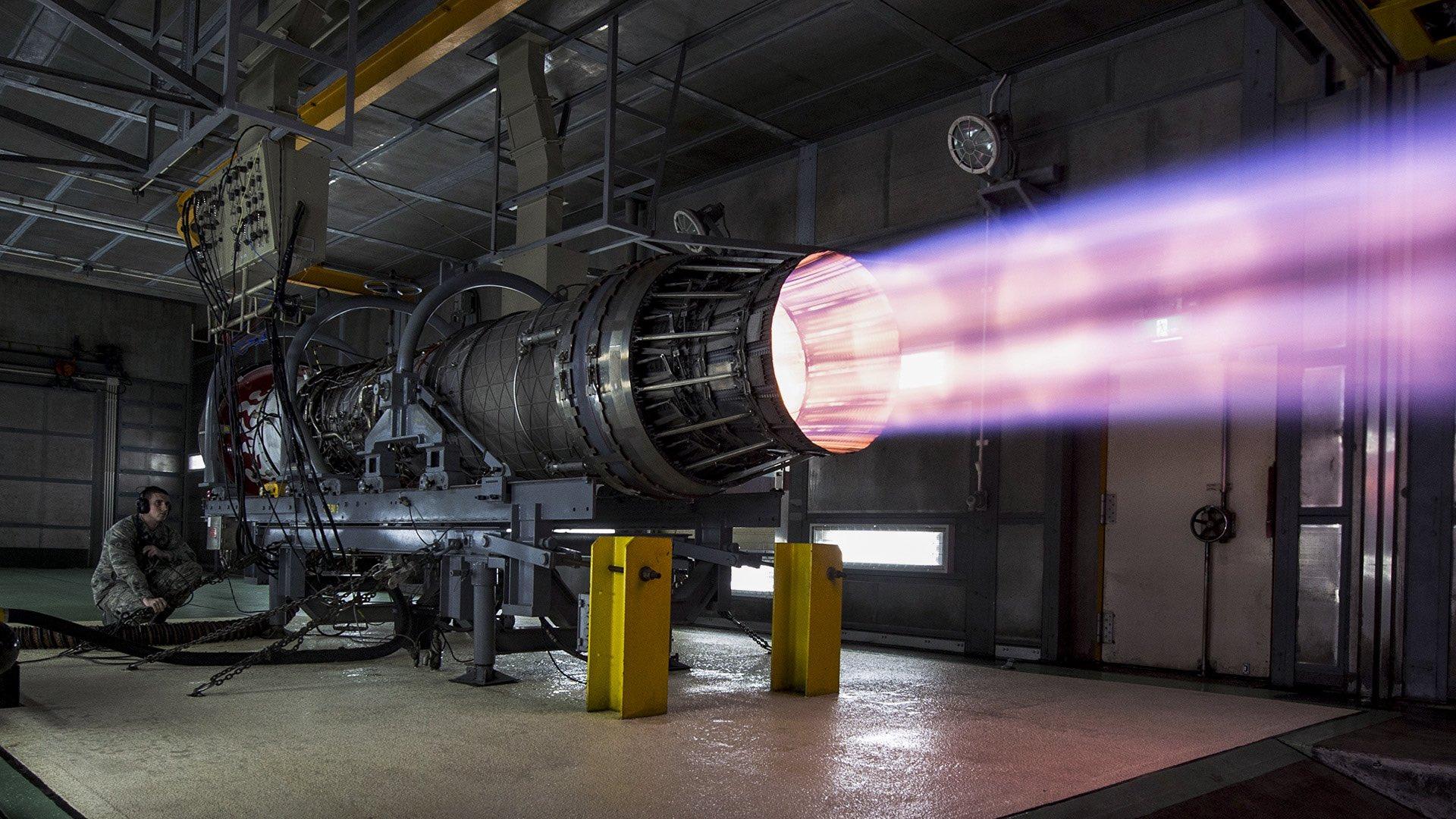
The F100 has previously been studied for high-Mach projects, including DARPA’s Rascal affordable space launch concept.
COLORADO SPRINGS—Hypersonic aircraft developer Hermeus expects to receive Pratt & Whitney’s F100-229 military turbofan for tests later this year as part of plans to integrate the engine into its upscaled Chimera II turbine-based combined cycle (TBCC) propulsion system.
The F100-based TBCC will power the Darkhorse, the next in a series of hypersonic vehicles for military and commercial applications under development by Hermeus. The company’s first aircraft, the Quarterhorse, is a subscale, proof-of-concept demonstrator powered by the initial Chimera I TBCC that is expected to fly late this year or in early 2024.
- F100 will form core of Chimera II
- Darkhorse targeted at Mach 5
Darkhorse is being developed as a hypersonic multimission vehicle for the Defense Department and other customers. The twin-tail delta also is intended as a precursor to a civil hypersonic transport design dubbed the Halcyon.
Hermeus, which announced the selection of the 29,000-lb.-thrust engine as the core for its next TBCC development in December, will use the F100 to accelerate the 45-ft.-long uncrewed aircraft to around Mach 2.8. Around this transition speed a ramjet will take over to accelerate the Darkhorse to a target velocity of Mach 5.
Work to adapt the F100 for its high-speed role follows two recent rounds of tests on the company’s Chimera 1, a General Electric J85-based TBCC, at the Notre Dame Turbomachinery Laboratory (NDTL) in South Bend, Indiana. The demonstrator TBCC incorporates a Hermeus-developed inlet, precooler, ram burner and bypass system—all of which will be scaled up for the Chimera II.
Commenting on the selection of the F100, Mike Smayda, co-founder and chief product officer at Hermeus, says “if you look at the missions that the larger longer-range aircraft are designed for, it’s clear that the entire propulsion system needs to be scaled up. So when we surveyed all the gas turbines that were out there, the F100 is in the right thrust class. It also has proven reliability and millions of flight hours on various platforms. And we weren’t just looking for an engine that was reliable, we were also looking for a great partner, and that’s part of what we found with Pratt.”
Hermeus initially plans to characterize the baseline performance of the F100 before integrating it into the Chimera II. “Then there’s a lot of development for everything around it, including the airframe,” Smayda says. “So we are building the inlet in front of it and the bypass system, the forward door, the aft door and integrate those—the ram burner behind them, and then the exit nozzle. So in general, the propulsion system will involve a far-reaching test campaign to qualify it and get it ready for integration into the Darkhorse.”
To date, Hermeus has tested engines either at its own purpose-developed site at its Georgia base or at the NDTL. But testing the more powerful Chimera II will require significantly larger and more capable facilities. “There are a lot of options for de-risking with sea-level static testing,” Smayda says. “But for testing at that scale, especially at high Mach conditions at higher temperatures and pressures, there are only so many facilities in the world, never mind in the U.S., that can handle this type of engine. So we’re certainly tracking that and figuring out what the details of the test campaign for that engine will look like over the next several years.”
Aside from thrust capability and reliability, Hermeus says it selected the F100 for its robustness and ability to operate from a standing start to Mach 2-plus, all without changes to the basic engine. Smayda adds the company’s requirement “speaks specifically to the engine architecture that we’ve chosen, and to something we can take off the shelf and then build around it.”
By using the F100 to accelerate to ramjet transition speeds, and then cocooning the turbine for high-speed cruise, Hermeus believes the propulsion cycle is less challenging than for a supersonic mission. “If you look at what would be required for a commercial engine that can cruise efficiently between Mach 1 and 2, I think that’s actually a harder propulsion problem even though the top speed of the vehicle is lower,” Smayda says.
“I think the fact that we can use something off the shelf that we know is reliable is a huge program de-risk, and working with Pratt & Whitney specifically on the F100—which is bulletproof—makes a huge difference to the program,” he adds.
Despite the vintage of the original F100 design, the engine has continued to be upgraded with fifth-generation technologies such as thermal coatings and advanced prognostics, says Chris Johnson, vice president for fighter and mobility programs at Pratt & Whitney. “Over 7,000 F100s have been produced and more than 3,700 are still in service today. We’re building on that legacy and that reliability and dependability.”
Johnson adds that although “at the end of the day it’s the Hermeus team that’s going to take this whole enterprise to Mach 5,” the development will benefit from Pratt’s lengthy experience in high-speed propulsion. Going back to the six-decade-old J58 engine developed for the Mach 3-plus Lockheed SR-71, this experience includes Hermeus-like designs that achieved sustained flight above the Mach cutoff point of a normal turbojet by diverting inlet air from the compressor directly into the afterburner.
The F100 previously has been associated with high-Mach projects, having been the proposed turbine engine for DARPA’s Rascal (Responsive Access Small Cargo Affordable Launch) project in the mid-2000s. In this concept the engine was boosted with a water-oxygen mix through a system dubbed MIPCC (Mass Injection Pre-Compressor Cooling). In other areas, Pratt has been exploring high Mach concepts under its Metacomet project, which is focusing on low-cost alternatives to ramjet and scramjet propulsion for high-speed flight.
Comments