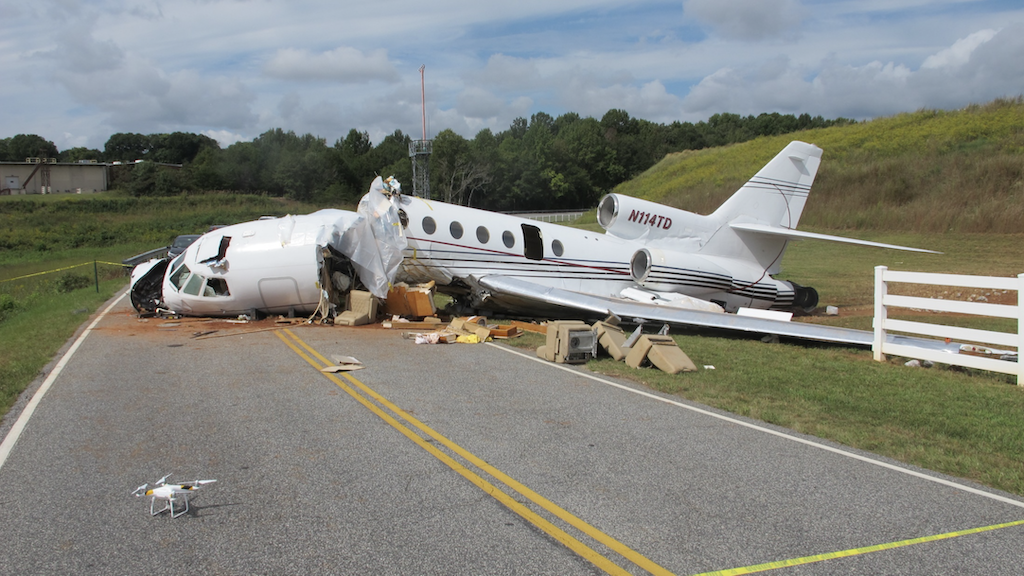
The pilot-in-command (PIC) of a Dassault Falcon 50 that landed at Greenville, South Carolina, in September 2018 was caught completely by surprise when he applied the wheel brakes and nothing happened. The cockpit voice recorder (CVR) recorded him saying “Whoa, whoa, whoa, whoa, whoa! Where are the brakes—where are the brakes?” Seven more times he exclaimed about the lack of brakes before the airplane went off the side of the runway, down a grassy slope and through an airport perimeter fence.
The lack of normal anti-skid brakes should have been no surprise. The pilot sitting in the right seat knew that the normal brake system had malfunctioned before. In addition, there was a yellow “INOP” sticker placed next to the brake selector switch, indicating the normal system was not working.
The copilot did not respond to the PIC’s repeated exclamations for 16 sec. after the PIC first called out the malfunction. Then all he said was “No brakes,” and he took no action to assist the PIC. Both pilots perished from blunt force injuries and the two passengers aboard were seriously injured.
The accident took place at Greenville Downtown Airport (KGMU) in the early afternoon of Sept. 27, 2018. The Falcon 50, registration N114TD, departed St. Pete-Clearwater International Airport (KPIE), Florida, at 1230 Eastern Daylight Time (EDT) and arrived in the Greenville vicinity an hour later.
The airplane was equipped with a Universal Avionics CVR-30 cockpit voice and flight-data recorder, and it captured sounds during the last 31 min. of the flight. The transcript of the pilots’ remarks and ATC radio transmissions are revealing.
During the descent into Greenville, the copilot made a rather cryptic remark about the brakes. He said, “OK, listen—so that will pull left on that regular braking.” The PIC replied, “OK on regular braking so just straighten it out.” It appears that the copilot was aware of braking anomalies on the airplane, but he did not think they were serious.
After listening to the KGMU automatic terminal information service (ATIS), the copilot told the PIC there were broken and overcast layers at the airport and that the wind—200 deg. at 8 kt.—favored Runway 19. The primary runway at KGMU, Runway 1, was 5,393 ft. long, had an ILS approach, a 1.1% upslope, and an engineered material arresting system (EMAS) at the departure end. Runway 19 had only an RNAV (GPS) approach.
The PIC asked the copilot several questions. Passing Colliers VOR (IRQ), about 80 nm south of Greenville, he asked “You know where you’re going?” He then asked, “Does this box have the approaches?” He did not know if the approach displays were loaded in the flight management computer (FMC). He then asked, “We’re not RNAV are we?” No answer could be heard on the CVR. He then asked, “We’re just picking up some of their folks?” referring to the reason for the stop in Greenville. It appears that the left-seat pilot was not familiar with this particular airplane or the day’s charter plan.
After handoff to Greer Approach Control, ATC turned the airplane left to a heading of 320 deg. for a downwind to Runway 19 and descended the crew to 6,000 ft. As the PIC extended the air brakes to slow the airplane, he attempted to verbalize their position and plan. He said, “Alright, we’re on vectors to VOR…zero zero six on the inbound…about a thousand feet on the altitude, field elevation, and one oh nine set…about 6 [?].” The inbound course for the ILS to Runway 1 is 6 deg. and 109.7 is the ILS frequency. The flight was about to be cleared for an RNAV approach to Runway 19 and their navaids were still set up for an ILS to Runway 1.
The RNAV (GPS) RWY 19 at KGMU is a standard “T” configuration. The western initial approach fix (IAF) is “DOODD,” the intermediate fix (IF) is “TIVIL” and the inbound final approach course is 186 deg. When Greer Approach Control cleared the flight to DOODD, and then later to TIVIL, neither fix was in the FMS database. The PIC struggled to enter the fixes while flying the airplane with little or no help from the copilot. After 15 confused transmissions between the pilots and approach control, the controller recognized what was going on and said, “Turn right heading one one zero and expect vectors to final.”
The flight continued inbound with the controller again clearing it for the RNAV approach, the copilot reading back the clearance, and the PIC blindly flying headings and assigned altitudes, setting the flaps, and looking for a hole in the clouds. At one point the PIC said, “What’s the minimum M-D-A out here?” The copilot quickly replied, “Twenty-three hundred.” That altitude is not to be found as a minimum safe altitude (MSA) or minimum descent altitude (MDA) on any approach chart for the airport. It is the final approach fix (FAF) altitude for the ILS to Runway 1.
Seven seconds later, the copilot said, “There you go,” and the PIC replied, “Where is it?” repeating the question three times. Greer Approach stated the airport was at 12 o’clock and 5 mi., and almost immediately the crew called the airport in sight, lowered the landing gear, and switched to the Greenville Tower. After they were cleared to land, they extended landing flaps. and 6 sec. later, an automated voice called out “One thousand.” They did not run a landing checklist but verbalized three green, pumps on, lights on and speeds set.
According to the KGMU Tower controller, the airplane touched down normally at the standard touchdown point on the runway and the center engine thrust reverser deployed. Five seconds after touchdown, the PIC realized he had no brakes.
The Investigation
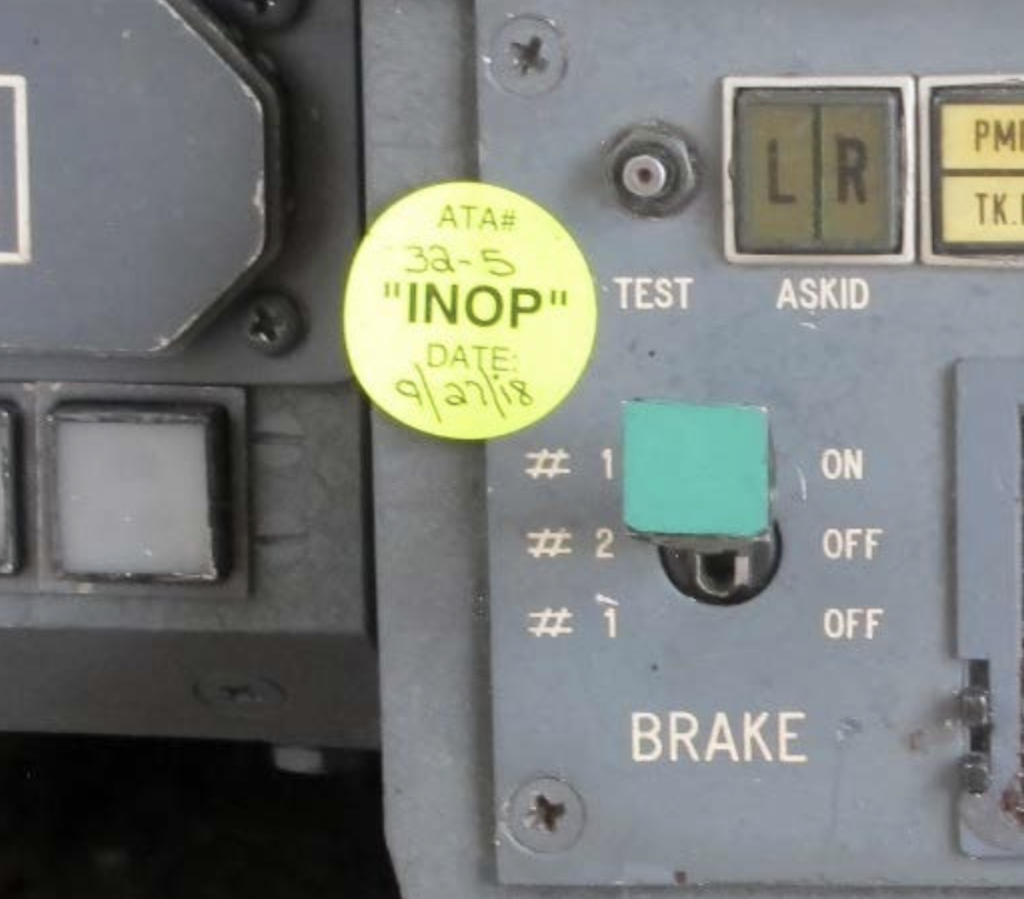
The Dassault Falcon 50 is a midsize, long-range business jet with three engines mounted at its rear. Only the center engine has a thrust reverser. The airplane has two independent hydraulic systems. System 1 provides hydraulic pressure for normal anti-skid braking and system 2 provides hydraulic pressure for emergency braking and the parking brake.
Selection of normal or emergency braking is done via a switch labeled "BRAKE" located on the instrument panel. The "#1-ON" position of the switch selects normal braking with anti-skid, and the "#2-OFF" position selects emergency braking without anti-skid.
The parking brake uses hydraulic system 2 pressure or pressure from a parking brake accumulator to operate the wheel brakes. Pulling the parking brake handle mounted in the center of the glare shield allows a light braking force of about 400 psi to be applied, or a full braking force of 1,560 psi, depending on how far the handle is pulled.
The abnormal procedures section of the airplane flight manual stated that in the event of failure of the normal brake system or inoperative anti-skid, the crew should move the brake switch to the “#2/OFF” position. If both normal and emergency brake systems failed, the parking brake could be used to stop the airplane.
Investigators at the accident site found the airplane was located at the bottom of a 50-ft. embankment and 425 ft. from the runway. Fuel was leaking from the wings, but there was no fire. The landing gears were all fractured, with the nose wheel separated and located about halfway down the embankment. The fuselage was separated just aft of the cockpit. The flaps and slats were deployed, and the airbrakes were extended. Hydraulic, landing gear and brake systems were examined and documented.
The cockpit switches and controls were also documented at the scene. The parking brake was stowed, and the brake switch was in the “#1-ON” position. There was a sticker next to the brake switch indicating "ATA# 32-5 'INOP' DATE: 9/27/18.” That code refers to the anti-skid system, and the date was the date of the accident.
The wreckage was moved to Atlanta Air Recovery in Griffin, Georgia, where aircraft systems investigators inspected brake components that were not visible on scene and removed braking components for further testing. The components were examined and tested at facilities in Akron and Dayton, Ohio.
Before functional testing, the anti-skid system components were examined by a computed tomography (CT) facility to document the internal condition of the components and connections. The CT scan showed that there was a broken solder joint on the left-side inboard transducer and a bent pin connection on the right-side inboard transducer. When further testing was done, investigators found that the left-side inboard wheel speed transducer was not working and the wiring on the right-side outboard transducer was reversed.
A separate maintenance records investigative group examined the airplane’s history in detail and examined the operator’s certification history as well.
Next: Unable To Stop, Part 2, Operator Background Check
Comments
A Falcon 50 is an extremely expensive airplane to maintain and operate.
I think with such a pilot shortage with the airlines, the problem of inadequately trained pilots on the charter side will increase.
The airplane should have been grounded. Accidents like this not only needlessly take lives but bring discredit on the rest of us who fly jets.