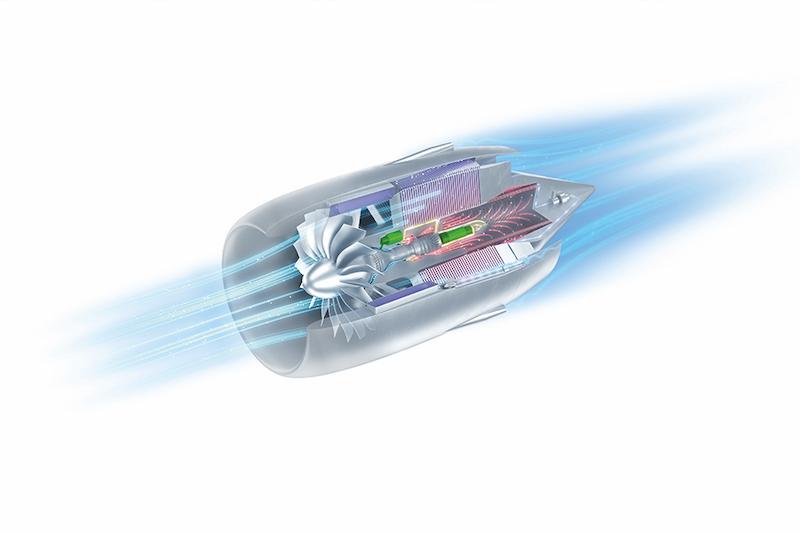
LYON—As part of the EU’s Clean Aviation public-private partnership, MTU Aero Engines is leading a research and technology project aiming at combining the benefits of its water-enhanced engine concept with a hybrid-electric architecture.
The timeline of the program suggests airframers may eventually have the choice between an engine that would be the result of CFM’s RISE research and technology program and one designed from MTU’s Sustainable Water-Injecting Turbofan Comprising Hybrid-Electrics (SWITCH) program. The entry-into-service date for such an aircraft would be in the mid-2030s.
MTU’s main four partners are Airbus, Collins Aerospace, GKN Aerospace and Pratt & Whitney, which may be interested in applications for future geared turbofans (GTF). Together they are pursuing a 25% reduction in CO2 emissions, an 80% cut in nitrogen oxide (NOX) emissions and an unspecified decrease in contrail-inducing emissions. The technologies they will develop may enter into service on a new engine in the next decade.
A water-enhanced turbofan (WET) engine adds a condenser to collect water from the GTF’s exhaust gas and a heat exchanger to vaporize that water into steam. The steam is then injected into the combustor, thus improving fuel efficiency. Under the concept, the temperature profile eliminates most of those hot spots where NOx forms. Most particles are washed out.
However, the large heat exchanger has an unfavorable impact on transient regimes, making the engine less responsive. That is what the hybrid-electric architecture can counteract, says Claus Riegler, MTU’s SVP, technology and engineering for advanced programs.
“WET technology is relevant for the improvement it brings in the cruise phase’s climate impact, while hybrid-electric is for better local air quality at airports,” Riegler says.
For Pratt’s parallel hybrid propulsion system, Collins will supply a 500-kW motor generator on the high-pressure spool and a 1-megawatt motor generator on the low-pressure one. They will be useful for electric taxiing and to give a boost at take-off, as well as in other transient phases, says Graham Webb, Pratt’s chief sustainability officer.
The program’s phase 1, covering the 2023-25 period, is fully funded and will include various assessments. A hybrid-electric GTF engine will be tested on the ground. WET technology will be evaluated at component and sub-system level in a laboratory. Design activity will take place around the combination of the two concepts. In addition, aircraft integration—which will need to be much deeper than for existing aircraft-engine couples—will be studied.
The program is starting from a relatively low technology readiness level (TRL). WET is hoped to be at TRL 2.5-3 by year-end 2022 and reach TRL 4 at the 2025 end of phase 1, Riegler says. If the program follows on with a 2025-30 phase 2, possibly including flight tests, it may hit TRL 6 in 2029-30, he adds.
TRL 6 is the minimum technology basis an OEM usually wants to launch an engine program from.
Meanwhile, the hybrid-electric propulsion system is starting at TRL 3, and Pratt is targeting TRL 5 at the end of phase 1, according to Webb. Simultaneously, integration will be at TRL 4-5, says Karim Mokaddem, head of electrification at Airbus.
Among the challenges are the weight and the size of the engine. MTU’s Riegler expects a 50% weight penalty. While the fan diameter will be unaffected, length will increase to accommodate the heat exchanger, he says. Drag is therefore anticipated to increase and the plan for a 25% improvement factors those drawbacks in.
As for batteries, a two-fold improvement is needed in energy density for the next generation of aircraft, says Mokaddem. Airbus plans to use its experience in batteries for space systems, such as satellites.
“This project will enable us to advance several key technologies on our roadmap to further extend the efficiency of the GTF engine architecture,” says Geoff Hunt, Pratt’s SVP of engineering and technology.
Switch technologies will be compatible with conventional Jet-A1 and sustainable aviation fuels and will be evaluated for use with hydrogen.