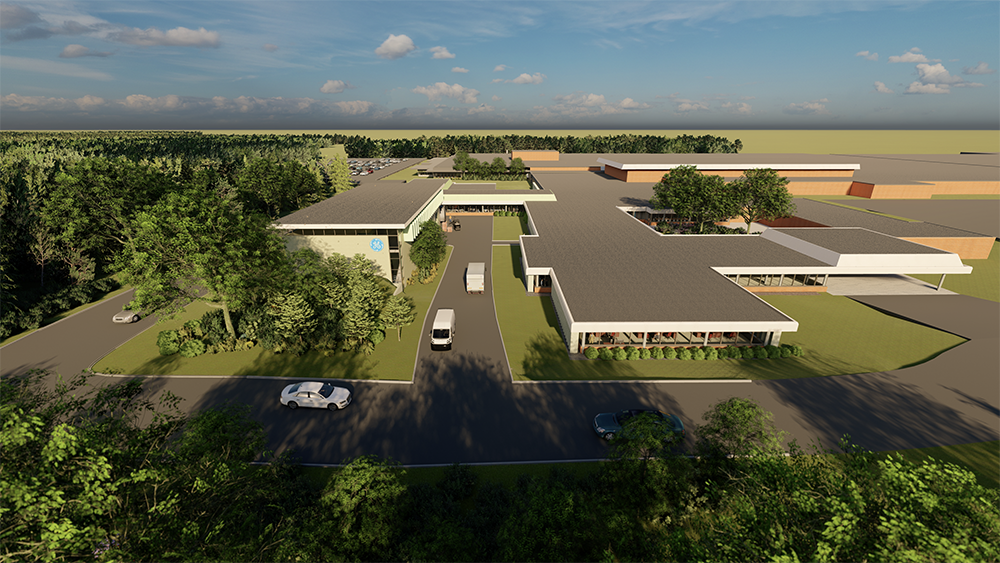
In fall 2023, GE Aerospace will open a new facility that it sees as a key to ensuring its newest engines live up to customer expectations—both in efficiency and ownership costs.
Announced late in 2022 and located near Cincinnati, the Services Technology Acceleration Center, or STAC, will be the de facto research and development lab for engine repairs.
GE has developed repairs for years, of course. So, why a stand-alone facility, and why will it play such a key role going forward? There are several reasons, says Nicole Tibbetts, chief manufacturing engineer-MRO and leader of the company’s time-on-wing group.
One, it gives GE a spot to develop and hone repair processes without bogging down shop floors or taking up technicians’ time.
“It’s really meant to provide a space outside of an active production environment where we can not only incubate [new-technology repairs] but grow and scale them to the point where they can be seamlessly introduced into production both within our network and our partner networks,” Tibbetts said at the recent Aviation Week MRO Americas event.
Counting on repairs in lieu of using new parts has long played an important role in keeping engine maintenance costs down. Repairs are even more prevalent on new-generation engines, which require myriad complex materials and coatings to run hot enough to meet ever-rising customer expectations for operating efficiency.
Those complex design elements have driven demand for more repairs to develop more quickly than for previous generation engines. For example, by the time the Leap-1A family hit its 90-month mark following entry into service, GE and its partners had developed about 1,000 repairs for the variant. By contrast, the CFM56-5B’s repair stockpile did not reach 1,000 until about 270 months after service entry.
And it’s not simply a question of getting the same work done more quickly, Tibbetts says.
“Technology drives the steepness of the slope—how fast you have to do it,” she said. “But the total number will be higher on the Leap engine than it is on the CFM56 engine because we want to ensure that even with that much more complex of an engine, a customer still has the same shop visit cost of ownership as it moves from CFM to Leap.”
Once open, the STAC will not only develop new repairs, but serve as a training center for both GE and third-party mechanics to learn. Such centralization will pay long-term dividends.
“Our vision is to create an up-skilled labor force, where we’re doing things smarter and not harder, and that we have equivalency in terms of how we provide MRO services across the globe, both within GE MRO shops and our partner networks,” Tibbetts said.