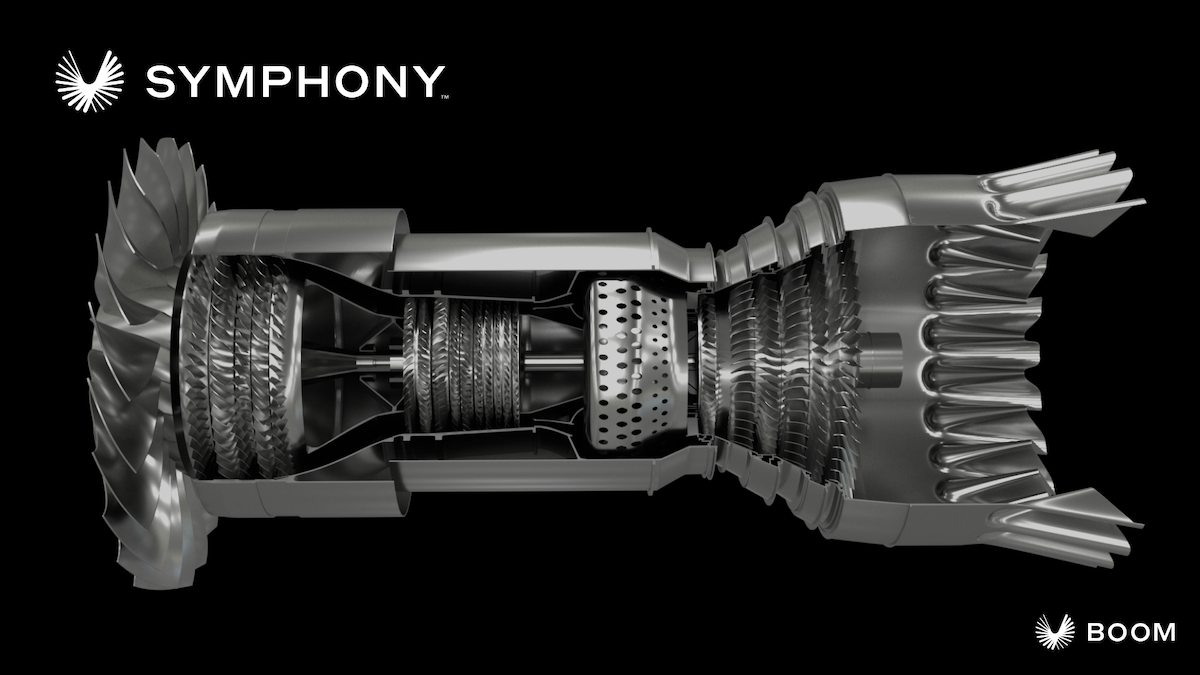
A rendering of Boom's proposed Symphony engine.
COLORADO SPRINGS—Ending months of speculation over its choice of engine, supersonic airliner developer Boom has revealed the formation of an industry team to design, develop and support a purpose-designed propulsion system for its Mach 1.7 Overture transport.
Dubbed the Symphony, the new centerline 35,000 lb.-thrust medium-bypass engine will be designed by Florida Turbine Technologies (FTT), a unit of Kratos Defense and Security Solutions, which is comprised largely of former Pratt & Whitney engineers and veterans of the F119/F135 combat engine programs.
Hinting at a wider potential role ahead for General Electric, Boom says manufacturing will be handled by GE Additive—a 3D-printed parts specialist that will be a unit of the reorganized GE Aerospace from 2023 onward. Maintenance and support will be provided by Phoenix-based Standard Aero, a maintenance, repair and overhaul (MRO) specialist that currently supports fleets of General Electric’s F110 supersonic combat engine and other powerplants.
Boom originally aimed to team with a major engine company with the intent of either co-developing a new powerplant or derive one from an existing core, but these plans came to nothing when talks with Rolls-Royce—which had worked on engine studies with Boom since 2020—ended abruptly in September.
Boom founder and CEO Blake Scholl says lessons learned from the experience already confirmed his growing conviction at the time that the company needed to go in a different direction for its engine.
“That work with Rolls really helped us understand what we want this engine to be,” says Scholl, who acknowledges the resulting change in direction toward a bespoke engine design will push back first flight by a year to 2027. “We’ve used some of our margin here for sure,” he says.
“A lot of people are going to say, ‘isn’t this an aggressive schedule for a new engine?’ And they’re right, it is,” Scholl says. “But we deeply believe the world needs supersonic flight as quickly as possible, and we want to challenge ourselves and our suppliers to do this safely and expeditiously. Is it possible it’s going to take longer than we think it will? Of course. But we like aggressive but achievable targets that challenge us to lean in,” Scholl says.
Despite the delay to the start of test flights and roll-out, which is now expected to slide from 2025 to 2026, Boom still aims to clinch certification in 2029 and achieve entry-into-service by the end of the decade.
The baseline Symphony is configured with a single-stage fan, multi-stage low and high-pressure compressors; a single-stage high-pressure turbine, and multi-stage low pressure turbine. Adaptations for supersonic operation include a Boom-designed axisymmetric supersonic inlet and a variable-geometry translating plug-type exhaust nozzle as previously speculated.
Boom says the engine, which is designed to be 100% compatible with sustainable aviation fuel (SAF), will meet Chapter 14 noise levels. “When compared to derivative approaches, Symphony is expected to deliver a 25% increase in time on wing and significantly lower engine maintenance costs, reducing overall airplane operating costs for airline customers by 10%,” Boom says.
Scholl says the decision to opt for an all-new core is primarily driven by Boom’s plan to adopt a radically different operating model to that used by current subsonic commercial engine-makers, which rely primarily on revenues from aftermarket spares and support. Boom wants the Symphony to remain for longer on the Overture wing with a reduced appetite for spare parts and—as the manufacturer of both the engine and the airframe—instead aims to make more from the initial sale.
Unlike subsonic engine designs in which materials are optimized for short periods at high running temperatures at take-off and climb, and longer cruise periods at lower temperatures, the opposite is true for supersonic engines. “A supersonic mission is different—it needs more cooling air flow. This is how a new core buys its way onto the engine. Working with a derivative core, the cooling air flow is fixed and without redoing the whole core you can’t change that. But it turns out a shockingly small change in cooling results in 25% more time on wing,” Scholl says.
The design therefore incorporates a passively cooled high-pressure turbine, a higher cooling flow rate than on similarly rated subsonic engines and high-temperature resistant turbomachinery core materials technology. “There is a common misconception that technologies like single crystal turbine blades and thermal barrier coatings are only available within the three OEMs. It turns out that’s not true and, in fact, that capability is now basically a commodity. There are a bunch of suppliers that have that capability, and you can partner for it,” Scholl says.
The ability to bring together vertically integrated propulsion system capabilities rather than having to rely on one of the big engine makers is a “paradigm shift for aviation,” which Scholl likens to the recent rise of the new space industry rocket-makers like SpaceX and Blue Origin. “I find it hard to imagine the success story of the Falcon 9 [launch vehicle] had SpaceX not taken that approach. I think what we’re doing here may be a paradigm shift in aviation, but it’s not a paradigm shift in aerospace.”
Together with the design expertise of FTT, Scholl believes the ambitious development, build and test schedule is also possible, citing the rapid prototyping and build capabilities of GE Additive compared to the longer timescales of traditional engine forgings. GE Additive has also “blazed new territory recently on certifications of additively manufactured components,” he adds.
Hinting strongly at the potential wider role that GE might play in the Symphony, Scholl says: “There are multiple discussions about both engine stuff as well as airplane stuff that we’re having with GE, and the one with GE Additive just matured first. So that’s the one we can talk about, but there are other areas we are exploring.”
GE has indicated interest in entering the civil supersonic realm. The engine-maker previously worked in 2018-20 with the now defunct Aerion AS2 Mach 1.4 business jet project on the Affinity engine concept.
Comments