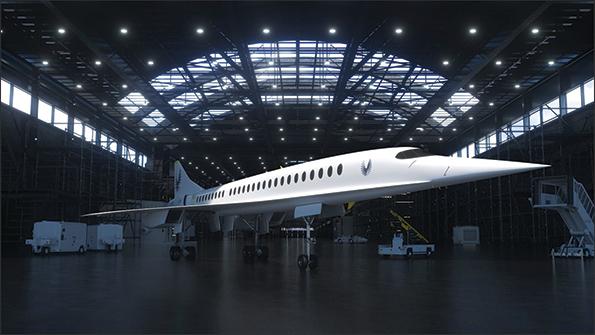
Credit: Boom Supersonic
Ahead of its XB-1 subscale demonstrator flight, targeted for the third quarter of this year, Boom Supersonic has revealed more details to Aviation Week about its planned Overture Superfactory near Greensboro, North Carolina. The Denver-based company in January already confirmed that it expects to...
Subscription Required
This content requires a subscription to one of the Aviation Week Intelligence Network (AWIN) bundles.
Schedule a demo today to find out how you can access this content and similar content related to your area of the global aviation industry.
Already an AWIN subscriber? Login
Did you know? Aviation Week has won top honors multiple times in the Jesse H. Neal National Business Journalism Awards, the business-to-business media equivalent of the Pulitzer Prizes.