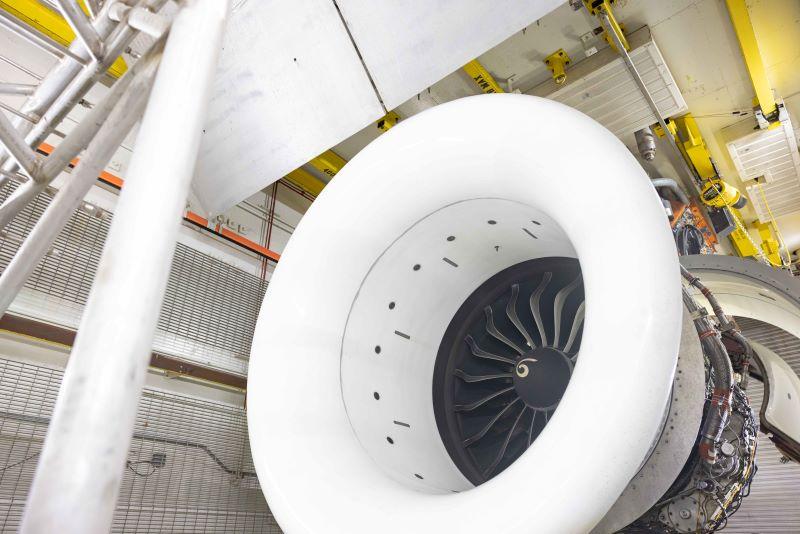
Leap 1 dust ingestion testing
EVENDALE, Ohio—Improvements to the CFM Leap 1 engine designed to enable CFM56-like durability are being validated in a series of dust ingestion tests now getting underway at GE Aerospace’s Evendale, Ohio, facility.
Like nearly all the new generation fuel-efficient turbofans designed to operate at higher turbine temperatures, the Leap 1 has experienced lower time-on-wing time than expected because of hot section durability issues—particularly on aircraft in service in regions with dusty or polluted atmospheric conditions. Now a high-pressure (HP) turbine blade designed to better handle these particulates is in the final confirmation stages.
Validation tests will continue through the remainder of the year and amass a “large” number of cycles. The work is “critical to getting to a time-on-wing and maturity levels of the CFM56. The changes have performed better than we expected,” says Carlos Perez, general manager of Service Engineering for CFM products.
Work is being conducted in Evendale’s Test Cell 40 where the engine, a Leap 1A, is running in front of a specially developed dust ingestion rig. The rig, like the dust itself, has taken GE years and several iterations to perfect, having begun initial ingestion testing for the GE90 in the 2000s. After much trial and error, the company says it is now able to reproduce the premature wear, tear and failure modes found on the baseline Leap 1 first stage HP turbine blades.
The same dust test protocol has also been applied to test and validate improvements to both the GEnx and GE9X engines. In all cases, including the latest tests on the Leap-1, GE has used heat transfer and computational fluid dynamics tools to analyze the revised design and to tie it back to what has been observed in service.
With a consistency similar to talcum powder, the dust has been specially created for the tests by geologists and chemists. It represents particulate sizes and consistency typically found all the way from ground level up to mid-altitudes throughout areas like the Middle East and Indian sub-continent.
“This is the 14th dust test, and we have learned something new on them all,” says Perez. “Our main competition is the CFM56, as our customers expect of the Leap the same high levels of durability and time-on-wing.” The injection rig consists of an array of multiple dispersion pipes which eject the dust into the streamlines of air passing into the inlet. GE says this produces a more even distribution of the particulates into the bypass and core.
Improvements to the HP turbine are mostly in the pattern and passageways of the cooling system and include a revised thermal barrier coating. Following validation tests on the Leap 1A, which powers the Airbus A320neo family, GE and CFM partner Safran plan to conduct clearance tests on the same upgrade in the Leap 1B, which powers Boeing’s 737 MAX. The improved HP turbine is scheduled to be introduced into new production engines as well as retrofits in 2024.
“Testing this technology has helped us unlock what we needed to do to keep this engine on wing as long as a CFM56,” Perez says.
Comments