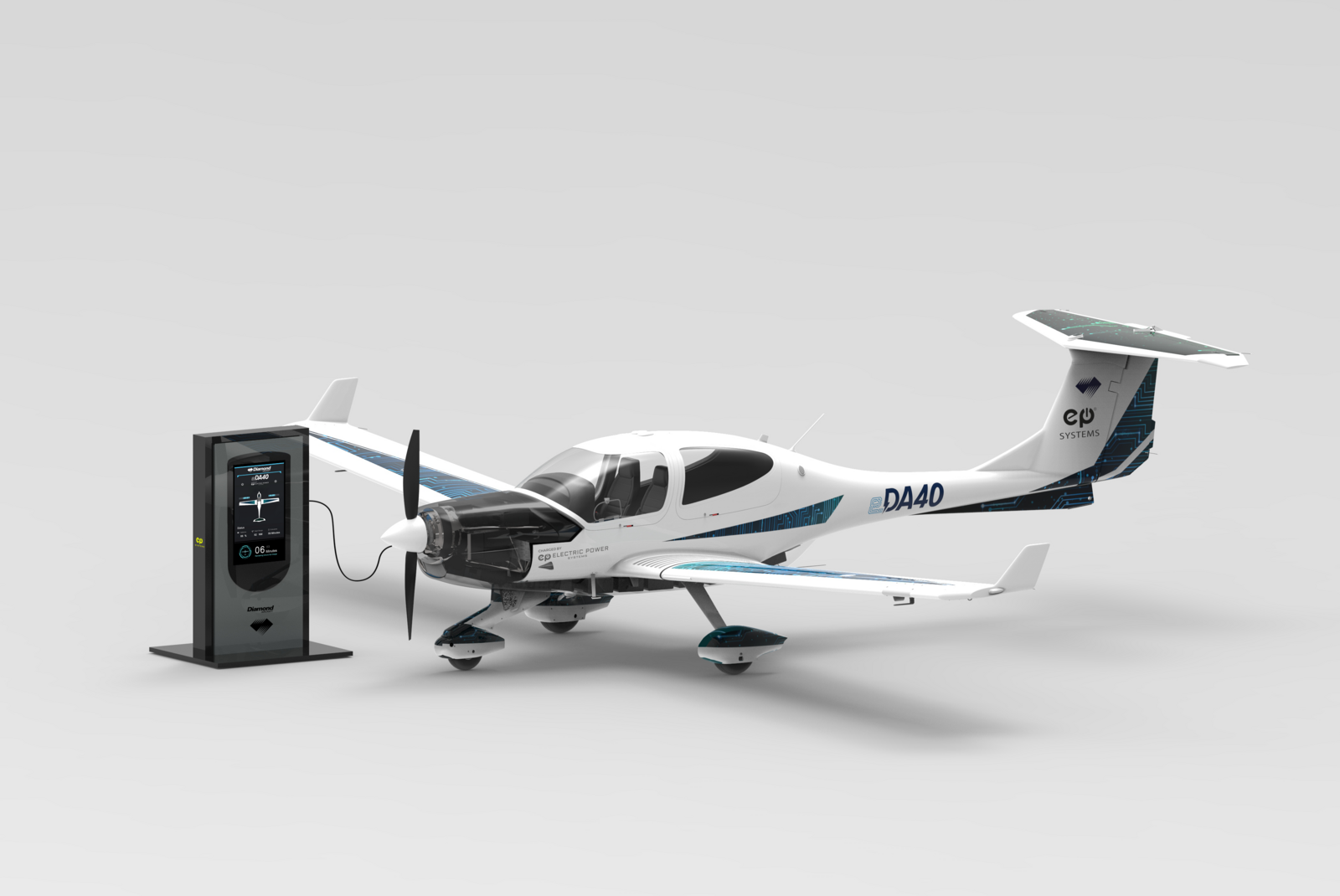
Credit: Diamond Aircraft
Electric Power (EP) Systems plans to ship its first EPiC modular propulsion batteries to electric-aircraft developers this summer for testing in their system-integration laboratories. Delivery of safety-of-flight hardware for use in piloted test flights is to follow. The Logan, Utah-based startup is...
Subscription Required
This content requires a subscription to one of the Aviation Week Intelligence Network (AWIN) bundles.
Schedule a demo today to find out how you can access this content and similar content related to your area of the global aviation industry.
Already an AWIN subscriber? Login
Did you know? Aviation Week has won top honors multiple times in the Jesse H. Neal National Business Journalism Awards, the business-to-business media equivalent of the Pulitzer Prizes.