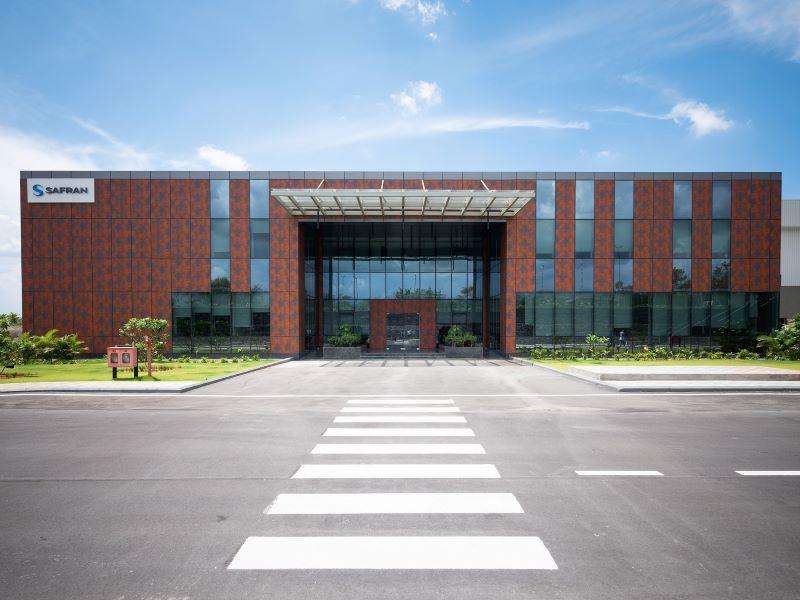
Credit: Safran
Over the 2018-25 period, Safran intends to invest a total $200-250 million in India, essentially around Leap engine production and MRO. The amount, given recently as factories were inaugurated and further plans announced, signals the growing importance of the country in commercial aircraft engine...
Subscription Required
Daily Memo: Safran Places Leap Bets On India is published in Aviation Daily, an Aviation Week Intelligence Network (AWIN) Market Briefing and is included with your AWIN membership.
Already a member of AWIN or subscribe to Aviation Daily through your company? Login with your existing email and password
Not a member? Learn how to access the market intelligence and data you need to stay abreast of what's happening in the air transport community.