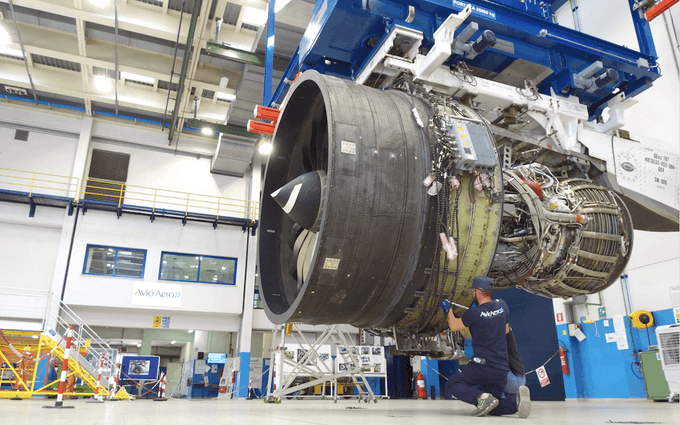
As the airframers go, so goes the aircraft engine industry.
After spending most of the past decade accelerating production to keep pace with unprecedented airliner delivery rates the engine makers have spent the past month in reverse thrust.
But as production lines slow, and in some cases come to a full stop, the grim guessing game about the industry’s post-COVID-19 pandemic future can begin. For every engine company, anchored midway between their own supply chains and Airbus, Boeing and Embraer in particular, all scenarios paint a bleak picture and the potential impact of the virus-triggered crisis is alarming on at least three key levels.
Near term, all must weather the storm and rapidly shrink capacity by 40% or even more to match the new realities of the slower airframe production rates now expected for the next couple of years. Second, having long since focused the core of their business models on the aftermarket, they must adjust to significantly lower revenues from a near term reduction in demand for maintenance, repair and overhaul (MRO) services.
Third, with nearly all their resources dedicated to survival, reduced revenues and spending trimmed, development of new engines and propulsion technology is expected to slow significantly—at least in the near term. However, all the manufacturers know that in the mid-to-longer term the environmental pressures on performance will return and so will the relentless demand for lower emissions and greater innovation. Already committed programs will therefore continue, albeit potentially stretched over longer test and development schedules.
From a volume perspective, GE Aviation and Safran’s CFM joint venture is expected to see the greatest change. Having delivered 1,736 LEAP-1s and 391 CFM56-5/7s in 2019, output from the combined French and U.S. operations will decline significantly in 2020 in lockstep with urgent reductions in production at Airbus and Boeing. CFM, which was previously on track towards a planned annual production rate of more than 2,000 LEAP-1s by the end of 2020, cannot comment on numbers while its parent companies remain in a dark period prior to earnings calls at the end of April, but is expected to slash this target by around half.
GE Aviation, which was already expecting a leaner 2020 before the COVID-19 pandemic because of delays to the GE9X-powered Boeing 777-9 and slow-downs to the GE90-115/GEnx-1 powered 777-200LR/300ER and 787 programs, is eyeing the even more troubling impact of the crisis on its aftermarket business. Although around a quarter of GE Aviation’s revenues come from its military and other businesses, just 30% comes from commercial engine sales. A much larger portion of its revenue—approximately 45%—comes from MRO services.
While some programs, like the CFM56 for the P-8 maritime patrol aircraft as well as military fighter engine efforts, will continue much as before, the company has already taken drastic action to stem losses by furloughing half of its engine manufacturing workers for four weeks. This move, taken in early April, followed an announcement in late March that it was reducing its workforce by 10% (around 2,500 employees), in direct response to the collapse of its MRO workload which the company estimates will be down by around 50% through mid-year at least.
However, given the exodus of around two-thirds of the world’s airline fleets into storage (almost 17,000 aircraft), the short to medium outlook for engine MRO would be described as dire at best. Compounding the issue for many of the OEMs is that the higher value aftermarket engines powering the widebody fleet, particularly the older generation Airbus and Boeing models, now look increasingly unlikely to ever return to service—at least in their existing guise.
For Rolls-Royce, this problem is particularly acute as the UK engine maker focused increasingly on the widebody market over the past decade, widening its exposure to reliance on the support revenue from aftermarket work on older fleets of 747 and 777s as well as older A330s. With full-time premature retirement a possibility, including the previously unthinkable sunsetting of relatively young Trent 900-powered A380s as well as the rapid decline of the RB211-535 powered 757 and Trent 500-powered A340-600 fleets, the company can no longer bank on the expected rebound in deferred maintenance coming out of the crisis.
Rolls has also rushed to mitigate losses by enacting measures aimed at saving at least £750 million ($937 million) in cash this year. These include a 10% salary cut for the global workforce and canceling dividend payments. Further moves are expected as the company adjusts to rate reductions announced by Airbus involving the Trent-powered A330no and A350-900/1000, as well as yet-to-be announced rate cuts for the Trent 1000-powered 787 which will shortly be revealed in detail by Boeing.
Pratt & Whitney, now part of Raytheon Technologies, is similarly impacted across the board with production of the PW1000G geared turbofan reduced for the A220/A320neo families and commercial revenues hit by falling aftermarket revenues for the PW2000/PW4000 and V2500. Measures such as 10% pay cuts through year-end, as well as furloughs, are being introduced while research and development spending is being frozen. Deliveries of military engines, in particular the F135 for the F-35 fighter and PW4000 for the KC-45A tanker remain unaffected. The early retirements of the PW4000, as well as some CF6-powered fleets, is also significantly impacting revenues for German engine maker MTU.