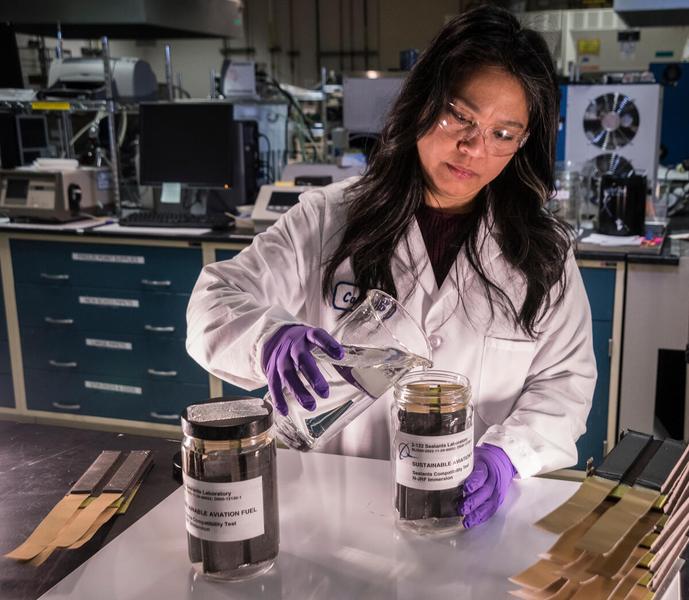
As part of sweeping plans to make its entire product range compatible with 100% sustainable aviation fuel (SAF) by 2030, Boeing is asking suppliers for help defining a SAF type fluid for testing a wide range of components from simple seals to entire engines.
Boeing says the tests will be essential to clearing the use of SAF at 100% because, unlike conventional petroleum-based jet fuel, the synthetic fuel does not always have the aromatics and heteroatomic compounds which help seal connections, valves, pipes and gaskets in today’s aircraft and engines. Testing also involves more than just engines as fuel is also used as a lubricant as well as a fluid for cooling and hydraulics.
To get a head start on the issue, Boeing’s SAF Aircraft Compatibility Integrated Product Team has developed an initial set of jet reference fluids (JRFs) composed of the simple chemical compounds that are found in all SAF. However, because the chemical makeup of SAF can vary depending on the feedstock and refining process, Boeing is asking suppliers to submit requirements for JRFs that apply specifically to their parts—thereby helping to formulate a wider ranging fuel make-up that will cover the needs of every component and system provider.
Boeing says the JRFs will be used both by the company and suppliers to test how SAF interacts with materials differently than conventional jet fuel. Development of the JRFs will also help standardize testing and evaluation as well as prime it for qualification testing once international standards for 100% SAF are set around 2025, the company says.
“Most of the SAF flavors that are out there today are HEFAs (Hydroprocessed Esters and Fatty Acids), and are also 100% paraffinic, so we’ve got some work to do,” Chief Engineer for Boeing Propulsion and Fuels Steve Clark says. “We’re doing some basic compatibility research, and we’re going to run some engineering tests with sealants, seals, pumps, valves, and engines and auxiliary power units. It won’t be for certification credit but for us to understand what the limitations are and where we might need to make changes in the product to accommodate this and field the concept.”
“That’s why the concept of the JRF was born and partly we’re doing that because the ASTM specification for 100% paraffinic fuel is probably a couple years down the road,” Clark says referring to the international standards-setting body which is working to approve SAFs for 100% use by the mid-2020s. “We don’t feel like we can wait those two years or thereabouts to get going. Seven years feels like a lot of time but in terms of deploying fully productionized changes in an airplane that time can be quickly consumed,” he adds.
Sheila Remes, VP of environmental sustainability at Boeing, says the 2030 target was selected “because the aircraft we will be building by then are going to last 20 years—and we hope that SAF scales to 100% by 2050. So, it was really a chance to take a 20-to-25-year lifecycle asset and make sure that those airplanes that come out of our factory at that point in time last through that entire growth period of the energy transition.”
“So, we created this idea of a jet reference fluid to enable us to do compatibility testing now,” Clark says. “We have provided our suppliers with a list of the range of parameters we think they should explore now. What each supplier will elect to pick from the jet reference fluid list will vary depending on the complexity of their product. Someone who’s making an O ring might have a shorter list of properties they would extract from the jet reference fluid list than the engine manufacturer who has to consider a whole bunch of stuff,” he adds.
“We also want to make sure we enable the widest possible future supply of 100% SAF. We could narrowly write a spec around SAF that fits completely with our product as we know it today,” Clark says. “If we did that, it would be a 100% drop in but we would be constraining supply and driving price up and that wouldn’t enable the future we want.”
The recommended fuel “would be largely the 100% HEFA fuels that are available today,” Clark says, adding, “we’re not coming up with unobtainium here for our suppliers. We need to have something that’s going to be available in quantity, particularly for the engine manufacturers because they’re going to be consuming it.”
Details of the requirements were issued to suppliers at Boeing’s “100% SAF Compatibility Supplier Symposium” held in April at the Climate Pledge Arena in Seattle. At the symposium “we were asking our suppliers to tell us what from that property list is important to them and that will help us tailor a jet reference fluid for their needs,” Clark says.
Boeing, which is due to discuss more details of its JRF initiative at a Sustainable Aerospace Together Forum on May 17, has asked suppliers of simpler components to respond “within the next month or so,” Clark says. “We’re giving the engine and APU manufactures a little more time because their needs are more complex, and their testing regimen will be more extensive. This is going to be a collaboration with the suppliers—not necessarily us completely dictating to them what they should do.”
“We are in this pre-ASTM specification phase, and I think it’s a really good thing because we have the opportunity here to really harness the collective knowledge of the supply base on how to do this. We also want the requirements generally to be open source,” Clark adds.
Boeing hopes to complete the compatibility test phase by early 2025. “At that point, we would launch into the change process which would involve formal qualification,” he says. “In that 2025 time frame, we would hope that the ASTM specification will be finalized as well so by then we wouldn’t be qualifying to a jet reference fluid, we would be qualifying to an industry standard.”