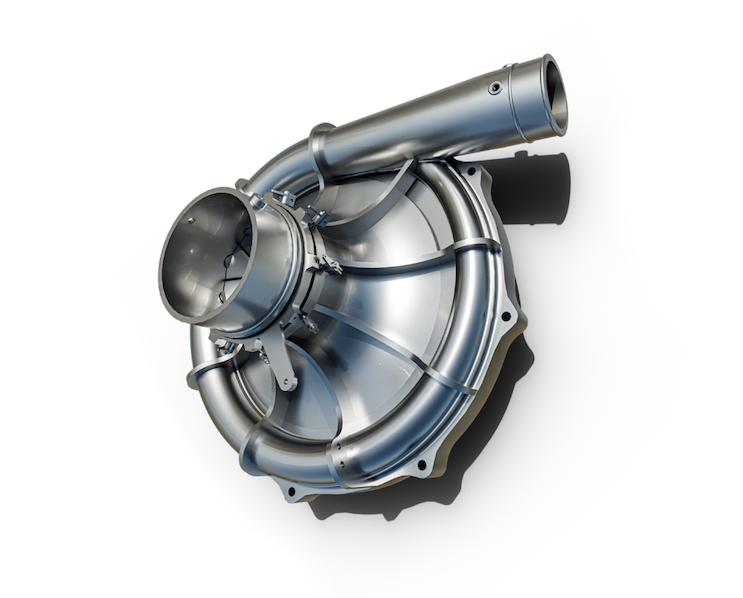
Zero-emissions startup ZeroAvia says initial testing of a purpose-designed compressor for the fuel cell at the heart of the ZA600—its first hydrogen-electric powertrain—shows stable performance over a wide power range.
Describing the radial compressor as a world-first for fuel-cell based aviation propulsion, ZeroAvia says the initial unit will support up to 900-kW power systems, making the design “many times” more powerful than any existing fuel cell compressors.
In addition to its use in the ZA600—a 600-kW powertrain designed for 9 to 19-seat aircraft—a version of the compressor will also be incorporated into the core of the larger ZA2000, a 2-4-megawatt propulsion system in development for larger 40-80 seat aircraft. The ZA600 is targeted at entry-in-service by 2025 with initial application on re-engined Cessna Caravans, while the ZA2000 is targeted at service entry on re-engined ATR 42/72 or Dash 8-300 regional turboprops in 2027.
A key component of most fuel cells, a compressor is used to force air into the fuel cell stack, where it is used as an oxidant to produce a reaction with hydrogen ions and electrons at the fuel cell cathode. The higher the pressure of the reactant gases, the greater the performance of the fuel cell. However, as compressor performance decreases at higher altitudes with reduced air pressure, temperature and density, the unit must be designed to compensate efficiently without added weight or complexity.
For transient power needs, ZeroAvia says the new compressor has also been designed to operate with “zero latency via an innovative flow-management approach.”
“The compressor runs on the power provided by the core electric propulsion system,” ZeroAvia says, “eliminating the additional inverter and electric motor normally required in fuel cell systems.”
“We are driving the compressor with the main propulsion motor—our ZA600 motor for the ZA600 system, for example. The compressor can, however, be driven by any suitable electric motor that meets the rpm and power requirements,” ZeroAvia tells Aviation Week.
The ZA600 uses pressurized, 350-bar (5,000-psi) gaseous hydrogen storage and low-temperature proton-exchange membrane (PEM) fuel cells supplied by Sweden’s PowerCell. The larger ZA2000, which is a liquid-cooled, high-speed machine that runs at 20,000 rpm and drives the propeller via a gearbox, will use liquid hydrogen and high-temperature PEM fuel cells developed internally by ZeroAvia.
The company is currently finalizing the design for certification of the ZA600 powertrain and its installation on the Caravan, having completed tests of the prototype propulsion system this July on a Dorner 228 testbed. The demonstrator powertrain tested included a fuel cell system and battery pack in the fuselage powering an electric motor in the nacelle.