Opinion: Engineered Materials Will Drive AAM and Aircraft Production
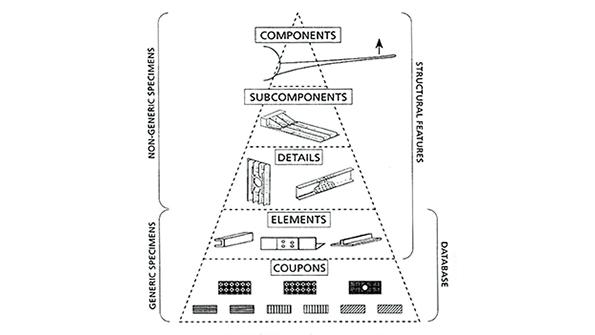
Credit: FAA
Recently, Boeing CEO David Calhoun stated that the OEM’s future jetliner would be driven largely by the production system and not necessarily by new engine technology, a fundamental departure from previous product iterations. The same production strategy underpins the business model for advanced air...
Subscription Required
This content requires a subscription to one of the Aviation Week Intelligence Network (AWIN) bundles.
Schedule a demo today to find out how you can access this content and similar content related to your area of the global aviation industry.
Already an AWIN subscriber? Login
Did you know? Aviation Week has won top honors multiple times in the Jesse H. Neal National Business Journalism Awards, the business-to-business media equivalent of the Pulitzer Prizes.