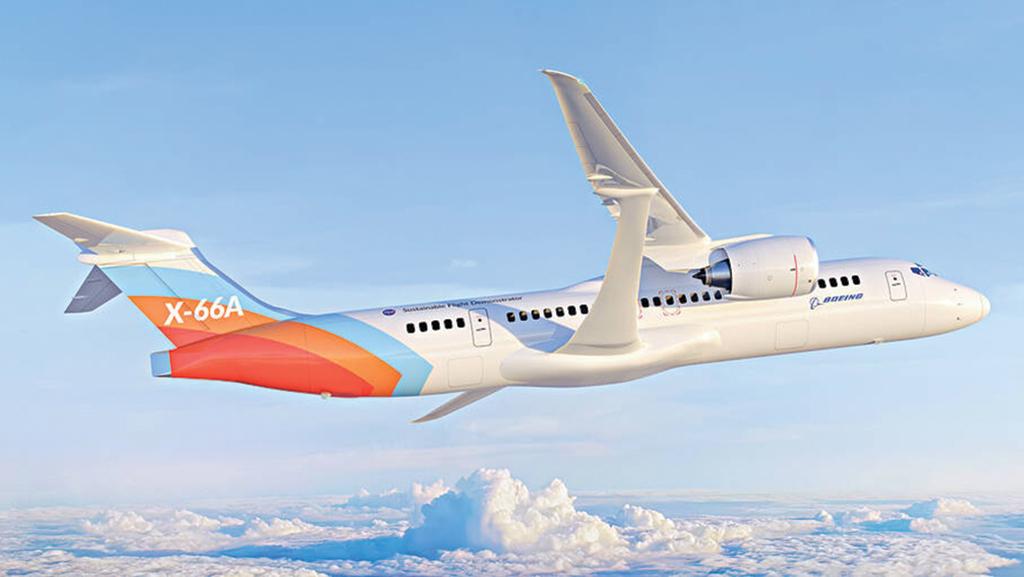
Are there technologies available today that could produce a better airliner? Yes. Are there technologies mature and ready today that could enable double the traditional generational improvement in aircraft fuel efficiency, to 30% from 15%, to help accelerate the decarbonization of aviation? No.
Given a choice, would airlines trade efficiency for maturity at entry into service? Probably.
That is the mathematics Airbus and Boeing are working through as they look ahead to launching their first clean-sheet single-aisle airliners in decades. When to launch, what technologies to use and what performance will the airlines expect?
A key variable in the equation is technology maturity. Airlines expect a trouble-free entry into service, but pushing the envelope on technology makes that harder to achieve. The CFM Leap and Pratt & Whitney PW1000G underwent the most exhaustive development and certification testing efforts ever for new commercial turbofans—26,500 cycles for the PW1000G family—yet both engines experienced significant teething problems, largely due to new technologies.
As aircraft and engine manufacturers develop an array of technologies that could dramatically improve the efficiency and reduce the emissions of next-generation airliners—from open-rotor engines and low-drag wings to electrified systems and high-rate composites—the question uppermost in their minds is: When will they be mature enough to incorporate into a product?
The measure of maturity that aerospace traditionally uses is technology readiness level (TRL). But experience with development and introduction of the latest generation of commercial engines—and with complex military programs such as the Lockheed Martin F-35 Joint Strike Fighter—raises the question of whether TRL is up to the task as the industry pushes the envelope.
TRL was pioneered by NASA in 1974, but its nine levels were not formally defined until 1989. Since then, TRL 6—prototype demonstration in a relevant environment—has come to be viewed as the gate to product development. But aerospace development is not about technologies in isolation, and many advances have been tripped up during their integration into a system.
In the 1990s, recognizing a gap between technology readiness assessments and successful development programs, the U.S. Defense Department augmented TRL with integration readiness level (IRL) and manufacturing readiness level (MRL). In 2006, the system readiness level (SRL) was defined to provide a more holistic integration between TRL and IRL.
“Industry experience has been that technology readiness TRL 6, while necessary, is not fully sufficient to assess the potential for application onto a platform,” says a 2021 report by a NASA/Boeing team. “The most successful seamless technology transitions rely on consideration of TRL, MRL, IRL and SRL in both technology development and vehicle design.”
Research technologists face a conundrum, the report says. They must initiate technology research without knowing the requirements of a specific application, while shorter product development cycles leave them with insufficient time to meet all the additional design requirements levied after TRL 6 when the application is known.
The report examines three technologies that reached TRL 6 but did not make it onto a new aircraft: drag-reducing riblets, bugphobic coatings and active flow control. The team concludes they failed to transition due to challenges in the operational environment.
“Missing from the TRL assessment were significant in-service operational environment ‘-ilities’ such as maintainability and reliability,” the report says. Other “-ilities” include the wearability of riblets, operability of bug-phobic coatings and certifiability of active flow control.
The team proposed a total technology readiness level (TTRL) model that brings together TRL, MRL, IRL and the “-ilities” into a more robust tool set. “The TTRL process can accelerate technology readiness and enable an earlier pragmatic understanding of feasibility, practicality and applicability,” the report says.
“Total technology readiness serves as a holistic model that can encompass all elements to more sufficiently bridge a new technology into an application,” the team says, adding it is critical that technology developers and vehicle designers are together responsible for the early identification of significant “-ilities” that may become showstoppers in a later business decision on whether a technology can transition or not.
What does this mean for the next Airbus or Boeing? It means flying an open-fan engine or long-span wing at full scale by 2028 may tick the TRL 6 box—prototype demonstration in a relevant environment—but that alone may not be enough to win it a place on the next-generation single-aisle.
Add sustainability to the list of “-ilities” that must be considered, and how hard the airlines are pushing—and how long they are willing to wait—for significant emission reductions becomes part of the technology readiness equation.
Comments