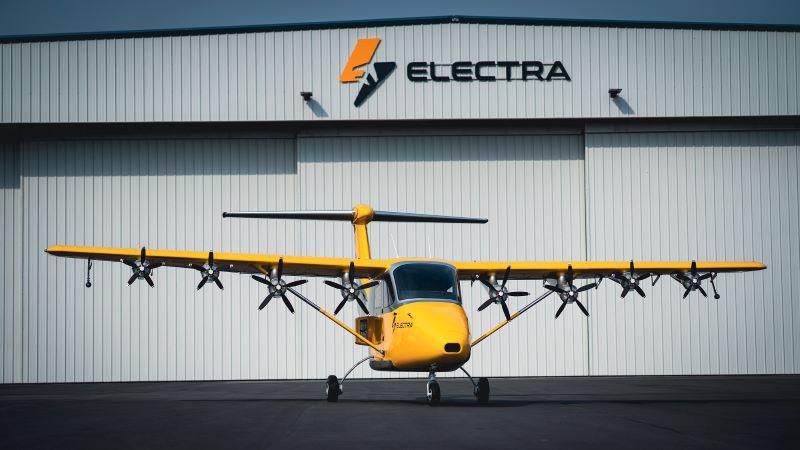
Electra technology demonstrator
Electra.aero has unveiled the technology demonstrator for its hybrid-electric ultra-short-takeoff-and-landing aircraft.
The piloted two-seat demonstrator is set to fly this year to test the blown lift aerodynamics and short-field performance of its design.
Based in Manassas, Virginia, Electra is developing an aircraft that can take off from a soccer-field-sized area with a 150-ft. ground roll and carry nine passengers or 2,500 lb. of cargo up to 500 mi. The TD2 demonstrator will flight-test Electra’s blown lift technology, which uses distributed electric propulsion.
The demonstrator has a modified Cessna 172 wing, with eight electric-powered propellers mounted under the leading edge so that their slipstream flows back over the wing and blows large, double-slotted flaps and drooped ailerons to increase lift at low airspeed. The goal is to demonstrate a 150-ft. ground roll.
Electra has completed a series of ground tests with the wing attached to a Cessna 172 fuselage and mounted on a truck that was driven along the Manassas Regional Airport runway to simulate takeoff and landing. This testbed was equipped to measure forces generated by the blown wing.
The test wing has now been attached to the demonstrator’s purpose-designed composite airframe, which has a turbogenerator in the nose, battery packs under the floor, two-crew cockpit, tricycle gear and a large T-tail to counteract the pitching moment generated by blowing the wing.
Flight tests of the demonstrator will generate data to inform the design of Electra’s production electric short-takeoff-and-landing (eSTOL) aircraft. The first prototype of the nine-passenger aircraft is planned to fly in 2025, and the startup is targeting certification in 2028 under FAA Part 23 regulations as a multi-engine airplane.
Electra was founded by John Langford, former CEO of Aurora Flight Sciences—now a Boeing subsidiary. Aurora has considerable experience with electric aircraft, including flying the Pegasus Personal Air Vehicle, an electric vertical-takeoff-and-landing (eVTOL) technology demonstrator, in 2019.
“We just could not close the business case for eVTOL using near-term technologies,” says Electra Vice President and General Manager J.P. Stewart. “Electra was founded to build electric aircraft that make sense.”
Short-Takeoff-and-Landing
Electra is targeting the market for trips of 50-500 mi., where people now choose to drive, with an eSTOL capability that enables the aircraft to get close to where people are and where they want to go.
Vertical-takeoff-and-landing (VTOL) aircraft design makes significant compromises for that capability, Stewart says, citing the team’s previous experience developing eVTOL vehicles.
Vertical flight capability requires additional power that reduces payload and range. The poor energy density of batteries makes this tougher. “Relax the VTOL requirement, and you see dramatic performance and cost improvements,” he says.
Chris Courtin, chief engineer for the technology demonstrator, compared the performance of eVTOL and eSTOL while at the Massachusetts Institute of Technology (MIT) studying under professors Mark Drela and John Hansman, both senior technical advisors to Electra. For equivalent gross-weight aircraft, he concluded a hybrid-electric eSTOL has more than twice the payload and 10 times the range of a battery-only eVTOL.
“We stepped back and questioned our initial assumptions. Do you need true VTOL capability to get into small spaces?” Stewart asks. “Vertiports have space for STOL.”
With the FAA’s required separation, putting together three 50 x 50 ft. landing pads requires at least 450 x 150 ft. before even considering the approach and departure clearway. Electra’s eSTOL aircraft is designed to take off from a 150 ft. ground roll with two motors failed, he says.
But how do you achieve a 150-ft. ground roll with a 9,000-lb. aircraft? The answer is more lift. In the 1950s, when Helio produced the ultra-STOL Courier, that was achieved using a big wing, slats, flaps and powerful engine. In 2023, the solution is to use distributed electric propulsion (DEP) to blow the wing and achieve a high lift coefficient of 6-7, compared to 1-2 for a conventional wing.
Blown Lift
Blown lift was used in the 1960s on the Breguet 941 STOL transport, but the aircraft was complex—its four turboprop engines mechanically interconnected to ensure continued safe operation in the event of a failure. The 941 could take off in 600 ft. at 48,000 lb., but never saw production.
Electra has revisited the concept using DEP to both increase the effectiveness of blown lift and simplify the system by using many small, electric-powered propellers—eliminating the gearboxes and cross-shafts.
In blown lift, the propeller slipstream interacts with the wing to increase lift. Blowing increases airspeed over the wing, but the biggest lift augmentation comes from the large, trailing-edge flaps turning the flow. Blowing adds energy to the wake coming off the trailing edge and creates a jet flap that continues downward, like a flap extension. Essentially, the airflow sees a bigger wing.
This effect strengthens as speed decreases and diminishes as speed increases and flaps are raised. This allows for a normal-sized wing in cruise to reduce drag and helps dampen the effects of turbulence.
On the technology demonstrator, the four inboard propellers blow the double-slotted Fowler flaps that generate the majority of the lift augmentation. The four outboard propellers blow the drooped ailerons, which also open a slot as they extend. A combination of aileron deflection and propeller-speed modulation provides lift, roll and yaw control.
The wing is based on a Cessna 172 wingbox and has a new leading edge designed to work with blown lift. The donor 172 wing has a break at about two-thirds span and is tapered outboard, so the outer pairs of propellers are smaller to avoid overblowing the outer sections. All eight motors are the same—and, on the production eSTOL, all eight propellers will be the same.
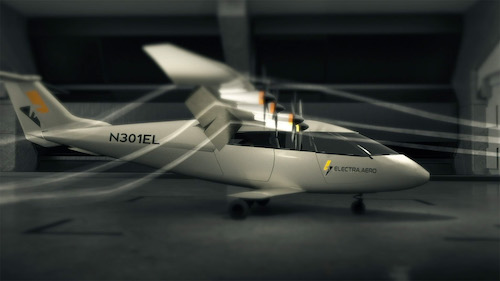
The inboard flaps have low-bandwidth actuators used for drag control on takeoff versus landing. The ailerons will have high-bandwidth actuators “and a lot of control authority in roll,” Stewart says.
Compared with the Breguet 941’s four large propellers, the eSTOL’s eight small propellers increase the blowing density and reduce flow blockage caused by the nacelles, which protects the suction peak on the wing’s leading edge and mitigates the effect of a motor failure, Stewart notes.
A key objective of Electra’s ground and flight tests is to determine whether the tail is sufficiently powerful. Blowing the wing and producing a jet flap moves the center of pressure aft and causes a nose-down pitching moment. To maintain stability, the demonstrator’s horizontal tail includes a high-lift slot.
“We didn’t want to add unnecessary complexity,” Stewart says. “A major objective of the technology demonstrator is to prove that the high-lift tail works.” As the result of its wing and tail design, the aircraft is exceptionally difficult to stall, he adds.
The demonstrator’s 150-kW-series, hybrid-electric propulsion system is built around a turbine engine based on a helicopter auxiliary power unit and driving an existing gearbox and generator, mounted like a 172 in the nose. “We could have used an internal combustion engine or fuel cell, but turbine power density is good and it’s reliable, robust, mechanically simple and well understood,” he says.
The turbine is sized for cruise. The liquid-cooled battery packs handle peak power and provide redundancy. The production eSTOL will have a 600-kW hybrid powertrain with a 50-kWh battery system. “We are gentle on the batteries. Takeoff and climb use 10% state of charge, and we have the whole cruise to recharge at a very low C rate,” Stewart says, noting that operating the battery between 80% and 70% charge will greatly extend cycle life.
The operator can choose to increase the hybridization factor in flight, including performing a battery-only takeoff. Electra is building in the hooks to move to a hydrogen fuel cell for prime power. Following Electra’s acquisition of rival startup Airflow, fuel cell producer Plug Power is an investor.
“Given the austere environments our aircraft will operate in, not requiring special or new infrastructure at entry into service is fundamental, and a turbine can work with a wide range of widely available fuels,” Stewart says. “But we believe in the long-term prospects of new propulsion systems.”
Electra is working with several partners on the hybrid system for the production eSTOL aircraft. Some have chosen a clean-sheet, purpose-designed turbogenerator, with high performance and low fuel burn but higher development risk. Others have mated an off-the-shelf engine with gearbox to an existing generator. “It’s a performance/cost/development risk trade,” he says.
With initial seed funding, Electra flew a one-third-scale eSTOL model with MIT in 2020, and in 2022 developed a 150-kW hybrid propulsion system for the technology demonstrator with its subsidiary in Switzerland. The recent full-scale wing aerodynamic truck tests have been funded by the U.S. Air Force’s AFWERX innovation unit under its Agility Prime program.
Building and flying the technology demonstrator is being funded by Electra’s 2022 Series A financing round, which included investment by Lockheed Martin Ventures. The full-scale prototype will be funded by Electra’s ongoing Series B round, which includes an AFWERX Strategic Funding Increase (STRATFI) award that secures up to $85 million of combined government funding and matching private investment.
The objective of the STRATFI award is to fly the prototype in operationally relevant ways, Stewart says, such as logistics resupply and medical evacuation. Following this initial non-conforming prototype, Electra plans to build a certification test aircraft, aiming for entry into service in 2028—a slip of two years from the startup’s original target.
Electra says it holds letters of intent for more than 1,200 aircraft from 32 customers, 70% of which are existing aircraft operators. “We are not our own operator,” Stewart says, a reference to the eVTOL market leaders that plan to operate as well as manufacture their air taxis.
The pre-orders cover the first four years of planned production and would get Electra to around 400 aircraft a year by 2030. “We only need approximately 400 aircraft in total to break even on our business case,” he adds, noting that developing a Part 23 aircraft does not carry the $1 billion-plus price tag of developing and certifying an eVTOL aircraft.