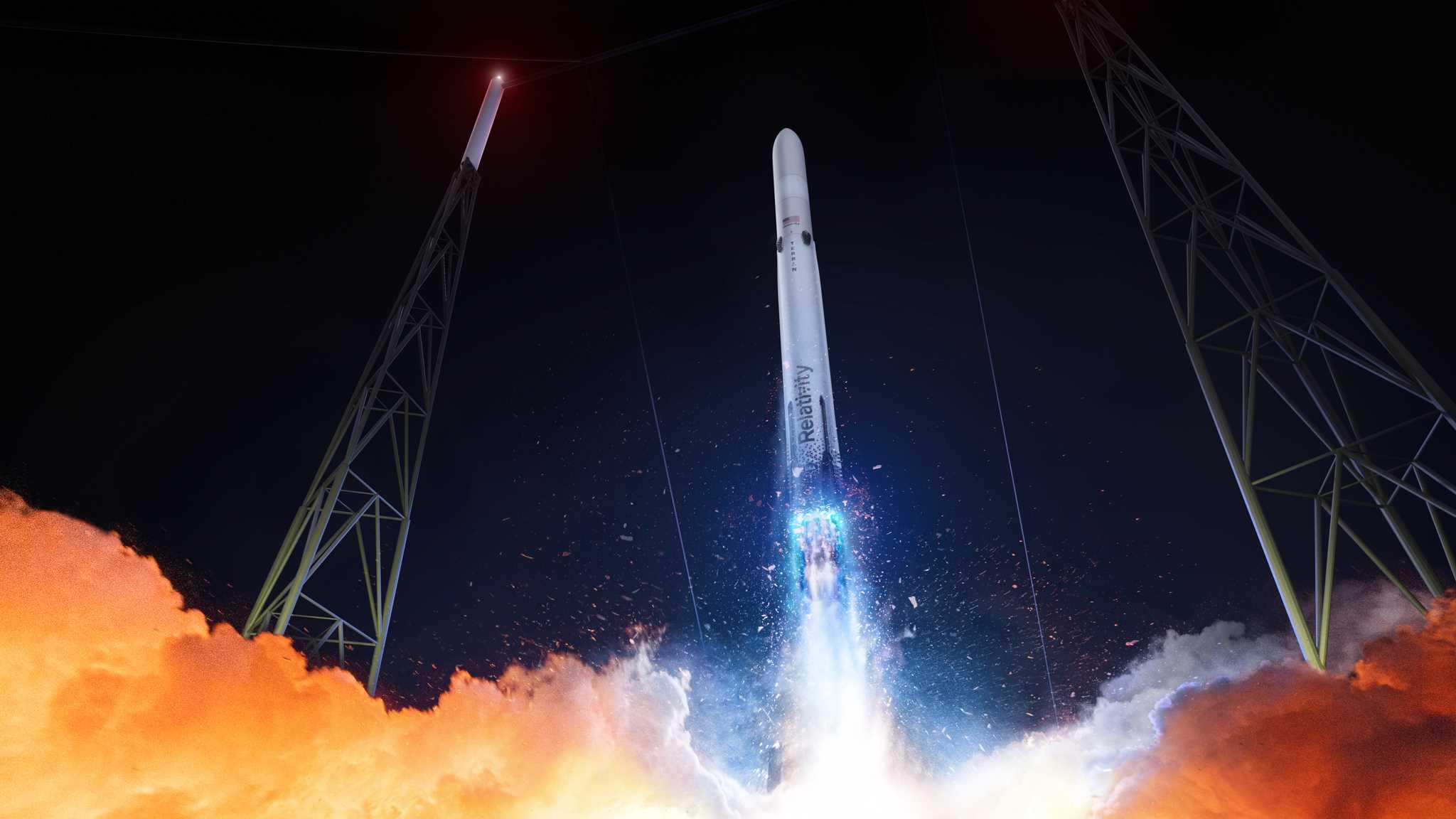
COLORADO SPRINGS—California-based startup Relativity Space is focusing on a rapid test series for its liquid oxygen/methane (LOx/CH4) Aeon R rocket engine following the company’s decision to pivot directly to development of the larger Terran R heavy-lift launch vehicle.
“The game plan is to do full engine testing this year,” says Tim Ellis, founder and CEO of Relativity. “Propulsion is usually the long pole for most launch programs just because rocket engines are still very hard to develop.”
Although Relativity originally planned to develop the Terran 1 for commercial launches of payloads up to 1,250 kg (2,760 lb.) to low Earth orbit (LEO) before moving to growth versions, the company is refocusing immediately on the more capable Terran R because of “overwhelming customer demand,” says Ellis, who spoke to Aerospace DAILY at the recent Space Symposium here. “We’ve sold $1.65 billion in launch service agreement contracts, and we have a customer pipeline with several billion dollars of additional agreements, some of which were in pretty rapid negotiations right now,” he adds.
“There is just a very clear need for that in the medium to heavy-lift launch market and other than SpaceX, which has been wildly successful with Falcon 9 and the soon-to-debut Starship, there’s really not another company that’s demonstrated the ability to have reusable rockets and disruptive technology,” he notes. Terran R will be designed for first-stage reusability, with the capability of launching 23,500 kg to LEO or 5,500 kg to a geosynchronous transfer orbit, both with downrange landing, or up to a maximum payload of 33,500 kg to LEO in expendable configuration.
Amid delays and hold ups in other launch vehicle programs and the loss of Russian capacity in the wake of the Ukraine invasion, the medium/heavy launch market is becoming tighter, Ellis says. “It’s not very clear yet. Who is going to take that trophy of the next great launch company? While certainly those are established companies that have a big track record, I think we have a really good shot at it just because of the high momentum that we have.”
The first stage of the 270-ft.-tall Terran R rocket will be powered by 13 Aeon R engines, each of which will generate up to 258,000 lb. sea level thrust. The upper stage will be powered by a single LOx/CH4 Aeon Vac engine with 279,000 lb. vacuum thrust. “Over the next couple of months, we will be working to complete our own vertical engine test stand which actually has two side-by-side engine bays,” Ellis says. The site is due to be completed this fall at the company’s facility at NASA’s Stennis Space Center in Mississippi.
The first-stage engine closely resembles the smaller Aeon version designed for the Terran 1 vehicle, which launched on its first–and only–flight on March 22 from Launch Complex 16 at Cape Canaveral. But the vehicle failed to reach orbit after a problem with the second-stage engine. “We’re still working with the FAA and external partners to put out a formal report, but there’s really two fundamental things,” Ellis says. “When we commanded one of the engine valves to open it happened more slowly than expected, so that affected some of the timing of the propellant getting into the gas generator and main thrust chamber assembly. The igniters fired successfully, but then the propellant timing was off.”
Another issue occurred with the oxygen system. “From the data it looks like there was a vapor bubble in the turbo pump inlet. Turbo pumps are designed to run on liquid propellants, so if they ingest any gas they won’t function properly. That’s what caused the lack of ignition,” Ellis says. “But the second stage still coasted up to 134 km, so we are the first methane-fueled rocket outside of China to reach space.”
“We’ve tested the Aeon R thrust chamber assembly at full power several times now and we’ve also tested the gas generator at full power,” Ellis says. “We have designed all the major valves in-house and built them and started actuation tests of those. Then we’ve already built the first full engine, so it has the turbopumps and all the assembly parts put together,” he adds.
Relativity plans to finesse the engine design through a series of iterations, much of them based on the company’s extensive 3D-printing capability. “We have four different types of 3D printing for this particular engine,” Ellis says. “We had to scale up a lot of the 3D printing technology to build something this large, but we already have the block 2 design iteration, which we’re building now. So we’ll build hardware, test it, get data, build a new iteration and improve at a pretty rapid cadence.”
Blocks three, four, five and six are “all in design and in different phases of maturity right now. So by the end of block six, we should be pretty close to an engine that we could start to do qualification tests quite soon,” explains Ellis. Following initial full engine tests, Relativity expects to work toward a full-mission-duration run on the first engine by the end of this year or early in 2024.
“The data looks really good,” Ellis says. “Getting to multiple firings at full power on the thrust chamber assembly is good, and some of the combustion efficiency data is coming back at 99%. The reason for that is Aeon R is a very big version of Aeon 1. It is a new design but we’re using two turbopumps–the same as Aeon 1–and it’s still liquid oxygen, liquid methane. So a lot of the data and tools and software design tools we’ve developed for Aeon 1 are applicable to the Terran R.”
The new engine, which is 12 times more powerful than the first Aeon, therefore looks promising in tests, according to Ellis, who adds, “I’m kind of surprised we haven’t blown anything up yet! I hope we do actually–it’s kind of a good thing because it means you are learning.”
The second-stage engine on the Terran R will differ from the Terran 1 by running on sub-cooled liquid oxygen and sub-cooled methane. “The first-stage engine is sub-cooled liquid methane, but the oxygen is at its normal boiling point, so not so cool–which is all to do with how the turbopump suction margin needs to work. You don’t need sub-cooling for the first-stage engines,” Ellis explains.
The upper-stage engine also features a much bigger vacuum nozzle extension that is around 7 ft. in diameter. Comprising high temperature resistant exotic metal alloy, the part cannot easily be made using 3D printing, unlike the regeneratively cooled section of the nozzle.
The first stage will be configured with four outer fixed engines aligned underneath four landing legs, and nine center gimbaled engines. On both Terran R stages, the LOx propellant tanks are forward of the methane tanks, separated by a printed common dome. Both stages use a cryogenic helium pressurization system to enable better pressure authority when the engines are not turned on. Relativity adds the vehicle also features an in-house developed pneumatic pusher stage separation system.
The switch to helium marks another departure from Terran 1, which was designed with an autogenous pressurization system in which self-generated pressure from the gaseous propellant is used to pressurize the liquid propellant. Ellis says although the system is “meant to be simpler, it is hard to get right when you don’t have the engines turned on.” The autogenous system involves gasifying and feeding back some of the Lox/CH4.
As the Terran R is designed for reusability, there will be a long period of time when the engines are not on during the coast and descent phase. “Yet you have to maintain pressure in the tanks. So if it’s autogenous some of the oxygen and methane—since it’s in contact with a really cold propellant—will start reliquefying,” he says.