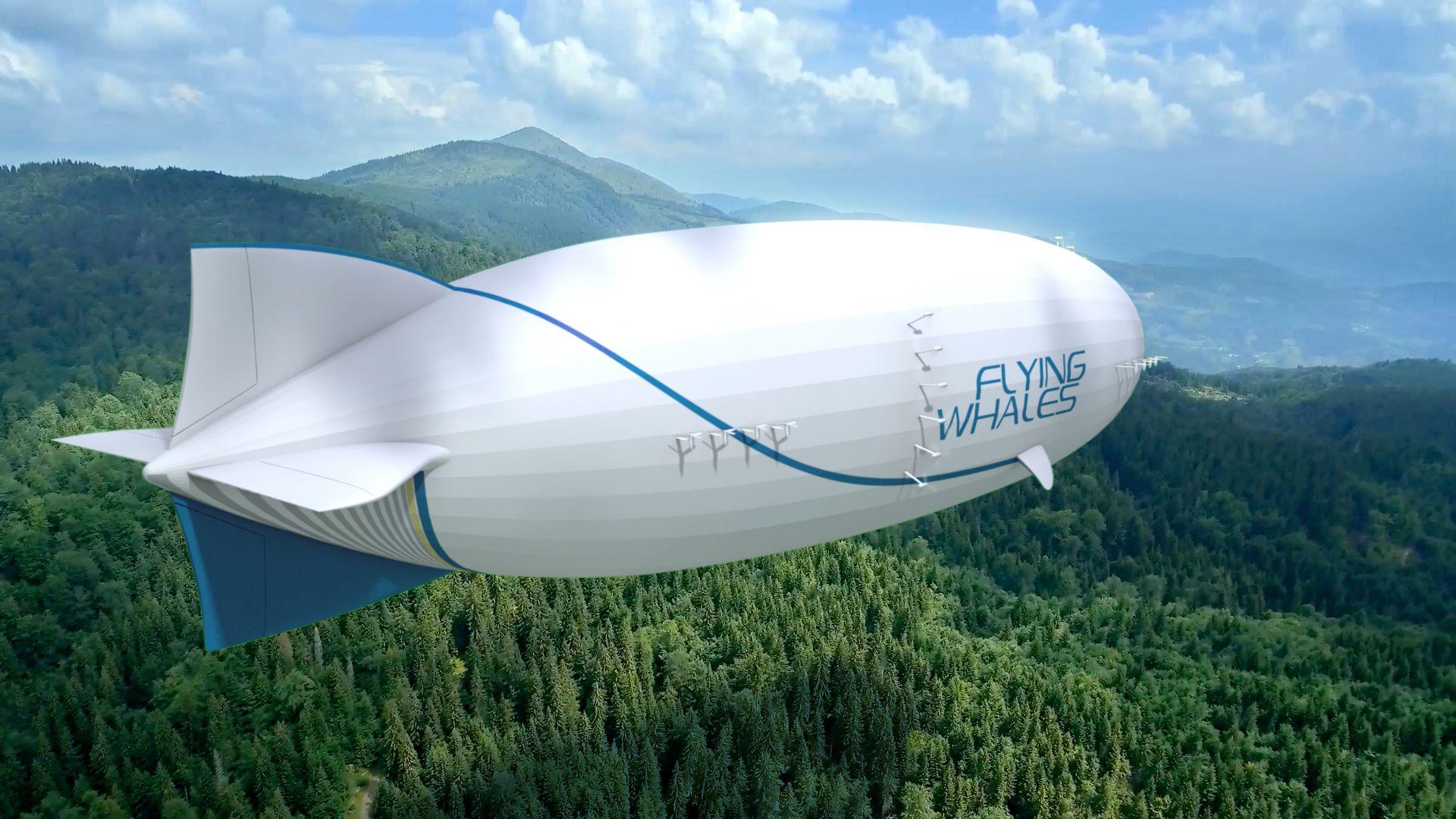
Honeywell has received a breakthrough order for its 1-megawatt generator from French and Canadian airship developer Flying Whales, which has selected the power system for its LCA60T large-capacity hybrid-electric cargo airship.
Honeywell says the generator will be integrated with a gearbox and a Pratt & Whitney Canada PT6C-based turbogenerator that will be capable of using regular jet fuel or sustainable aviation fuel (SAF). The Honeywell generator will supply power to the airship’s electric motors.
The 200-m-long (656 ft.) LCA60T rigid airship is designed to carry payloads of up to 60 metric tons (132,000 lb.) and cruise at around 100 kph (54 kt). The vehicle will be configured with a 314 ft. by 26 ft. by 23 ft. cargo bay supported by 10 non-pressurized helium cells.
The generator will be integrated into a 4-megawatt hybrid-electric propulsion system powering the vehicle’s 32 propellers. Eight will be arranged in two aft-mounted sets of four; 12 in two midship-mounted sets of six; eight in two forward-mounted sets of four props ;and four mounted fore and aft on the forward upper hull.
The LCA60T’s vectoring-thrust propulsion system is designed for vertical takeoff and landing and to maintain a stationary hover for loading and unloading over remote locations with no ground transportation infrastructure. Honeywell will provide the first generator to Flying Whales for integration and ground tests in 2024. Initial flight tests are planned in 2025.
Flying Whales will assemble the first LCA60Ts in Laruscade, in France’s Nouvelle-Aquitaine region. The company plans to produce 150 aircraft over the next 10 years. Commercial operations are due to begin in 2027 with production due to scale up following the addition of a second assembly line, planned for development in Quebec. The company also is hoping to establish a third production site in Asia.
The start-up airframer also recently selected Thales’ FlytX certifiable avionics suite and fly-by-wire flight control computer for the LCA60T. The airship will use a next-generation high-integrity, ultra-small, form-factor flight control computer, which Thales plans to develop in Quebec.
Flying Whales’ selection of Honeywell’s energy-dense generator is a key move for the power company as it seeks new hybrid-electric applications in the emerging advanced air mobility, autonomous cargo and regional markets. The 1-megawatt unit is two and a half times more powerful than the company’s first HTS900 turboshaft-based turbogenerator system announced in 2019 and builds on experience gained during development of a high-power generator for DARPA’s XV-24A LightningStrike Vertical Takeoff and Landing (VTOL) hybrid-electric X-plane.
Although the Aurora-developed XV-24A project was canceled in 2018, Honeywell continued work on the generator, which formed the design basis of the integrated 200-kW units unveiled with the HTS900 the following year. Designed to achieve an efficiency of 98%—compared with 92% for traditional aircraft generators—the XV-24A unit was packaged with five times the power density of existing megawatt-class generators to enable the high levels of power required for electric propulsion.
The 1-megawatt unit, which completed initial tests in May 2022, has run continuously at 1,000 kW and demonstrated a power density of 8 kW/kg at an efficiency level of around 97%. Dave Marinick, president of Honeywell Aerospace Engines & Power Systems, says, “Our generator is four times as powerful as any other generator flying today, and at unmatched power density.”
Honeywell’s success with the Flying Whales airship comes as rival Collins Aerospace continues development of a 500-kW electric motor that will power UK-based Hybrid Air Vehicles’ planned hybrid-electric Airlander 10 heavy-lift airship. The hybrid-electric Airlander is being pursued jointly by Hybrid Air Vehicles, Collins and the University of Nottingham, supported by more than £1 million ($1.39 million) in UK government funding via the Aerospace Technology Institute under the E-HAV1 project to build a full-scale prototype of the electric propulsor for ground testing.
The motor will produce 500 kW of continuous power at a low 2,000 rpm, enabling direct drive of the vectoring propulsor. The machine will operate at 1,000 volts DC—nearly twice the latest 540-volt standard used in aircraft.