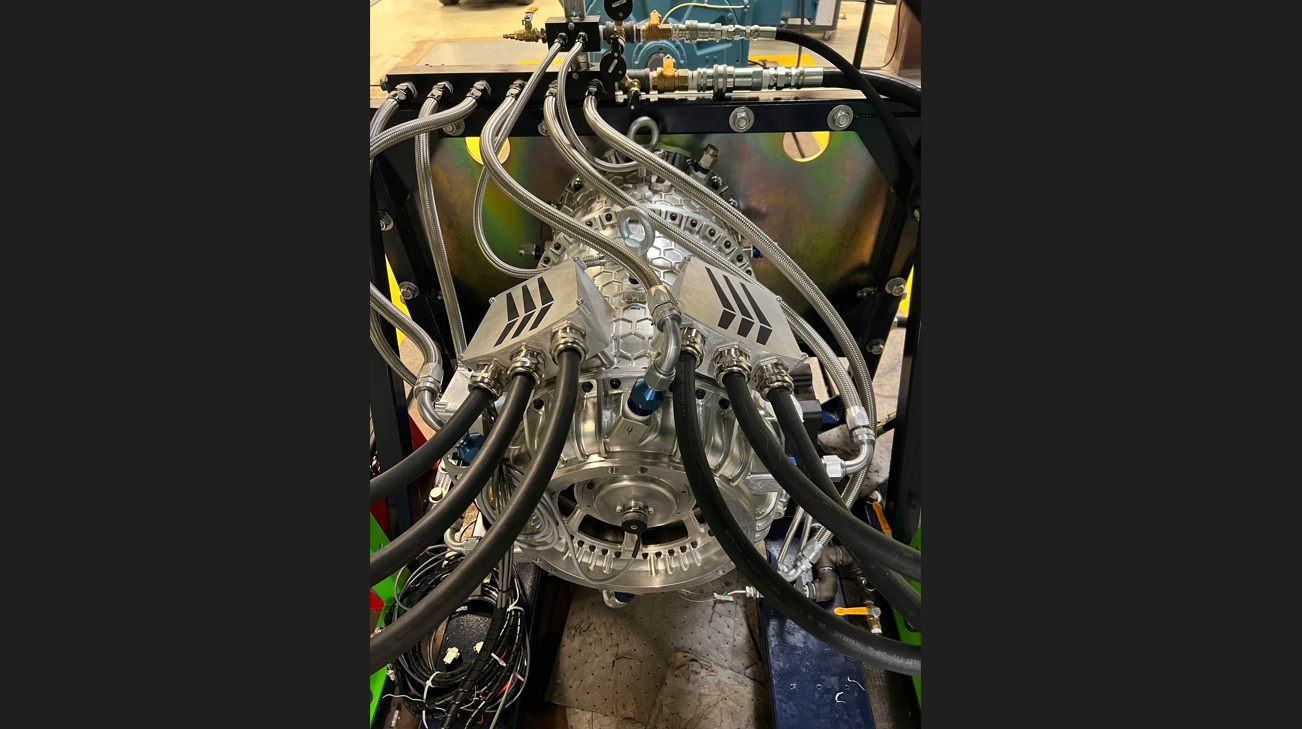
Wright’s electric propulsion motor has achieved 1 megawatt of power in bench tests.
U.S. startup Wright Electric has produced 1 megawatt of shaft power in tests of an electric motor-generator under development to power commercial aircraft.
A megawatt-class motor is widely viewed as a key building block for electrified aircraft propulsion.
The motor produced 1 megawatt of peak power on a dynamometer test stand at Wright’s facility in Albany, New York. The company has signed a Space Act Agreement with NASA to test the motor in an altitude chamber at the NASA Electric Aircraft Testbed (NEAT) in Sandusky, Ohio. The tests, up to a simulated altitude of 40,000 ft., are planned for late this year or early 2024.
“Achieving 1 megawatt of shaft power is an important step in reaching Wright’s goal of making all single-aisle flights under 800 mi. zero emissions,” Wright Founder and CEO Jeff Engler says.
“The next frontier in electric aircraft is ATR 42/72-size airliners,” he says, noting that these require from almost 1.5 megawatts to more than 2 megawatts of power per side. “We’re seeing a lot of testing at 600 kW. That’s a good demonstration, but not what is needed.”
“Our focus is on getting to the power level needed,” Engler says. Wright’s electric motor is designed to reach 2 megawatts so that a single propulsor can provide the power needed on an ATR-size aircraft.
Stacking two motors together on the same shaft would produce 4-5 megawatts, enough to power a BAe 146-size regional jet, he says. Wright is proposing to re-engine the 146, its electric motors replacing the aircraft’s four Honeywell LF507 turbofans but powering the same fans.
While using a conventional permanent-magnet architecture, the motor includes integrated power electronics and liquid cooling. To increase power and reduce weight, Wright uses high-frequency silicon-carbide inverters and “aggressive” in-slot oil cooling of the stator winding.
“In-slot cooling places the coolant adjacent to the conductors, enabling higher current loading and greater specific power. We are using oil cooling, MIL-PRF 23699, commonly used in turbine engines,” Engler says. Motor specific power is an “industry-leading” 12 kW/kg, he adds.
The 1-megawatt motor is being developed under a NASA program. An advanced 2-megawatt electric propulsion unit is being developed under an Advanced Research Projects Agency – Energy program with the goal of achieving a specific power of 16 kW/kg. Engler says this motor will support fan testing for the re-engined 146, which the company calls the Wright Spirit.