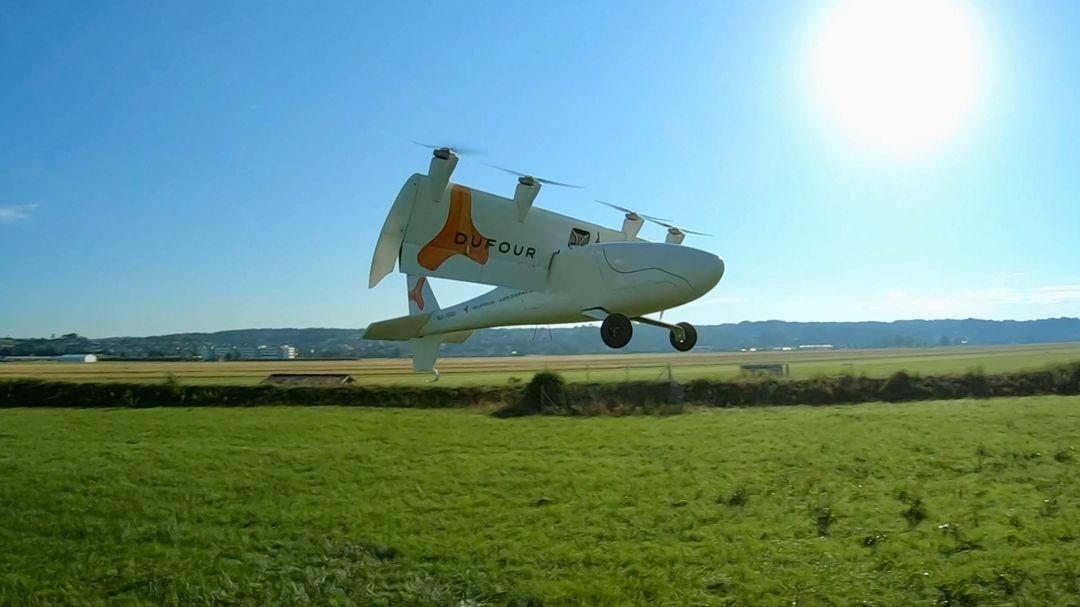
The Aero2 is designed to fly a 40-kg payload up to 400 km (216 mi.).
Tilting propellers have emerged as a leading form of propulsion for electric-vertical-takeoff-and-landing (eVTOL) vehicles, with applications including air taxis from Archer, Joby, Vertical Aerospace and Wisk, among others.
But despite their popularity, tiltrotor aircraft can be very power demanding in vertical flight mode, necessitating more powerful–and heavier–batteries and motors, which in turn limits payload and range.
For that reason, Swiss startup Dufour Aerospace has opted to build its planned family of eVTOL aircraft with tilting wings — tilt-wings —, which the company expects to produce substantial power and weight savings compared to tiltrotor designs, according to Simon Bendrey, the company’s lead engineer.
“With tilting propellers, you need to produce 20 - 30% more power than for tiltwing, and power is weight,” Bendrey tells the AAM Report. “So you need more powerful propellers, more powerful motors and more powerful batteries to provide that system, and that is weight that you can’t then sell as payload. So, from a pure efficiency perspective, the tiltwing is significantly more efficient.
“It’s also less draggy, because you’ve got less pylons and other stuff you’re carrying around,” Bendrey adds. “And from a certification basis, you’ve only got one tilting mechanism to deal with–the hinge–not six or eight different nacelles all wagging around, so the number of failure conditions you have to cover is significantly reduced.”
To be sure, tiltwing aircraft are nothing new. The concept was studied extensively in the mid-20th century, including the Canadair CL-84 and LTV XC-142, but was never commercialized [due to the winding-down of the Vietnam War and consistently poor handling and control issues during transition with the technology of the time. But Dufour believes that advances in airframe, control technologies and electric propulsion technologies have opened the door to a viable, mass-produced tiltwing eVTOL aircraft.
“We can now remove the mechanical durability issues they had in the ’60s and ’70s,” Bendrey says. “We don’t have any drive shafts or gearboxes. We have distributed lift-thrust systems for the power and software to synchronize and control everything ... 70 years on, we can now bring the tiltwing concept to life.”
For its first product, Dufour is developing the Aero2, an unmanned, hybrid-electric tiltwing VTOL aircraft designed for middle-mile cargo and logistics missions. The company in July completed initial transition flights of its X2.2 battery-powered prototype aircraft, and is currently completing a second prototype aircraft for delivery to launch customer Spright, the drone division of U.S. medical services provider Air Methods, to serve as a technology demonstrator beginning in October.
The two aircraft are planned to be followed by several X2.3 prototypes, which will be representative of the production Aero2. The X2.3 will weigh 210 kg and have hybrid-electric propulsion and a 6-m wingspan. The aircraft is designed to fly a 40-kg payload 400 km (216 mi.), or up to 1,300 km with a reduced payload of ¨10 kg.
“The Aero2 is clearly a first product that aims at the uncrewed market, and we think these use cases are currently ready to be served by a suitable product,” Chief Commercial Officer Sascha Hardegger explains. “We also believe in regional air mobility, and eventually urban air mobility [UAM], but these are a bit more down the road–at least as we talk about viable business cases.”
Launch customer Spright has ordered up to 40 Aero2s, with options for up to 100 more, to be used in transporting medical samples and specimens on time-sensitive short hops between hospitals and laboratories. The company currently operates small uncrewed aircraft systems (UAS) on such missions, but sees potential for the Aero2 to carry heavier payloads on middle-mile, longer-range trajectories, Hardegger says.
The Aero2 was originally intended as a subscale, uncrewed demonstrator for the larger, piloted Aero3, which is designed to carry eight passengers up to 1,020 km (634 mi.) at a cruise speed of 350 km/hr.
Hardegger said work on the Aero2 will lay groundwork for the eventual certification of the Aero3, including by establishing supply chain management, production processes, relationships with regulatory bodies and certification experience, in addition to providing opportunity for early revenue generation.
“Our overall ambition is to eventually build a larger aircraft that carries people, but the Aero2 allows us to work our way toward that without having to fully determine today what the market is going to demand tomorrow,” Hardegger says. “But the fundamentals of these aircraft are the same; they are not two isolated products. It’s a very natural way of learning and growing into bigger aircraft.”
The company plans to certify and begin first deliveries of the Aero2 in 2025, with the Aero3 expected sometime afterward.