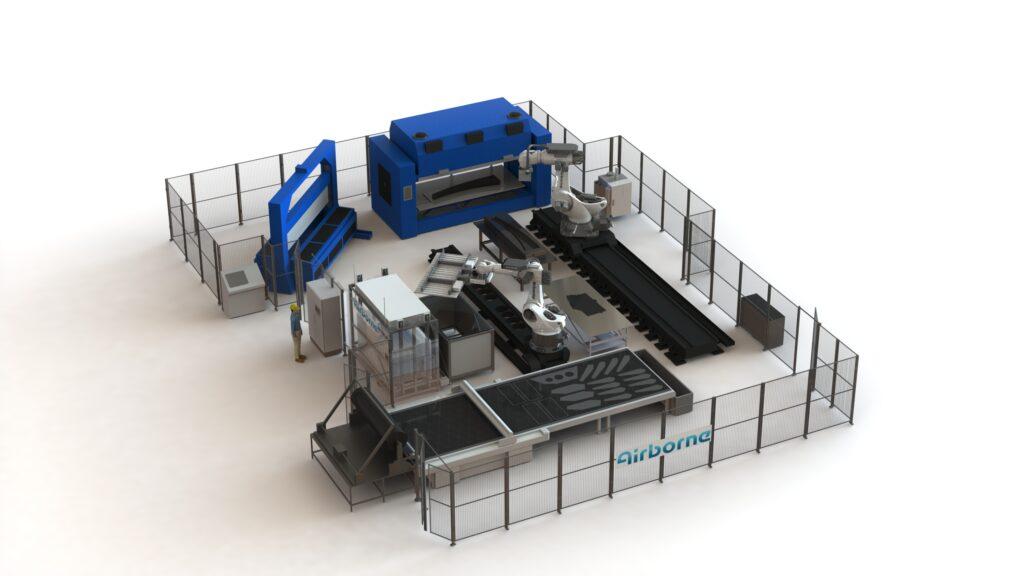
GKN will use Airborne’s automated line to produce composite preforms for resin transfer molding.
Tier 1 aerostructures supplier GKN Aerospace is leaning into the advanced air mobility (AAM) industry, seeing an opportunity to get a head start on technologies that Airbus and Boeing will need for their next generation of single-aisle airliners.
UK-headquartered GKN supplied the composite wing and empennage as well as the electrical wiring system for Eviation’s prototype Alice electric regional aircraft. GKN is supplying thermoplastic control surfaces for Joby Aviation’s S4 electric-vertical-takeoff-and-landing (eVTOL) air taxi and is also providing the wing and wiring for Vertical Aerospace’s VX4.
The company has partnered with Supernal to design and build the lightweight aerostructures and high-voltage, high-power wiring systems for the Hyundai’s subsidiary’s full-scale eVTOL technology demonstrator, which is planned to fly in 2024.
“AAM is a business opportunity. It is also a breeding ground to prove out manufacturing technologies,” says Russ Brigham, GKN Aerospace program director for AAM.
If market projections prove out, eVTOL vehicle production could ramp up to volumes not previously seen in commercial aerospace, requiring manufacturing technologies more suited to high-volume production than current certified aerospace processes.
But those same technologies are expected to be required by Airbus and Boeing as they aim to achieve high-rate production of their next clean-sheet aircraft more quickly than for previous generations in an effort to renew airline fleets more rapidly.
GKN is already advancing the next generation of manufacturing technologies with deals to accelerate certification of additively manufactured parts and automate the molding of composite parts.
The company has selected the Netherlands’ Airborne to supply a fully automated composites preforming line for its Global Technology Center in Bristol, England. The line is part of a UK government-backed project to accelerate development of composite materials and processes for aerospace and automotive supply chains to support next-generation aircraft and future mobility.
The automated line will transform composite broad goods into 3D preforms for resin transfer molding (RTM). The system will integrate an automated ply placement cell by Airborne, automated preform trimming by Accudyne Systems, ply cutter from Assyst Bullmer and a hot drape former from PAC Group.
Cut shapes can be stored in Airborne’s buffer, enabling out-of-sequence nesting of plies to minimize waste and reduce cost. Plies will be assessed using a vision system and then “pick and weld” assembled into 2D tailored blank preforms. These will be 3D formed by the hot drape former and trimmed to shape.
The automated preforming line will initially be used for the GKN-led Ascend project, which is intended to accelerate the adoption of composite technologies. Ascend is a £40 million ($52 million) project funded 50:50 by the UK government and industry.
In a second deal, GKN has signed a letter of intent with U.S. 3D printing specialist Materialise to accelerate the certification of the additive manufacturing process to produce functional and flight-critical aerostructures.
Materialise has been a supplier of polymer additive manufacturing to GKN since 2015 and supported the delivery of 3D-printed wingtips for the Eviation Alice. The collaboration will range from prototyping to production parts and the partnership will focus primarily on eVTOL aircraft.