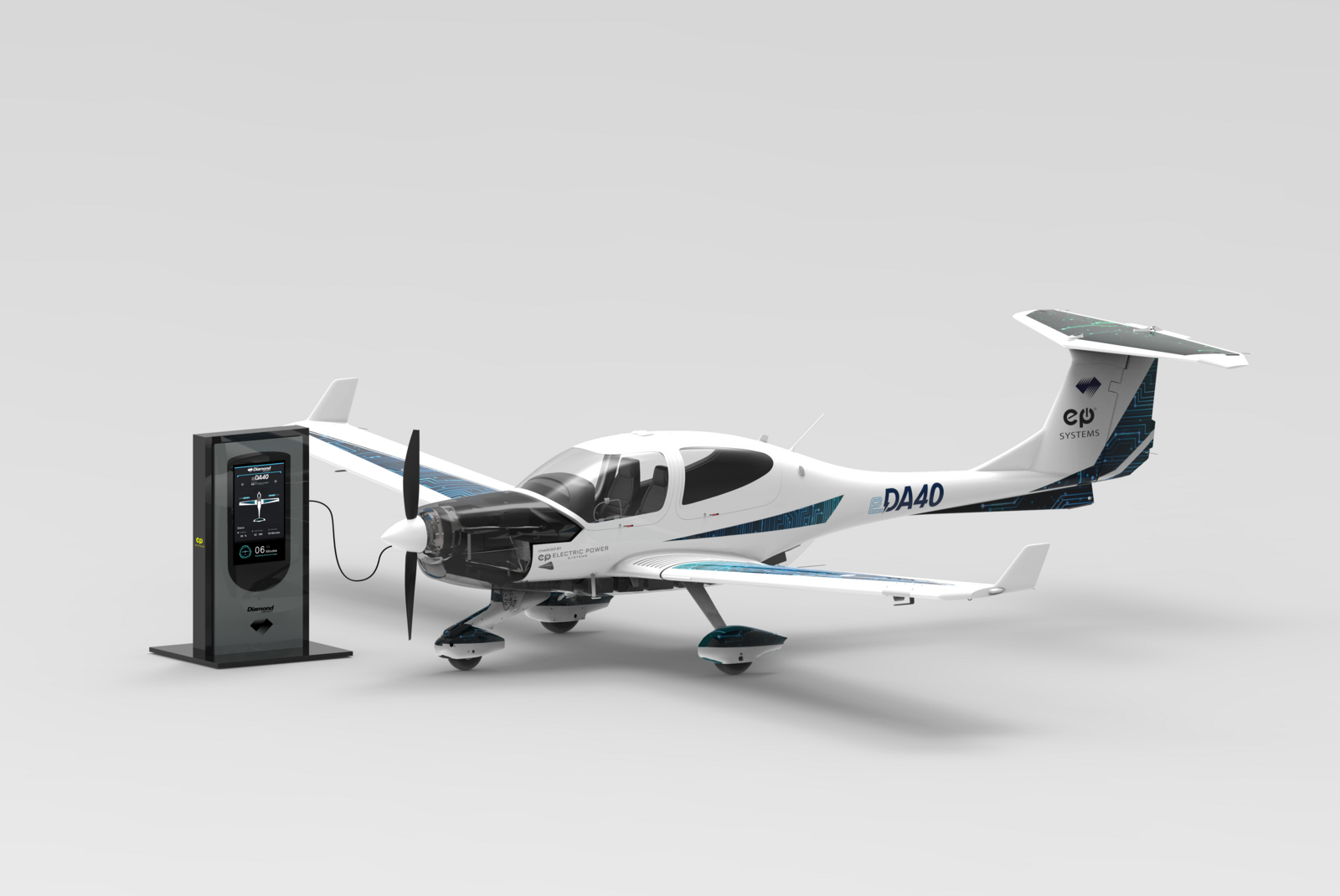
Credit: Diamond Aircraft
Diamond Aircraft is facing challenges to reaching agreement with regulators on requirements for certification of its eDA40 electric trainer. Battery safety is a key concern for certification, which is planned for 2023. The two-seat eDA40 is a derivative of the already certified four-seat, piston...
Subscription Required
This content requires a subscription to one of the Aviation Week Intelligence Network (AWIN) bundles.
Schedule a demo today to find out how you can access this content and similar content related to your area of the global aviation industry.
Already an AWIN subscriber? Login
Did you know? Aviation Week has won top honors multiple times in the Jesse H. Neal National Business Journalism Awards, the business-to-business media equivalent of the Pulitzer Prizes.