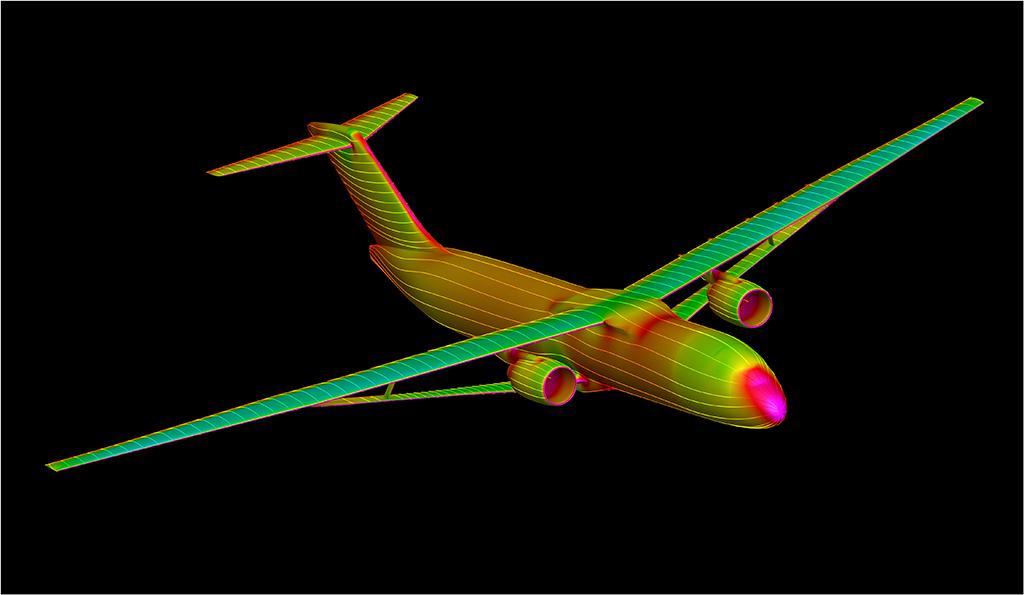
Transonic Truss-Braced Wing
The Transonic Truss-Braced Wing (TTBW) is a configuration developed by Boeing for NASA under the Subsonic Ultra Green Aircraft Research program. With a long-span, low-drag wing, braced by struts to minimize the weight penalty of the slender structure, the TTBW configuration is estimated to have a 9% fuel-burn advantage over a conventional cantilever wing. With a span of 170 ft. versus 113 ft. for a Boeing 737-800, the initial TTBW design has an aspect ratio of about 14 compared with 9.25 for the 737. NASA is proposing to build an X-plane flight demonstrator of the TTBW to fly in the mid-2020s.
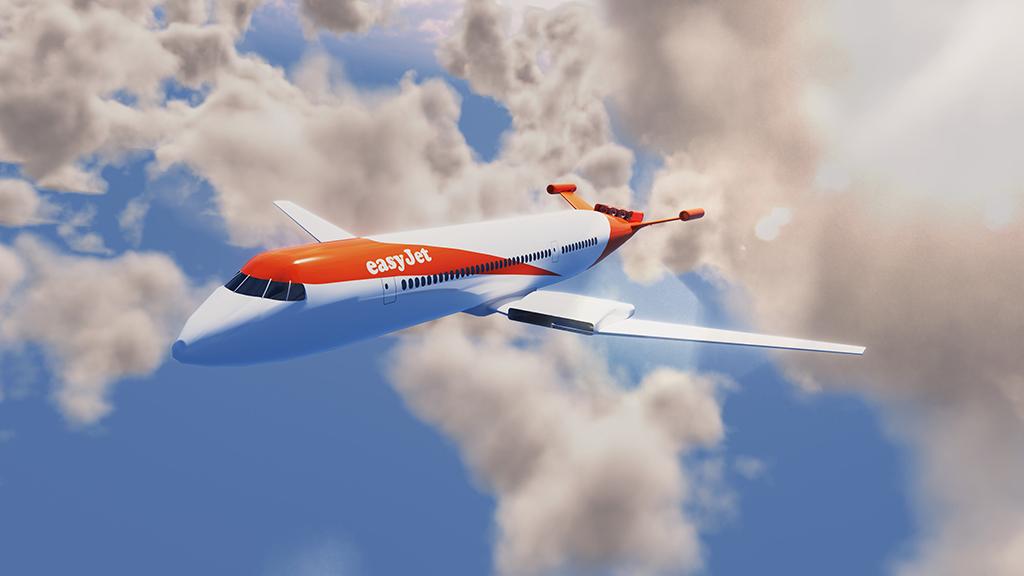
Distributed Electric Propulsion
Wright Electric is a U.S. startup working to develop a 186-seat electric-powered airliner with a range of about 540 km (290 nm) that could enter service around 2030. The company is working with low-cost carriers EasyJet and VivaAerobus to help define the aircraft. The Wright 1 would have multiple electric-driven ducted fans embedded in the wing and tail, gas-turbine range extenders mounted on the V-tails and quick-swap batteries. Wright has been working with NASA to define an electrified-propulsion flight demonstration that could involve flying its embedded ducted-fan system on a testbed aircraft.
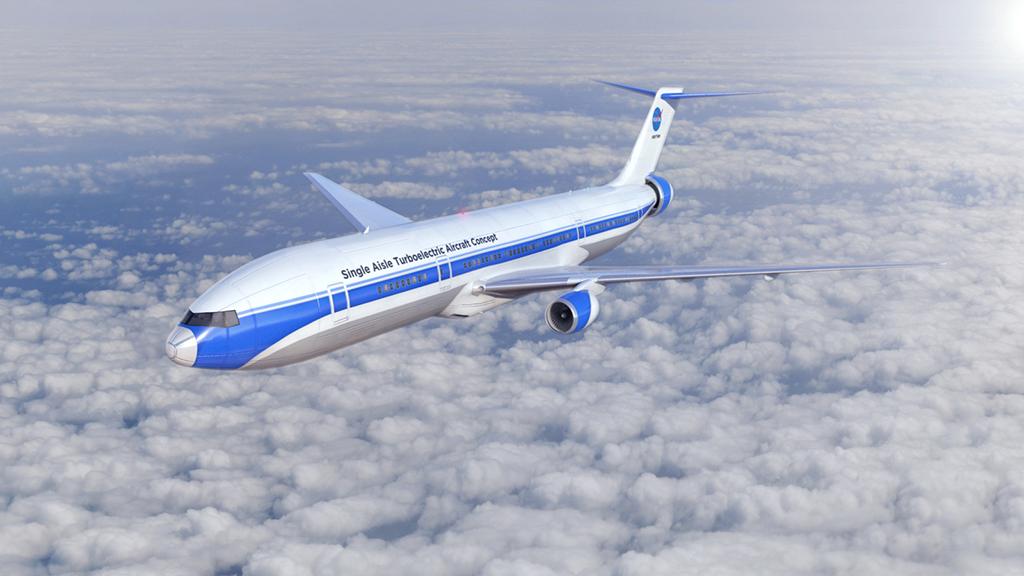
Boundary-Layer Ingestion
Several aircraft configurations have been studied that use boundary-layer ingestion (BLI) to reenergize the fuselage wake and reduce drag. These include NASA’s STARC-ABL concept, a turbo-electric airliner with wing-mounted turbans powering an electric BLI tail thruster, and the “double-bubble” D8 studied by Boeing’s Aurora Flight Sciences with its embedded engines. French research center Onera’s Nova and Airbus’ Nautilus are concepts that exploit BLI by embedding a pair of ultra-high-bypass turbofans in the rear fuselage.
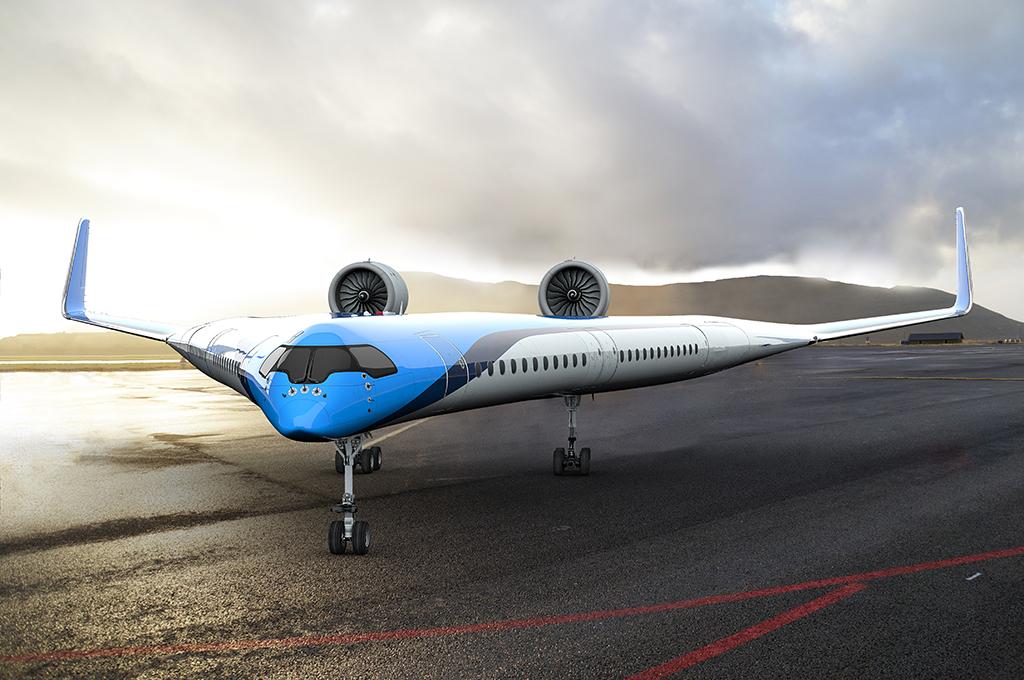
Tailless Flying Wing
Delft Technical University’s Flying-V concept for an ultra-efficient airliner uses a tailless flying-wing design. Instead of a single wide, twin-aisle cabin, the Flying-V has two Airbus A320-size single-aisle cabins integrated into the arms of the V along with the cargo holds and fuel tanks. The V-shaped aircraft has the same wingspan and passenger capacity as an Airbus A350, but is predicted to use 20% less fuel because the aircraft has less surface area, resulting in lower drag. A 4.7%-scale model was flown in 2021.
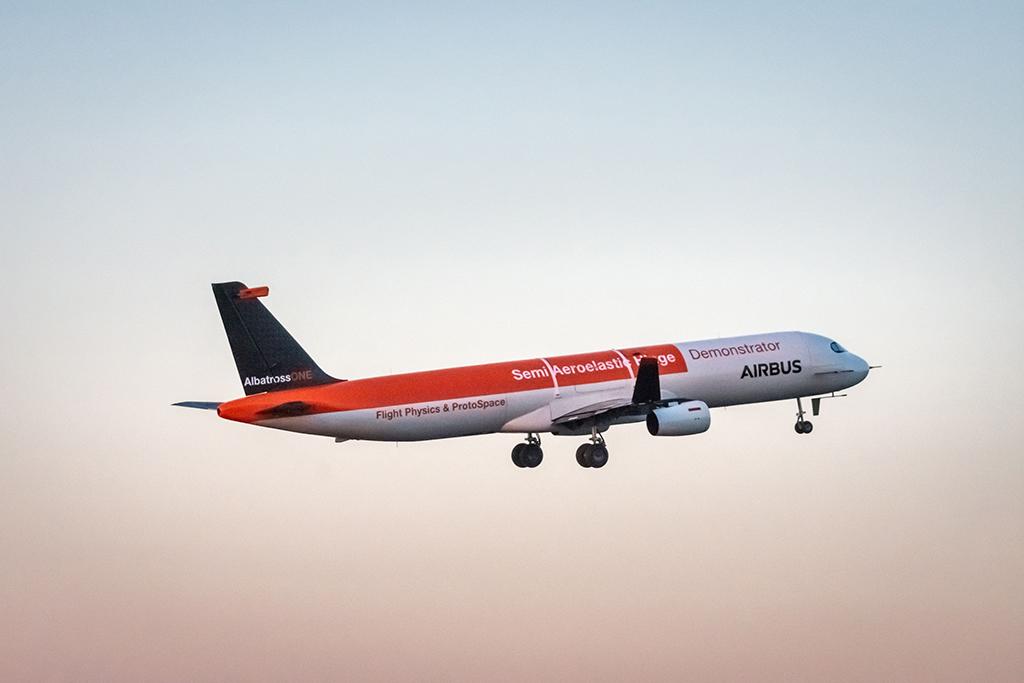
Adaptive Folding Wing
While Boeing’s 777X introduces commercial aviation to wings that fold on the ground to fit airport gates, researchers are studying the benefits of wings that fold during flight. NASA’s Spanwise Adaptive Wing uses shape-memory actuators to fold the wingtips up or down in flight to improve stability and reduce tail size. Airbus’ subscale AlbatrossOne flight-tested semi-aeroelastic hinges that allow the wingtips to flap during flight, reducing drag and gust loads on the wing and enabling a lighter, more efficient structure.
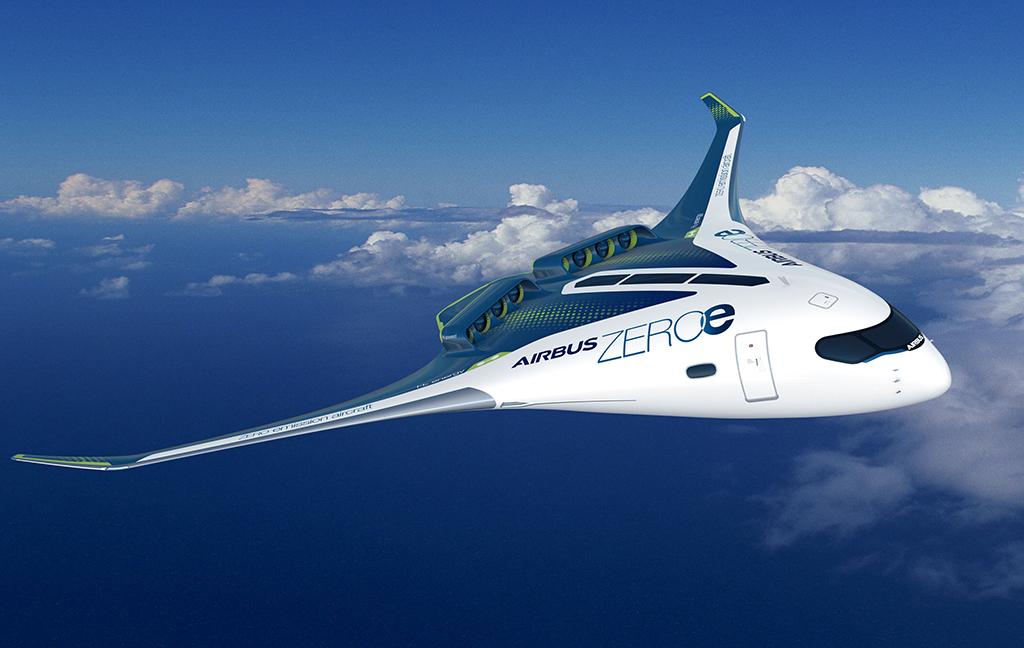
Airbus ZEROe Blended-Wing Body
As part of a broader initiative to introduce hydrogen-powered aircraft by 2035, Airbus also presented a blended-wing body concept, based on earlier studies in the configuration. The range of the proposed aircraft would be around 2,000 nm, and it would have space for around 200 passengers. Airbus argues the configuration is particularly efficient aerodynamically and offers a wide range of options for hydrogen storage and passenger cabin layouts.
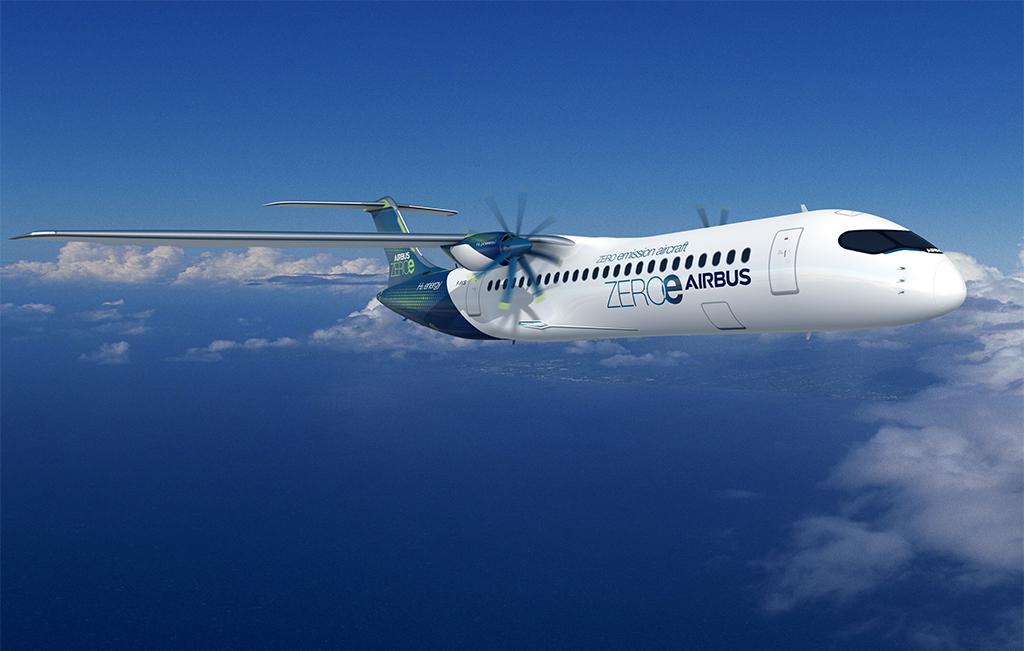
Airbus ZEROe Turboprop
Designed for flights of up to 1,000 nm for a maximum of 100 passengers, the ZEROe turboprop project layouts more closely resemble those of legacy aircraft than the blended-wing body. Hydrogen is stored in the aft fuselage. The market for large turboprops is dominated by ATR, a joint venture between Airbus and Leonardo, with the future of the de Havilland Dash 8-400 less clear. Embraer is considering launch of a large conventional turboprop around 2022 for entry into service well before the end of the decade. The ZEROe concept is to be ready by 2035.
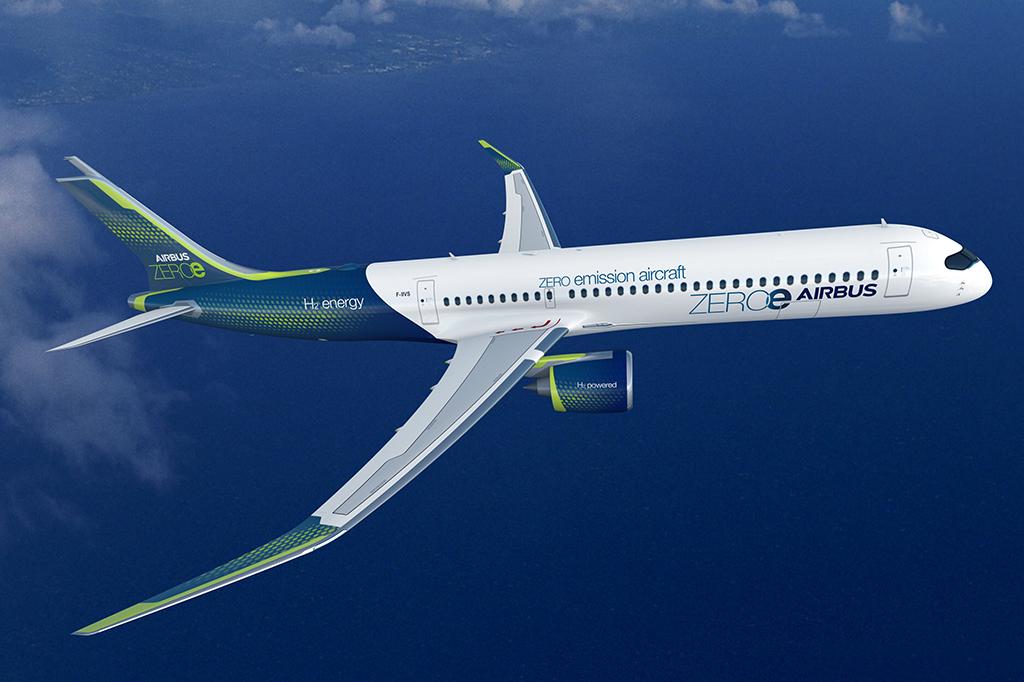
Airbus ZEROe Turbofan
Airbus is cautioning it likely will not be able to replace its current narrowbody family around the A320neo entirely with hydrogen-powered aircraft by 2035. But the technology has possible initial applications for the lower end of the single-aisle market, covering a passenger capacity of 120-200 and ranges up to around 2,000 nm. The turbofan, like the turboprop, would feature a relatively conventional fuselage that is stretched to accommodate large hydrogen tanks in the rear, modified wings and engines to adapt to the technology. French and German government funding supports Airbus’ research, which is aimed at making aviation environmentally sustainable as part of a broader push into the use of hydrogen across many industries.
The aerospace industry’s financial resources are strained as companies focus on surviving the novel coronavirus pandemic. However, many players are looking at what the next generation of aircraft could look like as governments expect major improvements in environmental performance, and as new avenues such as sustainable aviation fuels and hydrogen and hybrid-electric propulsion edge closer.